In this article, you’ll learn what are Welding Defects? How do they occur? what are the causes and remedies for the welding defects? at the end download the PDF file of this article.
What is Welding Defect?
Welding defects are formed in welding work due to the weak or poor technique used by inexperienced or untrained welders or due to structural problems in the welding operation.
Or you can say, in a welding process, the size and shape of the metal structure are varied. It is maybe due to the incorrect welding process or the application of the incorrect welding procedure.
An ideal weld or good weld must be one that exists with good penetration with sufficient fusion between the filler metal and the edge preparation.
You can read also about different welding processes like plasma arc welding, laser beam welding, resistance welding, gas welding, and arc welding you can check them out by clicking on them.
For this article, let’s discuss the types of welding defects that appear while welding.
Types of Welding Defects
Following are the types of welding defects:
- Porosity and Blowholes
- Undercut
- Weld crack
- Incomplete fusion
- Slag inclusion
- Incomplete penetration
- Spatter
- Distortion
- Hot Tear
- Mechanical damage
- Misalignment
- Excess reinforcement
- Overlap
- Lamellar tearing
- Whiskers
#1 Porosity and Blowhole
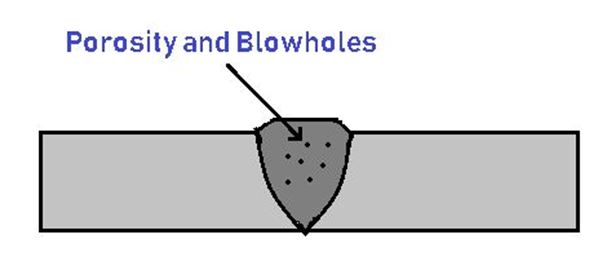
Porosity is a group of small bubbles and blowholes are relatively large hidden holes or pores. They are mainly caused by trapped gases. Porosity is a result of weld metal contamination.
Causes and Remedies of Porosity
Causes of Porosity | Remedies of Porosity |
Using insufficient electrode deoxidant. | Choosing suitable electrode and filler materials. |
Applying too large a gas flow. | Checking the gas flow meter and ensuring that it is adapted as needed with appropriate pressure and flow settings. |
Using a larger arc. | Make sure that the arc distance is correct. |
Existence of moisture in the process. | Cleaning the metal before starting the welding process. |
Unsuitable gas shield. | Decreasing welding speed, it will allow the gas to escape. |
Dirty job surface i.e. the occupation of scales, rust, oil, grease, etc. on the surface of the job. | Individual cleaning and prevention of pollution from entering the weld zone. |
#2 Undercut
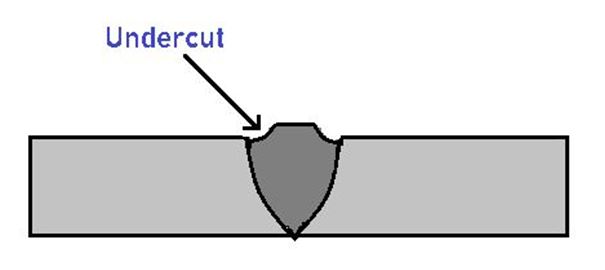
Undercut in welding makes imperfection, it is the formation of grooves in the weld toe, which decreases the cross-sectional thickness of the base metal. As a result of this weld and workpiece get weakened.
Causes and Remedies of Undercut
Causes of Undercut | Remedies of Undercut |
Incorrect use of angle, which will deliver more heat to the free edges. | Using of suitable electrode angle, with more heat delivered towards thicker components. |
Because of too fast weld speed. | Decreasing the travel speed of the electrode, but should not be too slow. |
Using poor welding methods. | Applying the multipass technique. |
Use of incorrect gas shielding and filler metal. | Select the shielding gas with the right structure for the material you are welding. |
Doing too high weld current. | When approaching thin areas and free edges, use an appropriate stream to reduce them. |
Using larger diameter electrodes. | Decreasing the arc length. |
#3 Weld Crack
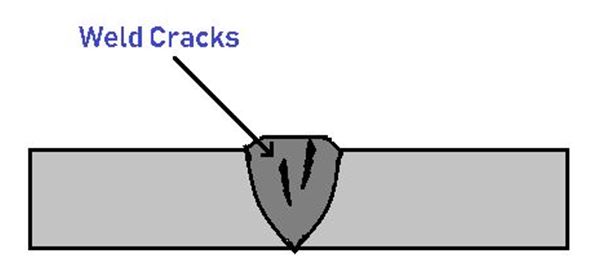
These are the most dangerous types of welding defects. It is almost not allowed by all standards in production. It can appear on the surface, in the weld metal, or in an area affected by strong heat.
There are different types of cracks that occur during welding, it depends on the temperature.
1. Hot Cracks
Hot cracks happen while the welding process or during the crystallization process of the weld joint. Temperatures at this point can exceed 10,000C.
2. Cold Cracks
These cracks occur after the weld is created and the metal temperature has passed down. They can also be made hours or days after welding steel. This mostly occurs when the deformation is made in the steel structure.
3. Crater Cracks
These cracks occur at the end of the welding process before the operator completes the weld joint. They are usually made near the end of the process.
When the weld pool cools and freezes, the weld must be sufficient in volume to overcome the metal shrinkage. Otherwise, it will make a crater crack.
Causes and Remedies of Weld Crack
Causes of Weld Crack | Remedies of Weld Crack |
Using hydrogen while welding ferrous metals. | Using suitable metals. |
Applying low current with high welding speed. | Utilizing the appropriate welding speed and current. |
The design concept is poor. | Using proper design concepts. |
Not doing preheating before starting welding. | Preheating the metal before starting welding. |
Contamination of base metal. | Cleaning the metal surface before welding. |
Residual stress solidification due to shrinkage. | Giving decent cooling of the weld area. |
The high mixture of sulfur and carbon in the metal. | Using a correct mixture of sulfur and carbon in the metal. |
Improper filling of the crater in welding. | Ensure that the crater is properly filled to prevent crater cracks. |
#4 Incomplete Fusion
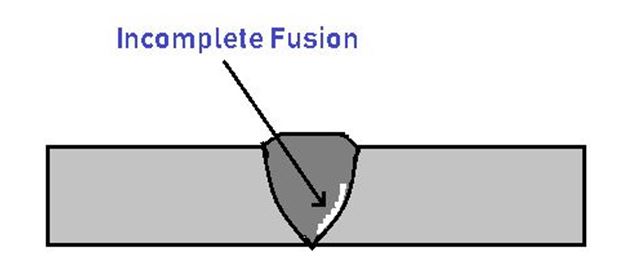
These types of welding defects occur when there is a shortage of suitable fusion between the metal and weld. It may also be visible between adjacent weld beads. This produces a gap inside the joint that is not filled with molten metal.
Causes and Remedies of Incorrect Fusion
Causes of Incorrect Fusion | Remedies of Incorrect Fusion |
Contamination of metal surface. | Cleaning the welding area of the metal surface before welding. |
Using low heat input. | Utilizing the proper heat input for welding. |
The diameter of the electrode is wrong for the thickness of the material you are welding. | Use the correct diameter of the electrode to fit the thickness of the material that you are welding. |
Incorrect electrode angle. | Ensure the angle of the electrode is suitable for welding. |
Employing too fast travel speed. | Decreasing the speed of arc travel. |
The weld pool is very large and it moves ahead of the arc. | Make sure the weld pool that you are using is proper according to the movement of the arc. |
#5 Slag Inclusion
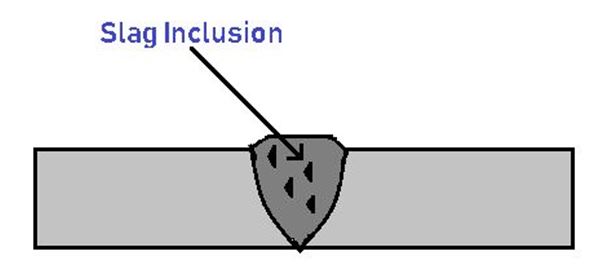
Slag inclusion is welding defects that are usually visible in welds. The slag is a dangerous substance that appears as a product of stick welding, flux-core arc welding, and submerged arc welding.
It is can occur when the flux, which is a solid shielding material applied when welding, melts in the weld or on the surface of the weld region. Slag inclusion decreases the strength of the joint and hence makes it weaker.
Causes and Remedies of Slag Inclusion
Causes of Slag Inclusion | Remedies of Slag Inclusion |
Poor chipping and cleaning of previous passes in multipass welding. | Through the wire brush, clean the weld bed surface before the next layer is deposited. |
Due to the incorrect angle of the electrode. | Adjusting the angle of the electrode. |
Using too low welding current. | Increasing the current density. |
Insufficient space for the puddle of molten weld metals. | Redesigning the joint to allow sufficient space for proper use of the puddle of molten weld metals. |
Maybe cooling is very fast. | Decreasing the rapid cooling. |
Cleaning of the metal may be improper. | Proper cleaning of the metal before welding. |
The speed of welding is fast. | Reducing the speed of the welding. |
#6 Incomplete Penetration
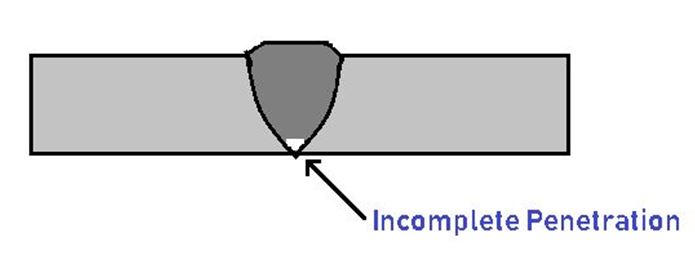
In these types of welding defects, penetration is defined as the distance from the uppermost surface of the base plate to the maximum extent of the weld nugget.
Incomplete penetration happens when the metal groove is not entirely filled, which means that the weld metal does not fully spread through the joint thickness.
Causes and Remedies of Incomplete Penetration
Causes of Incomplete Penetration | Remedies of Incomplete Penetration |
There was too much space between the metal that you are welding with. | Assuring that the surface is jointly fine. |
You are moving the bead too fast, which does not allow sufficient metal to accumulate in the joint. | Decreasing the arc travel speed. |
You are using a very low amper setting, which results in the current not being strong enough to melt the metal properly. | Selecting a decent welding current. |
Using improper joints. | Improving the design of the joint. |
Wrong position of the electrode. | Make sure the position of the electrode is very accurate. |
Using of larger diameter electrode. | You must need to use proper diameter electrodes as suitable for your welding. |
#7 Spatter
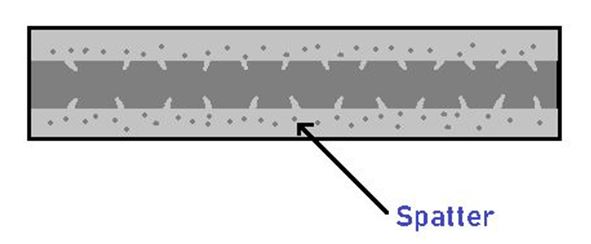
Spatters are tiny metal particles that are ejected from the arc during welding and accumulate on the base metal throughout the weld bead along its length. This is particularly common happens in gas-metal arc welding.
Causes and Remedies of Spatter
Causes of Spatter | Remedies of Spatter |
Contamination of metal surface. | Cleaning metal surfaces before welding. |
The working angle of the electrode is much more rigid. | Decreasing the arc length and increasing the electrode angle. |
Utilizing too high amper current and too low voltage settings. | Using proper polarity with adjusting the weld current. |
Using the larger arc and wet electrode. | Make sure to use the proper arc and electrode according to the welding. |
#8 Distortion
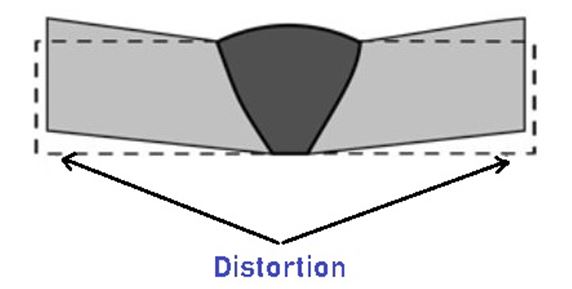
Distortion is the difference in size and location between the positions of the two metal plates before and after welding due to the temperature grade present at several points along the weld joints.
Or in other words, you can say that the distortion is due to uneven extension and reduction of the weld metal and that all kinds of distortion rise with the number of metal depositions.
Causes and Remedies of Distortion
Causes of Distortion | Remedies of Distortion |
Employing incorrect welding orders. | Ensure to use the correct welding order. |
Using a large number of passes with small diameter electrodes. | Using the appropriate number of weld passes. |
Because of high residual stresses in the plate to be welded. | Make sure you use the appropriate amount of weld metal as required by the joint. This will decrease contraction forces. |
Due to the slow speed of arc travel. | Maintaining the speed of arc travel. |
Not using any measuring instrument for dimension purposes. | If required you can use a measuring instrument, so that dimensional accuracy is accurate. |
Using too much time for the welding process. | Decreasing the time of the welding process so that the volume around the metal is not even expanded. |
#9 Hot Tear
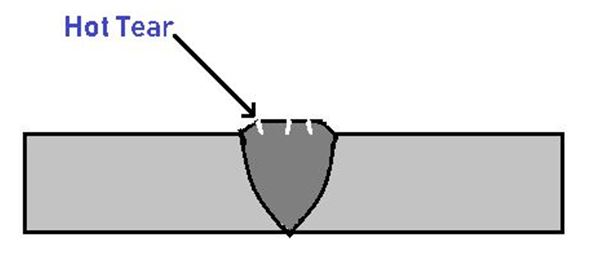
In these types of welding defects, the deposited metal starts to develop cracks from the nearby edge so that it will solidify the crack increase.
Due to the tearing of grain boundaries of the weld metal before it freezes and the metal is still in plastic condition. Therefore, it is also known as solidification cracking.
Causes and Remedies of Hot Tear
Causes of Hot Tear | Remedies of Hot Tear |
The thickness of the electrode may be wrong. | Using the right thickness of the electrode according to the base metal to be welded. |
Not using a suitable welding current. | Ensure the use of suitable welding current as needed. |
It is due to the incorrect choice of proper materials. | Using a suitable type of material for the electrode. |
#10 Mechanical Damage
Mechanical damage is an indentation in the surface of the parent metal or weld caused by damage during welding. It occurred by the incorrect use of welding tools such as hammers, grinders, and other tools used in welding.
Causes and Remedies of Mechanical Damage
Causes of Mechanical Damage | Remedies of Mechanical Damage |
---|---|
This is due to the additional force applied during chipping. | This can be easily prevented by operating the welding tools properly. |
Due to incorrect handling of the electrode holder. | After welding, make sure that the other part should not fall on the welded metal. |
Inefficient use of a grinder. | The process of hammering should be moderate when used. |
It is also caused by not engaging the arc to the metal parts. | The arc should be engaged before welding. |
#11 Misalignment
Sometimes, the decomposition of filler metals is occur in the welded joint, it is probably of misalignment. It can be recognized as wavy or curvy on the surface.
Causes and Remedies of Misalignment
Causes of Misalignment | Remedies of Misalignment |
---|---|
This type of welding defect is caused by the rapid welding process. | To avoid this, apply a slow or steady welding process. |
Due to unskilled welder or improper checking while welding. | Employing skilled welders and conducting proper checks before welding. |
The welding wire is not inline or not placed properly. | Maintaining welding wire inline or checking wire location. |
#12 Excess Reinforcement
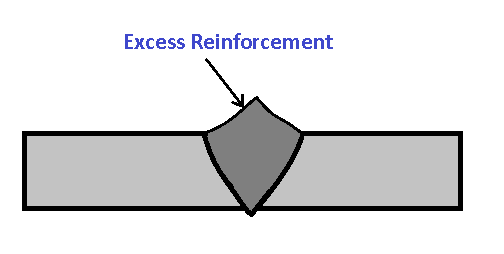
It is also a common type of welding defect that occurs occasionally. Unlike underfill defects, this occurs when there is too much filler material in the welding joint. In addition, the excess reinforcement is uneven and ragged.
