In this article, you learn what is moulding sand, types of moulding sand and their properties.
Moulding Sand And Types
The Moulding sand is also known as foundries sand, this sand is commonly used for making moulds. Natural sand located on the bed and banks of rivers gives a larger source, although high-quality silica sand is also mined.
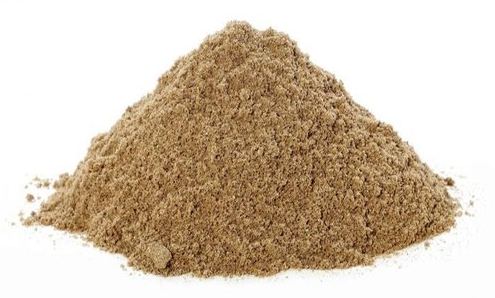
The sand is chemically Si02, silicon dioxide in a granular manner. Ordinary river sand contains a percentage of clay, moisture, non-metallic impurities and traces of magnesium and calcium salts besides silica grains. After appropriate treatment, this sand is used to make a mould.
Types of Moulding Sand
Following are the 8 different types of moulding sands:
- Greensand
- Dry sand
- Loam sand
- Facing sand
- Backing sand
- System sand
- Parting sand
- Core sand
1. Green Sand
Green sand is a sand or sandstone which has a greenish colour. it is a mixture of silica sand with 18 to 30% clay, having total water of 6 to 8%. It is soft, light and porous with clay and water furnishing the bond for green sand.
In green sand, It is slightly wet when squeezed by hand. It has the ability to maintain the shape and impression given to it under the pressure. The green sand can be easily available and it has a low cost. The mould that is prepared in this sand is called green sand mould. It is commonly used for the production of ferrous and non-ferrous castings.
Read Also:
- Heat treatment: Types, Working and Process of Heat Treatment
- Metal Casting Process: Types, Stages of Metal Casting
2. Dry Sand
The Green sand that has been dried or backed after the mould is made is called dry sand. They are suitable for large castings. Moulds prepared in dry sand are known as dry sand moulds. If we talk about the physical composition of dry sand, it is similar to green sand except for water.
3. Loam Sand
The Loam sand with 50% of clay is called loam sand. They are also suitable for large castings. It is a mixture of sand and clay and water is present in such a quantity that it forms a thin plastic paste. In these types of sand, moulding patterns are not used.
4. Facing Sand
It forms the face of the mould. The facing sand is used directly next to the patterned surface and comes into direct contact with the molten metal when the molten metal is poured into the mould. It has high strength and refractivity as it comes in contact with molten metal. It is made of clay and silica sand in addition to unused sand.
5. Backing Sand
The backing sand is also called floor sand used to back up the facing sand. It is an old and frequently used moulding sand is used for backing purpose. It is sometimes called black sand because of the addition of coal dust and burning due to in contact with the molten metal.
6. System Sand
In mechanical sand preparation and handling units, facing sand is not encountered. The sand that is used is cleaned and reactivated by adding water, binder and special additives. And the sand we get it is called system sand.
The system sand is used to fill the entire flask in the mechanical casting where machine moulding is employed. The mould made of this sand has high strength, permeability and refractivity.
7. Parting Sand
The parting sand is used to avoids sticking of green sand to the pattern. And also it allows in easy removal of cope and drag. This parting serves the same purpose as dust. It is pure clay free silica sand.
8. Core Sand
The core sand is the sand for making cores. It is also called oil sand because it is a mixture of silica sand and core oil. Core oil is a mixture of linseed oil, resin, light mineral oil and other binding materials. For the sake of economy, pitch or flour and water can be used to make large cores.
[quads id=2]
Properties of Moulding Sand
Good, well-prepared moulding sand must have the following properties:
- Refractoriness– It should be able to withstand high temperature.
- Permeability– Ability to allow gases, water vapour and air to pass through it.
- Greensand strength– When the mould is formed of moist sand, it must have sufficient strength, otherwise, the mould will break.
- Good flowability– When it is arranged around a pattern in a moulding box, it must be able to fill all nooks and corners, otherwise the impression of pattern in mould would not be sharp and clear.
- Good collapsibility– It should collapse easily after the casting has cooled down and has been extracted after breaking the mould. It is particularly important in case of care making.
- Cohesiveness– Ability of sand grains to stick together. Without cohesiveness, the mould will lack strength.
- Adhesiveness– Ability of the sand to stick to other bodies. if the moulding sand does not stick to the wall of moulding box, the whole mould will slip through the box.
That’s it, thanks for reading. If you have any question or doubts about “Types of Moulding Sand” ask in the comment section below. Share this article if it is worth sharing.
Read Next: