In this post, you will learn what is brazing and how it is done with It’s Working principle, Applications, Advantages, Types of brazing and more
Brazing and It’s Types
Brazing is a process of joining two pieces of metal in which a non-ferrous alloy is introduced in a liquid state between the pieces of metal to joining allowed to solidify.
The melting temperature of the filler material is about 600°c, but lower than the melting temperature of the parent metal. The filler metal is distributed between the surface by capillary action.
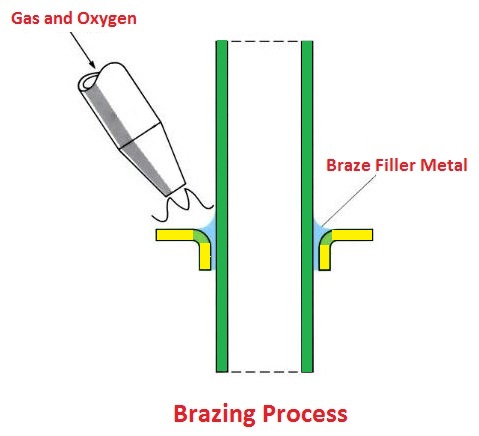
Brazing is basically the same as soldering, but it gives a much stronger joint than soldering. The principal difference is the use of harder filler material, commercially known as a speller, which fuses at some temperature above red heat, nut below the melting temperature of the parts to be joined.
Read also: Soldering: Types, Soldering Tools, Safety in Soldering and Advantages
Types of Filler Metal Used in Brazing
Filler metals used in this process may be divided into two classes:
- Copper-base alloys.
- Silver-based alloys.
There are a number of different alloys in each class, but brasses (copper and zinc), sometimes with up to 20% tin are mostly used.
They have a melting range from 850 to 250°C and are used mainly for brazing the ferrous metals. Silver alloys (silver and copper or silver, copper and zinc) having a melting range of 600 to 850°C are suitable for brazing any metals capable of being brazed. They give a clean finish and a strong ductile joint.
Like welding and soldering, The parts joined by brazing are cleaned of oil, dirt or oxides and clearances between mating surfaces are very small. The flux is applied and the pieces are applied together with proper clearances for filling the filler metal.
They are then heated at about 600°c. The molten is allowed to flow by capillary action into space between the parts and then cooled slowly. Borax, either alone or in combinations with other salts is commonly used in a flux.
The advantages of joining metals by brazing are that dissimilar metals and parts having a thin section can be joined easily. Brazing is used for the fastening of pipe fittings, tanks, credible tips on tools, radiators, heat exchangers, electrical past and the repair of castings.
Types of Brazing
Following are the common types of brazing:
- Torch brazing
- Furnace brazing
- Silver brazing
- Braze welding
- Cast iron welding
- Vacuum brazing
- Dip brazing
1. Torch Brazing
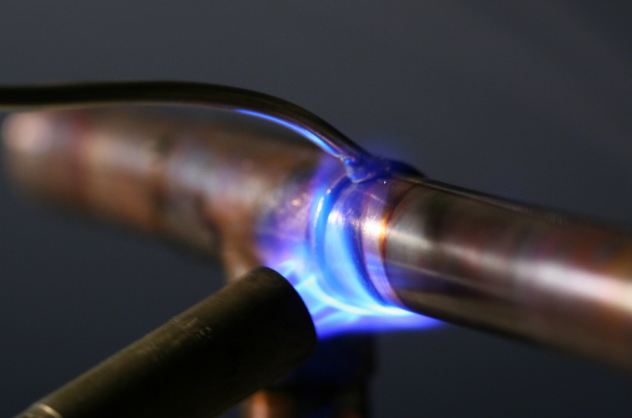
Torch brazing is the most common method used in mechanized brazing. It is used in small production versions or in special operations, and in some countries. There are three main classifications of the torch brazing in use:
- Manual torch brazing
- Machine torch brazing
- Automatic torch brazing
2. Furnace Brazing
Furnace brazing is a semi-automatic process that is widely used in industrial brazing operations due to its flexibility to mass production and the use of unskilled labour. One of the main advantages of furnace brazing is the ease with which it can produce a large number of small parts that are easily toothed or self-detecting.
