In this article, we will discuss what is unconventional machining process and its 9 Types of unconventional machining processes.
Unconventional Machining Process
Unconventional machining is also called non-traditional machining.
The unconventional machining used for the machine the hard and brittle materials such as carbides, stainless steel, Hastelloy, nitralloy, waspaloy, and any other that cannot be machined by a conventional process using the conventional machines such as lathe, milling, shaper, planer, etc.
These materials are widely used in the fields of the nuclear industry, space research, missile technology, and other industries that require a high strength-to-weight ratio, heat-resisting quality, hardness, and toughness.
By using conventional machining, the time taken for machining is more, and the fewer surface finishes, as well as no accuracy. Therefore by using unconventional machining, the time taken is less and the surface finish and accuracy are excellent.
The unconventional machining uses some form of energy for metal removal there is no direct contact between the tool and the workpiece. This process is also uneconomical, time-consuming, and sometimes impossible to machine complex shapes.
Read Also: Different Types of Welding Rods and Their Uses Explained
Classification of Unconventional Machining
The following are the classifications of unconventional machining:
Mechanical Machining
The process of mechanical machining involves the exact removal of unnecessary material by use of a high-velocity stream of abrasives or fluid.
Ultrasonic Machining (USM) and Waterjet Machining (WJM) are two important examples of non-traditional mechanical machining methods that use only one operation. WJM uses fluid machining, whereas USM employs solid grains.
Electrical Machining
Unconventional machining processes in electrical machining use electrical energy to remove material, as opposed to electroplating.
For example, electrochemical machining eliminates the machining allowance electrochemically by using ion transfer within an electrolytic cell.
Thermal Machining
To cut or shave the workpiece, thermal machining uses heat energy. Typically, applying heat energy to a small part of the work surface is enough to cause the material to fuse or evaporate. Electrical energy must be fully converted to produce thermal energy.
There are many different types of heat sources, including ions in IBM, photons in LBM, electrons in EBM, and plasma in EDM and PBM.
Chemical Machining
Chemical machining uses chemicals that can attack certain material components to remove material from a workpiece in a selective manner. A mask is used to shield other parts of the surface from chemical activity.
These unconventional processes are mainly categorized according to the energy type that is used to remove material. They are mechanical in character and include eroding work material using a stream moving at a high speed.
Read Also: Common Types of Welding Defects [Causes & Remedies]
Types of Unconventional Machining
Following are the different types of unconventional machining processes.
#1 Abrasive Jet Machining (AJM)
A high-velocity jet of dry air, nitrogen, or carbon dioxide containing abrasive particles (typically∼0.025mm) is aimed at the workpiece surface under controlled conditions.
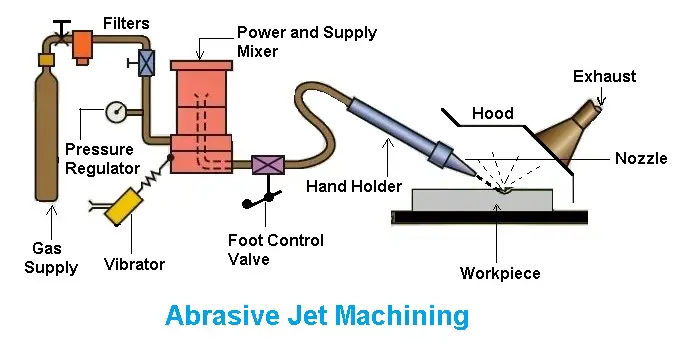
As particles impact the work surface, they cause small cracks, and the gas stream carries both the abrasive particles and the fractured (wear) particles away. The gas supply pressure is of the order of 850kPa and jet velocity can be as high as 300 m/s and is controlled by a valve.
It consists of a mixing chamber in which abrasive particles such as aluminum oxide, silicon carbide, diamond powder, and glass particles are used. Air or gas, nitrogen, or carbon dioxide is used to mix with the abrasive particles. From the mixing chamber, the mixture is supplied to the nozzle which is the high strength of a material i.e., tungsten carbide.
From the nozzle, the abrasive particles with a velocity of 150 to 300m/min are made to impact the workpiece due to the high-velocity metal removed from the workpiece with no contact with the tool.
Advantages of Abrasive Jet Machining
- It can cut hard materials such as composites, ceramics, and glass.
- Good for materials that cannot withstand high temperatures.
- The complex shape can be produced in the hard and brittle material.
- Ability to cut heat-sensitive materials.
- Low initial cost.
Disadvantages of Abrasive Jet Machining
- It is an expensive process.
- Flaring can become large.
- This process is not suitable for mass production because of the high maintenance requirement.
- the metal removal rate is slow.
- The nozzle wear rate is higher.
- Additional cleaning is necessary.
#2 Ultrasonic Machining (USM)
In ultrasonic machining, ultrasonic waves are produced using magnetostrictive effects which are converted into mechanical vibration. In this machining, the metal is removed from the workpiece by microchipping and erosion with fine abrasive grains in the slurry.
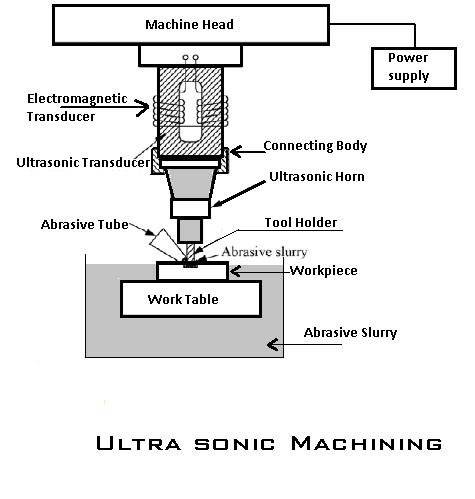
The tip of the tool vibrates at a frequency of 20kHz and low amplitude (0.0125mm – 0.075mm). The tool has the same shape as the cavity to be machined.
It consists of an electromechanical transducer which is connected to an AC supply. The velocity transformer holds the tool firmly. An abrasive gun is used to supply an abrasive slurry, which is a mixture of abrasive grains and the water in between the tool and workpiece interface under pressure.
Advantages of Ultrasonic Machining
- The workpiece after machining is free of any stress.
- Extremely hard and brittle materials can be easily machined.
- Very good accuracy and surface finish can be obtained.
- The operational cost is low.
- The process is environmentally friendly as it is noiseless without any chemical reactions and heating.
- This process is economical.
- Better efficiency can be obtained.
- It is suitable for both conducting and non-conducting materials.
Disadvantages of Ultrasonic machining
- In this, the metal removal rate is low and cannot be used for large machining cavities.
- The initial cost and cost of the tool are very high, frequency tool replacement is required as tool wear takes place in this operation.
- Not for soft and ductile materials due to their ductility.
- Power consumption is quite high.
- The slurry may have to be replaced frequently.
- The tool life is low.
#3 Electro-Chemical Machining (ECM)
In this machining, an electrolyte acts as a current carrier and a high rate of electrolyte movement in the tool and workpiece gas washes the metal ions away from the workpiece before they have to change to plate onto the tool.
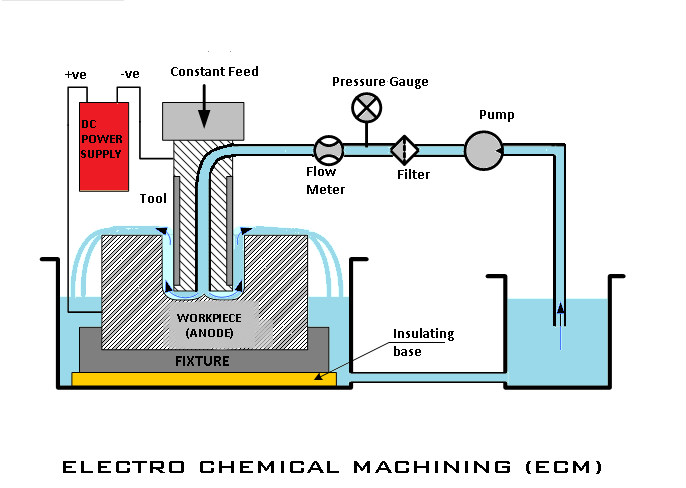
It is the reverse of electroplating. Modifications of this process are used for turning, slotting, trepanning, and profiling operations in which the electrode becomes the cutting tool. The tool is made up of brass, copper, bronze, or stainless steel. which is used to perform the work on the workpiece.