Causes and Remedies of Excess Reinforcement
Causes of Excess Reinforcement | Remedies of Excess Reinforcement |
---|---|
This is caused by over flux or fast/uneven travel speed on the feed wire. | Maintain the torch running at the proper speed. |
Because of more current and heat. | Set the current correctly and avoid overheating. |
Because of the varying voltage that is mostly low. | Adjust the voltage to make sure it is not too low. |
Leaving a big gap between the welding pieces. | Align the pieces so the gap isn’t too big. |
#13 Overlap
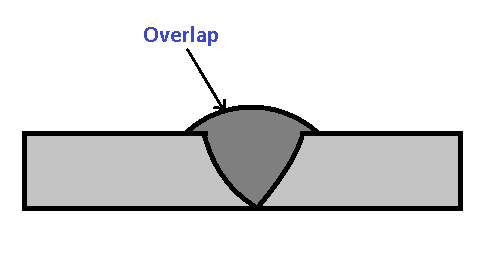
Overlap is a welding defect in which the filler material at the toe of the weld covers the base metal without bonding. In other words, it is an excessive flow of weld metal.
Causes and Remedies of Overlap
Causes of Overlap | Remedies of Overlap |
---|---|
The main reason for this defect is applying improper welding technology. | Achieving improvements in welding techniques. |
Due to varying the torch angle. | Maintaining correct torch angle. |
Using large-size electrodes in welding. | Be sure not to use large-size electrodes. |
#14 Lamellar Tearing
It is a cracking defect that occurs at the bottom of the weld and is mainly found in rolled steel plate fabrication. The tearing always occurs within the parent plate, often outside the heat-affected zone, and usually occurs parallel to the weld fusion boundary.
Causes and Remedies of Lamellar Tearing
Causes of Lamellar Tearing | Remedies of Lamellar Tearing |
---|---|
Due to the weld metal deposits on the metal surface where optimum cohesion occurs. | This is prevented by conducting welding rest at the end. |
Because of Improper welding orientation and material selection. | Using the proper welding orientation and selecting the best quality materials. |
#15 Whiskers
In the case of MIG welding, short lengths of electrode wire are glued through the weld on the root side of the joint, it is known as Whiskers. This is due to the electrode wire protruding from the leading edge of the weld pool.
Causes and Remedies of Whiskers
Causes of Whiskers | Remedies of Whiskers |
---|---|
Applying an increase in the electrode wire feed speed. | This can be prevented by reducing the electrode wire feed speed. |
Due to excessive travel speed. | Keep the travel speed optimal, and avoid going too fast. |
#16 Burn Through
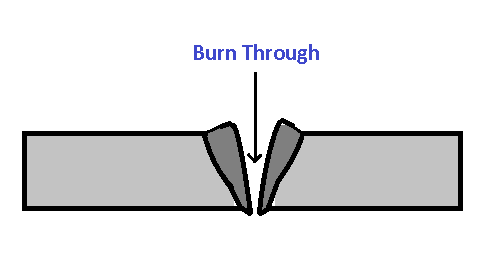
When a lot of heat is applied during the weld, the metal can blow a hole through the center. This defect is called burn-through. This is a common welding defect when welding thin parts less than 1/4 inch thick.
Causes and Remedies of Burn Through
Causes of Burn Through | Remedies of Burn Through |
---|---|
This can happen with thick stock if welder settings are too high. | Do not let the current increase too much. |
If the gap between the pieces is significantly large. | Avoiding excessive gaps between plates. |
Not using enough metal hold-down and clamping. | Use adequate metal hold-down and clamping. |
Because of the very slow moment of the torch. | Make sure your travel speed is not too slow or too fast. |
Download PDF of this article
I hope that I have cleared all your doubts about “Types of Welding Defects“. If you have still any doubts about this topic you can in the comments. That’s it thanks for reading. If you liked our article then please share it with your friends.
Finally, Subscribe to our newsletter to get notifications of our new articles.
Read more about welding in our blog:
VERY USEFUL AND INFORMATIVE INFO. THANKS.
You,re welcome.
Very informative!
Good Baseline tool for Quality criteria in a fab shop!!
Thank you so much.
Thanks for you, Sir
You’re welcome.
Good explanation
Thanks for your feedback.
Very Good information sir
Thanks for your feedback.
welding
Yeah