In this article, we are discussing TIG and MIG welding. Its Advantages, Disadvantages, Applications, and Difference Between Tig and Mig Welding are explained with pictures.
And also, you can download the PDF file of this article at the end of it.
What is TIG and MIG welding?
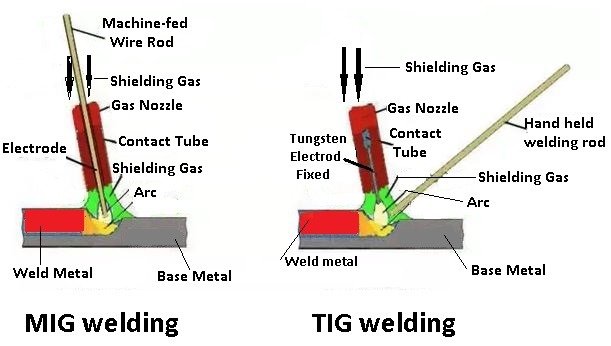
The difference between TIG and MIG welding is that MIG uses continuous feeding wire, and TIG uses welding rods that slowly feed them into the welding place.
Both TIG and MIG welding uses an electric arc to make the weld. With the help of MIG welding, you can weld various materials such as stainless steel, mild steel, and aluminum. On the other hand, tig welding is more commonly used for thinner gauge materials.
Read more: Different Types of Welding Processes & Their Uses [PDF]
Watch Slideshow Of This Post:
Let’s discuss both TIG and MIG welding one by one.
Tungsten Inert Gas Arc Welding (TIG)
TIG welding TIG stands for tungsten inert gas arc welding. From the American welding society, it is also known as (GTAW). The TIG stands for tungsten inert gas welding. This welding process is also called gas welding.
It is a welding process in which heat is produced by an electric arc ignited between a base metal (workpiece) and the non-consumable tungsten electrode.
TIG welding uses a tungsten electrode because tungsten has a high melting point. When the tig weld electrode gets hot but doesn’t melt, it is a non-consumable electrode. The non-consumable electrode doesn’t mean it lasts forever that just means that it doesn’t melt and become a part of the weld.
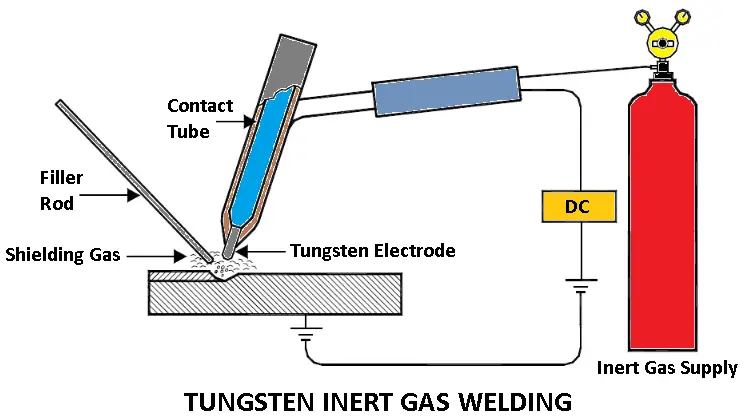
- The weld pool is shielded by an inert gas (Helium, Argon, Nitrogen), protecting the molten metal from atmospheric contamination.
- For most metals, the current is direct current or DC.
- The heat generated by the arc melts the workpiece edges and joins them.
- In tig welding, you can control the amount of heat by pressing a foot pedal or thumbwheel on the torch.
- If required filler rod may be used.
- It produces a high-quality weld of most metals.
- Flux is not used in the process.
Read more: What is Underwater Welding and types of Underwater welding?
Metal Inter Gas Arc Welding (MIG)
MIG welding is an arc welding process. MIG stands for metal inert gas welding. This MIG welding process is also known as gas metal arc welding (GMAW) you might also call wire welding.
In this welding, a thin wire acts as the electrode fed from a spool mounted on a gun through a flexible tube and comes out of the nozzle on the welding gun or torch. The wire is fed continuously when the trigger on the welding gun is pulled.
An electric arc forms between this wire electrode and the workpiece and heats both metals above their melting point these metals mix and solidify to join the workpieces into a single piece. The metal in these parts to be joined calls as the base metal. Here, the metal from the melting wire electrode is filler metal.
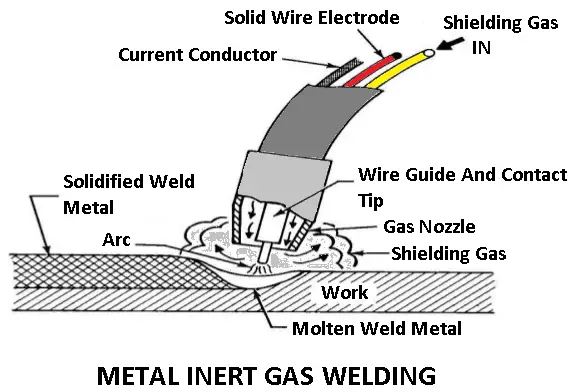
MIG welding uses filler metal for the joint. Because the wire electrode melts as it’s being used. These types of electrodes are called consumable electrodes.
- It is the arc welding process, in which the weld is shielded by an external gas such as argon, helium, CO2, and argon+oxygen.
- It has consumable electrode wire with a chemical composition similar to the parent material, continuously fed from a spool to the arc zone.
- The arc heats and metals both the workpiece’s edges and the electrode wire.
- The fused electrode material is supplied to the surfaces of the workpieces, fills the weld pool, and forms joints.
- Due to the automatic feeding of the filling wire (electrode), the process is considered semi-automatic.
- The operator can control only the torch positioning and speed.
Advantages and Disadvantages of Tig and Mig Welding
Advantages and Disadvantages of Tig Welding
TIG welding, also known as tungsten inert gas welding, is a flexible method that can join a variety of small and thin materials by using a non-consumable tungsten electrode and an optional, separate filler rod.
Because TIG welding takes longer than MIG welding, production times and costs are increased as a result. TIG welding is more difficult for beginners and needs experienced operators to produce the proper weld with precision and accuracy.
However, TIG welds are stronger, more accurate, and more aesthetically pleasing than MIG welds because TIG offers greater control over the welding process.
Advantages and Disadvantages of Mig Welding
Metal inert gas welding, or MIG, uses consumable wire as both the electrode and filler material to join large and thick materials. MIG welding is quicker than TIG welding, which results in quicker weld production and lower costs. Because it is simpler to learn, it is also simpler to create welds that require little to no cleaning and finishing.
However, MIG welds are not as accurate, durable, or aesthetically pleasing as those made by an experienced TIG welder.
You might like: What Are The Uses of Aluminium? [Complete Guide] PDF
Tig and Mig Welding Comparison Table
Following are the common comparison of tig and mig welding:
Benefits | Tig Welding | Mig Welding |
---|---|---|
Welding Speed | High speed operation is impossible for tig welding. | The Mig welding process can work quickly. |
Welding Costs | Tig welding doesn’t cost all that much. | Mig welding is more expensive. |
Ease of Welding | Tig welding requires a lot of skill. | It is simple to perform mig welding. |
Strength of Weld | Tig welding has a high weld strength. | The lifespan of mig welding is limited. |
Weld Precision | Welds made using tig welding are extremely precise. | The mig welding process has poor precision. |
Weld Aesthetics | The tig welding process produces high-quality welds. | The mig welding technique has poor weld aesthetics. |
Thick Materials | Thick materials can’t be welded with tig welding. | Thick materials can be easily welded with mig welding. |
Thin Materials | Thin materials can be easily welded using tig welding. | Thin materials are difficult to weld with mig welding. |
You might like: Difference Between Brazing and Soldering [Explained]
Application of Tig and Mig Welding
Tig Welding
Compared to MIG welding, TIG welding is more challenging to learn but offers a more precise result than MIG welding. TIG can be used to weld a variety of materials, including titanium, copper, steel, and aluminum.
It is better for joining thinner materials, as we already said in the above table. TIG welding is therefore frequently used in fields where accuracy is necessary, including aerospace, motorsport, industrial structures, manufacturing on a production line, and more.