The electrolyte is a highly conductive inorganic salt solution, such as sodium chloride mixed with water or sodium nitrate. It is pumped at a high rate through the passage in the tool. A DC power supply in the range of 5 – 25 V maintains densities, which for most of the applications are 1.5 – 8A/mm² of the active machined surface.
Advantages of Electro-Chemical Machining
- Machining of hard and brittle material is possible with good quality surface finish and accuracy.
- Complex shapes can be easily machined.
- There is almost negligible tool wear, so the cost of tool-making is only a one-time investment for mass production.
- There is no use of force and no direct contact between the tool and the workpiece.
- No use of heat, so mechanical and thermal remaining stresses are absent in the workpiece.
- Very close tolerances can be obtained.
Disadvantages of Electro-Chemical Machining
- All non-conducting materials cannot be machined.
- The tool and workpiece should be chemically still with the electrolyte solution.
- Designing and making a tool is difficult but its life is long recommended only for mass production.
- The accurate feed rate of the tool is required.
#4 Electrical Discharge Machining (EDM)
Electrical discharge machining is also called electro-discharge or spark erosion machining based on the erosion of metal by spark discharges. The basic EDM system consists of the shaped tool (electrode) and the workpiece, connected to a DC supply and placed in a dielectric (electrically non-conducting) fluid.
When the potential difference between the tool and the workpiece is high, a spark discharges through the fluid, removing a very small amount of metal from the work surface. In this process the voltage between 50V and 980V and currents from 0.1A to 500A. the workpiece is fixed in the tank containing the dielectric fluid.
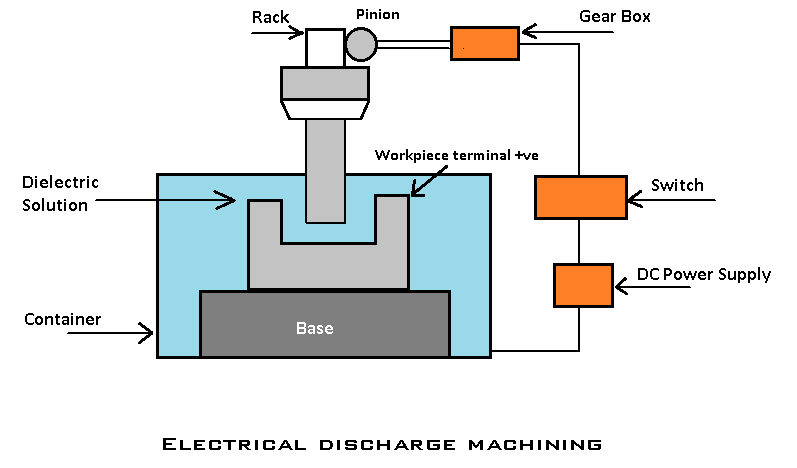
The gap between the tool and the workpiece is important, thus the downward feed of the tool is controlled by the feed mechanism, which automatically maintains the constant gap. The spark gap normally varies from 0.005mm to 0.50mm.
The most common electric fluids are minerals oil such as kerosene and distilled & deionized water is used in special applications. The present trend is the use of clear low viscosity fluids. The EDM process can be used on any materials that are an electrical conductor.
Advantages of Electro Discharge Machining
- Costlier for machining very hard material.
- Maintain a high degree of dimensional accuracy, so it is recommended for tool and die-making.
- Complex geometries can be produced.
- Highly critical sections and weak materials can also be processed without any risk of their deformation because in this process applies direct pressure on the workpiece.