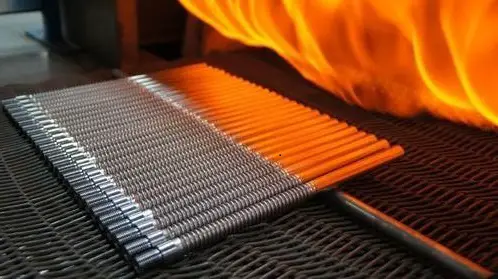
This process has a controlled heat cycle (permitting the use of parts that may be deformed under localization heating).
3. Silver Brazing
Silver brazing is also known as hard soldering, is brazed utilising a silver alloy-based filler. These silver alloys contain many different percentages of silver and other metals, such as copper, zinc, and cadmium.
4. Braze Welding
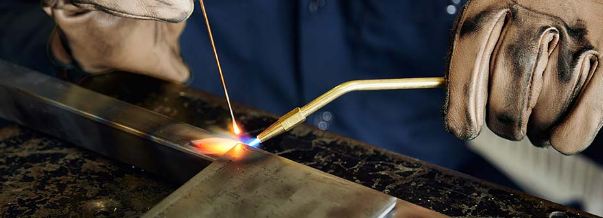
Brake welding is the use of a bronze or brass filler rod coated with flux to attach the steel workpiece. The equipment required for braze welding is basically the same as the equipment used in brazing.
Since brake welding usually requires more heat than brazing, acetylene or methylacetylene-propylene (MAP) gas fuel is commonly used. Brake welding has several advantages over fusion welding.
Read also: What is TIG & MIG Welding? and Difference Between TIG and MIG welding
5. Cast Iron Welding
Welding of cast iron is usually a brazing operation, in which mainly nickel filler rods are made, although true welding with cast iron rods is also possible. The purpose behind this process is to use electricity with copper to hold underground climate pipes warm in cold climates.
6. Vacuum Brazing
Vacuum brazing is a material joining method that gives vital benefits such as extremely clean, superior, flux-free brake joints of high integrity and strength. This process is expensive because it must be done inside a vacuum chamber vessel.
The temperature uniformity is maintained at room temperature when heated in a vacuum, reducing residual stresses due to slow heating and cooling cycles.
7. Dip Brazing
Dip brazing is particularly suited to aluminium brazing because air is excluded, thus preventing the formation of oxides. Joining parts are fixtures and brazing complexes applied to mate surfaces, usually in slurry form.
Advantages of Brazing
Following are the advantages of brazing:
- Dissimilar metals and parts having a thin section can be easy.
- brazing may avoid the metallurgical damage to the base metal.
- The strong joint can be obtained by brazing.
- Properly brazed joints are pressure-tight.
- It is an economical and quick process.
- Less heating is required than for welding.
Disadvantages of Brazing
Following are the disadvantages of brazing:
- Reduction of joint strength compared to a welded joint due to the soft filler metals used.
- The strength of the brazed joint is less than that of base metal but is more likely to be higher than filler metal.
- The brazed joints can be destroyed under high service temperatures.
- Brazed joints need high-metal cleaning when done in an industrial setting.
- The joint colour is usually different from the base metal, creating an aesthetic disadvantage.
Applications of Brazing
Following are the applications of brazing:
- It is used in vacuum interrupters.
- It is used in transport applications.
- Used in constructions.
- It is helpful in medical equipment.
- Used in art and jewellery.
That’s it, thanks for reading if you have any question about “types of brazing” tell us in the comments. If you like this article please share with your friends.
Read Next:
- How Arc Welding is Done? Types of Arc Welding, Equipment, Applications and More
- How Does UnderWater Welding Works? and Types of Underwater Welding
Images Sources:
- Indiamart.com
- Wikipedia.org
Very Good information sir
Thank you