Mig Welding
MIG welding is appropriate for a variety of applications because it is simple to learn, relatively easy to execute, and capable of joining materials like aluminum, mild steel, and stainless steel. This type of welding is frequently used when weld aesthetics are not a concern and is especially effective for thicker metals.
You might like: Properties of Steel Explained [Definition & Characteristics]
Main Difference Between Tig and Mig Welding
I’ve already discussed some of the differences between the MIG and TIG welding processes above.


MIG welding is often considered as being quicker and better for joining thick materials, as well as being simpler to learn and execute. TIG welding, on the other hand, provides greater control and precision, works better with thinner materials, and produces cleaner welds with less finishing needed.
In addition to these fundamental differences, the following major differences can be grouped according to various characteristics, price, ease of learning, and other factors:
#1 Weld Strength
The joints made by TIG welding are typically more durable than those made by MIG welding. This is due to the fact that the metal can be penetrated more effectively by the TIG welder’s focused, narrow arc.
Further, TIG weld beads do not contain many holes or other defects that can weaken a weld when applied correctly.
In spite of this generalization, MIG welds can still produce good penetration with strong welds when a V-shaped groove is ground or cut into the joint before welding. MIG welds will be stronger if the torch is positioned correctly and the travel speed is good.
#2 Welding Speed
In a manufacturing environment, MIG welders generally provide faster welding speeds. This is because air-cooled MIG welders have wider, rounder arcs that better eliminate heat and automatically feed filler material into the weld pool.
This prevents welders from overheating and enables them to move the weld puddle more quickly over longer runs. TIG welders, on the other hand, are unable to match MIG welding speeds in terms of moving the weld puddle quickly or providing enough filler rods.
In addition, air-cooled torches used in TIG welding become too hot during long welding runs, requiring cooling or replacement with more expensive water-cooled torches.
You might like: Different Types of Casting Defects [Their Causes & Remedies]
#3 Shielding Gas
During Tig and Mig welding, shielding gases are used to ensure a quality weld. The shielding gas shields the weld puddle from reactive air gases that could result in weld impurities. The tungsten electrode used in TIG welds is more sensitive to reactive gases like oxygen or CO2, so pure argon gas is typically used to protect the weld.
In order to stabilize the arc and improve penetration, MIG welds are typically performed with a mixture of argon and carbon dioxide (typically 75/25%). Depending on the application, there are variations from these standard shielding gas guidelines.
TIG welding occasionally uses a mixture of argon, helium, hydrogen, or nitrogen, whereas MIG welding uses 100% pure argon when welding aluminum and can use 100% pure CO2 to reduce costs and improve weld penetration.
Also, the two methods employ different shielding gas flow rates, with MIG welding typically requiring 35 to 50 cubic feet per hour and TIG welding requiring 15 to 25 cubic feet per hour.
#4 Weld Aesthetics
In comparison to MIG welds, TIG welds often display superior aesthetic qualities. TIG welds only need light polishing to finish and get rid of any discoloration because there is little to no spatter.
The TIG process often results in the most pleasing welds and can enhance the appearance of unpainted welds (in steel or aluminum, for example). MIG welds, in contrast, have a less appealing appearance, though a skilled welder can still produce attractive MIG weld beads.
Despite the differences in appearance, MIG welds are suitable for applications where aesthetics are not as critical or where the welds will be coated, masking the joint’s appearance.
You might like: Types of Forging Defects [Their Causes & Remedies]
#5 Process Difficulty
Learning and mastering MIG welding is much simpler than TIG welding. A TIG welder needs two hands, one for moving the welding torch and the other for feeding the filler rod into the weld pool. In addition, you usually have a foot pedal to control the amperage.
These various motions can be difficult to learn even though they give you more control. Welders typically observe TIG welds as a more advanced process, and the metals to be joined must also be thoroughly cleaned and prepared.
On the other hand, MIG welding is much simpler to learn. You only need to use one hand to complete the weld because there is no foot pedal to learn and the filler material is automatically fed through the welding gun.
#6 Cost of the Weld
Compared to MIG welding, TIG welding has a higher price per foot of beads. Due to TIG’s lower deposition rates and the need for more experienced welders, the price is higher. TIG welding involves more initial preparation, which also raises the price.