- Fine holes can be drilled easily and accurately.
- The adequate form of the high value of MRR can be achieved as compared to other non-conventional machining processes.
Disadvantages of Electro Discharge Machining
- This process cannot be applied to the large-sized workpiece, as size for the workpiece is helpless by the size of setup.
- Electrically non-conducting materials cannot be processed by EDM.
- Due to the use of very high temperature at the machining zone, there are chances of deformation of the workpiece in case of these sections.
- EDM process is not capable to produce sharp corners.
- MRR achieved in EDM process is enough lower than the MRR in case of the conventional machining process, so it cannot be taken as an alternative to conventional machining processes at all.
- Redressing of the tool is required for deep holes.
#5 Electron Beam Machining (EBM)
The electron beam machining arrangement is made as shown in the figure. The cathode is made of tungsten or tantalum.
Cathode filaments are heated to a temperature of around 2500°C, which leads to the thermo-ionic emission of electrons, which is further increased by maintaining a very low vacuum within the chamber.
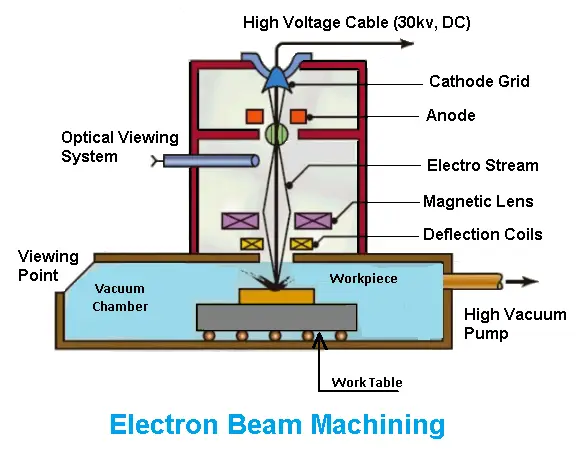
Just after the cathode, there is a grid. A high negative bias is applied to this grid so that the electrons generated by this cathode do not diverge and approach the next element. The anode which is in the form of a beam attracts the electron beam and gradually gets accelerated.
Advantages of Electron Beam Machining
- EBM provides very high drilling rates when small holes with large aspect ratio are to be drilled.
- It can machine almost any material irrespective of their mechanical properties.
- Work holding and fixturing cost is very less because of the absence of mechanical cutting force. So, fragile and brittle materials can also be processed.
- Heat affected zone in EBM is less due to shorter pulse.
- EBM can provide holes of any shape by combining beam deflection using electromagnetic coils with high accuracy.
- It is a fast process.
- Utilizing the CNC table for the machining.
Disadvantages of Electron Beam Machining
- The high cost of the equipment and necessary regular maintenance applicable to any equipment using the vacuum system.
- A valuable amount of non-productive pump down period for attaining the desired vacuum.
- Only small cuts are possible.
- A hole shape is affected by the depth of the workpiece.
- It requires a highly skilled operator.
#6 Laser Beam Machining (LBM)
A laser is an optical transducer which converts the electrical energy into coherent light. Laser stands for “light amplification by stimulated emission of radiation”.
The laser being coherent or consistent in nature a specific property to generate high power density. The laser is man-made ruby crystal, containing chromium or Aluminium oxide. LBM uses the light energy of a laser beam to remove material by vaporization and ablation.
In this process, the coherent or consistent light beam is focused optically for a particular period of time.
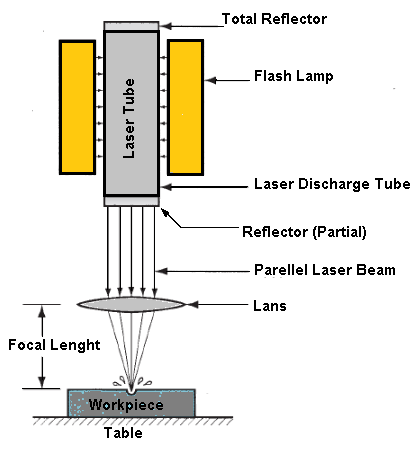
The beam is pulsed so that the released energy results in an impulse against the work surface that does melting and evaporation. In this process, the metal removing is the same as that of the EDM process but the method of generation of heat is different. The application of heat is very focused in case of LBM as compared to EDM.
The LDM setup consists of a laser tube, a pair of reflectors, one at each end of the tube, a flash tube or lamp, an amplification source, a power supply unit and a cooling system. This whole setup is fitted inside an enclosure, which carries good quality reflecting surface inside.
Advantages of Laser Beam Machining
- Materials which cannot be machined by conventional methods are machined by LBM.
- There is no tool, so no tool wear.
- Application of heat is focused, so rest of the workpiece is latest affected by the heat.
- Precise holes and cavities are obtained.
- Metals and non-metals can be machined.
- Micro-drilling is possible.
- Rubber and plastics can be machined.
- No tool wear.
Disadvantages of Laser Beam Machining
- Initial cost and operating cost is high.
- Recommended for some specific operations only, as the production rate is very slow.
- Cannot be used for high light reflecting materials.
- A highly skilled operator is required.
- The efficiency is low.
- Used for thin materials only.
- The materials removal rate is slow.
Difference Between Conventional and Unconventional Machining
The table below shows the difference between traditional and non-traditional machining processes.
Aspect | Conventional Machining | Unconventional Machining |
---|---|---|
Material Removal Method | It is usually mechanical cutting or abrasion. | It includes various approaches such as chemical, thermal, electrical, or mechanical. |
Heat Generation | It produces significant heat, which can cause thermal damage in some situations. | Heat generation is usually low, lowering the possibility of thermal damage to the workpiece. |
Tool | Cutting tools are often built of either high-speed steel or carbide. | There is no one tool; they can vary greatly depending on the process (for example, electrodes, abrasive particles, and chemicals). |
Material Suitability | It is useful with typical engineering materials such as metals, polymers, and ceramics. | It can be applied to a broader range of materials, including heat-sensitive and difficult-to-machine materials. |
Cutting Speed | Generally, it has slower cutting speeds. | Cutting speeds might vary greatly based on the particular unconventional process. |
Precision and Accuracy | Excellent precision and accuracy, making it ideal for high-precision applications. | It can be used in precision machining and microfabrication due to its great precision and accuracy. |
Surface Finish | It creates a good surface finish but might need more finishing steps. | It can produce a good surface finish without any further procedures. |
Tool Wear | Tool wear is a common problem that needs regular tool replacement or sharpening. | Minimal tool wear reduces the requirement for regular tool replacements. |
Advantages of Unconventional Machining
- It has a high degree of accuracy.
- It provides a great surface finish.
- The complex shapes can be easily machined.
- It has a higher tool life.
- The metal removal rate is high.
Disadvantages of Unconventional Machining
- This process has a higher cost.
- It requires high operator skills.
- It is complicated in setup.
Download PDF of this article
Conclusion
So now, we hope that we have clear all your doubts. If you have still any doubts about the “Types of Unconventional Machining Process” you can contact us or ask in the comments.
That’s it thanks for reading. If you like our article, then please share it with your friends.
Subscribe to our newsletter to get notified when we upload new posts.
Read more:
- What is TIG & MIG Welding: Difference Between TIG and MIG welding
- What is Welding? How it works? [Short and Complete Guide]
- 26 Essential Welding Tools and Equipments [Pictures & PDF]
External Links and Referances:
this has been helpful. thanks.
please what process variables do we consider during ECM and their effects?
Certainly! Key variables in ECM include electrolyte composition, current density, voltage, electrode material, gap distance, feed rate, electrolyte flow rate, tool design, temperature, polarity, and tool wear compensation. These variables impact material removal rate, surface finish, accuracy, and overall process stability.
how can i get those notes about un conventional machining types
download link
The PDF file has been sent to your inbox.
Thanking you sir
You’re welcome.