The cost of MIG welding equipment and supplies is typically lower than TIG. TIG welding is more expensive than MIG welding due to a combination of all these factors.
You might like: Different Types of Flanges and Their Applications
Selecting the Right Welding Process for Your Application
Making the choice between MIG and TIG welding can be challenging due to the differences between the two welding techniques.
The advantages of each technique can be used as a guide when selecting one.
For Tig Welding
- Because of its accuracy and precision, TIG welding is perfect for joining thin materials that could warp or burn through.
- For short runs, TIG welding works best.
- TIG welding is a difficult process to manage when not in position, so the best results are obtained when working on a bench or in a shop.
- When the appearance of the final weld is crucial, TIG welding is preferred. TIG welding improves the appearance of visible items like artwork or automotive restoration while also providing better control to avoid warping or burning.
- TIG welding is often utilized by skilled welders to work with non-ferrous metals like aluminum, copper, stainless steel, and others.
- Having an experienced welder is essential for TIG welding, otherwise, it is better to opt for a simpler method, such as MIG welding.
For Mig Welding
- Thick metals can be joined more effectively with MIG welding.
- Compared to TIG welding, MIG welding is better for longer runs because it requires fewer stops and starts to replace filler material, which reduces the possibility of weld defects.
- Since MIG welding only needs one hand, it is simpler to use in awkward positions.
- MIG welding, which is a faster process than TIG welding, is more suited to high levels of productivity.
- MIG welding is simpler to master than TIG welding, making it more suitable for beginner welders.
Conclusion
So now, we hope that we have cleared all your doubts about TIG and MIG welding. If you still have doubts about the “Difference Between TIG and MIG welding,” you can contact us or ask in the comments. If you like our article, then please share it with your friends.
Subscribe to our newsletter to get notifications of our new posts.
Download PDF of this article:
For more welding knowledge, visit: weldnotes.com, www.millerwelds.com
You may be interested in reading this article on machines:
- Different Types of Welding Machines & Their Functions
- 16 Types of Welding Defects [Causes and Remedies] PDF
- 5 Different Types of Welding Positions [You Know Must]
Frequently Asked Questions
MIG (Metal Inert Gas) welding is an arc welding method that utilizes a continuous solid wire electrode that is heated and fed via a welding gun into the welding pool.
The Tungsten Inert Gas (TIG) welding process, also known as Gas Tungsten Arc Welding (GTAW), uses tungsten electrodes to make welds.
It is difficult to say whether TIG is more effective than MIG because it is dependent on a variety of factors. If properly performed by an experienced welder, TIG offers greater weld strength and better aesthetics; however, if the welder is less experienced, MIG welding may be more suitable for a quality weld. Also, MIG welding is a quicker process than TIG welding, enabling longer runs to be finished more quickly.
In conclusion, TIG is more effective in some situations while MIG is superior in others.
There are a number of reasons why TIG welding is considered to be more difficult to master than MIG welding, including the fact that it is less automated and demands greater precision than MIG welding.
While stick welding is frequently regarded as the best process for newbies, MIG welding is a better choice than TIG welding as a starting point for learning the fundamentals.
i need the pdf file for reference. great explanation for me as a beginner.
Thanks for your feedback. The PDF file has been sent to your inbox.
I interest welding book
Thanks for reading.
One major difference between mig welding and tig welding is that Mig welding is cheaper than Tig welding and also mig welding works faster than tig welding.
Thanks 🙂
Please I need the PDF file
The PDF file has been sent to your inbox.
I thoght you dont use CO2 in MIG or TIG, couse CO2 is an active gas, rather for MAG.
yes, you are right CO2 is active gas primarily used for MIG welding most metals except MIG brazing and aluminium. Using CO2 produces a cooler, more spattery arc, and slightly harder weld deposit. If active gas used for tig the raised arc voltage increase hole blows and cause excessive burning of the tungsten electrode.
That’s good to know that you could get a continuous weld with a MIG welder. I would think that would be a good way to make it a bit easier. I’ll have to consider getting an automatic one and see if it would be something that I would want to invest some time in.
I like to have both tig and mig weld