In this article, you’ll learn what is piston ring and how it works in a piston. different types of piston rings with their functions, and more.
Also, you can download the PDF version of this article at the end of it.
What is a Piston Ring?
The piston rings are fixed into the grooves of the piston to maintain a good seal between the piston and the cylinder wall. Piston rings are made and classified based on their functionality and usage.
The main purpose of the piston ring is to seal the chamber, which is the area where the piston is traveling in a two-stroke or four-stroke engine.
The piston ring is a crucial piston component, and its numbers and functions vary based on the kind and size of the engine.
Compression-type piston rings are used in 2-stroke big engines to seal the combustion chamber, and wiper rings are put beneath them to spread oil over the surface of the liner and remove deposits.
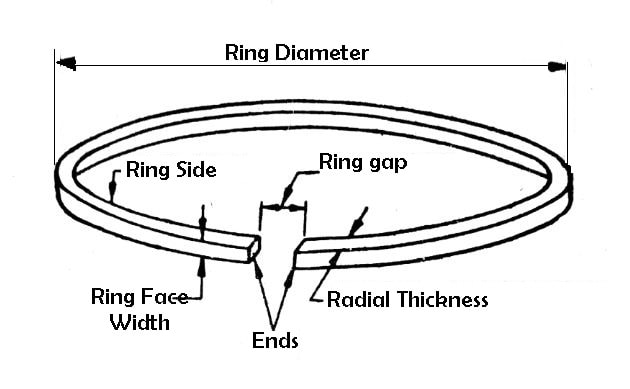
There are three functions of the piston rings as follows:
- To provide a pressure seal to prevent blow-by of burnt gases. Blow-by is the name that defines the exhaust of burnt gases from the combustion chamber, through the piston, and into the crankcase.
- To form the main path for the conduction of heat from the piston crown to the cylinder walls.
- To control the flow of oil to the skirt and rings themselves in inadequate quantity while preventing an excessive amount from reaching the combustion chamber with consequent waste and carbonization.
Read also: List of Car Engine Parts: Its Function (With Pictures)
Types of Piston Rings:
Following are the types of piston rings
- Compression rings
- Counter bored and scraper rings
- Headland rings
- Oil control rings
- One-piece slotted cast iron type
- One-piece pressed steel-type
- Three-piece steel rail type with an expander
Compression Piston Rings
In modern engines, there are two or three compression rings fitted into the top grooves. The number of compression rings tends to improve the compression ratio. An oil control ring is fitted into the lower groove of the piston. Generally, the second and third compression rings are taper-faced and supplied to improve oil sealing.
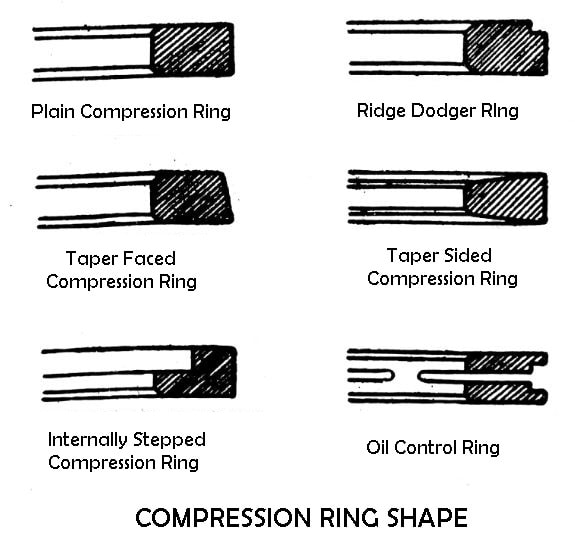
Taper-sided compression rings are utilized to control ring-sticking problems in high-output engines. It must not be fitted in grooves other than ones of the same section. A special ridge-dodger ring having a small step is specially designed for use in worn engines so that the wear ridge left by the original compression ring is cleared.
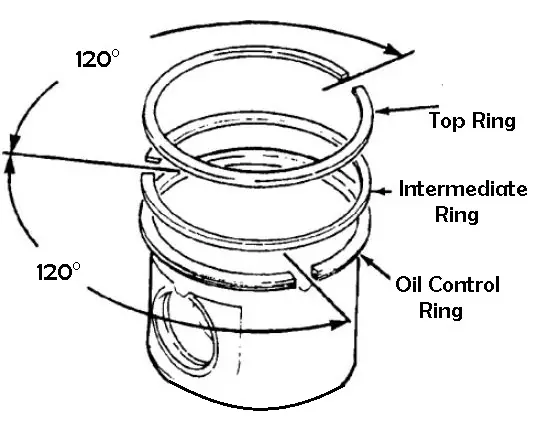
In many cases, oil control rings have a series of slots that transfer excess oil through holes in the piston groove to the inside of the piston and so to the sumps but leave sufficient oil to lubricate cylinder walls. Oil control rings have slightly more radial pressure than compression rings.
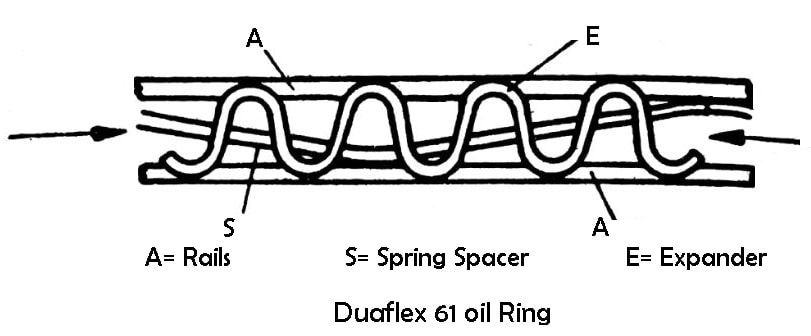
1. Counter Bored and Scraper Rings
In many engines, these types of piston rings are used for the top and second compression rings. During suction stroke as shown in the figure, the rings twist slightly due to the internal forces produced by cutting away a corner of the rings.
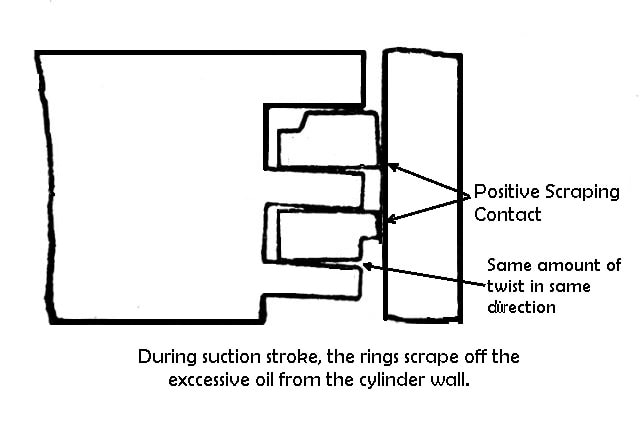
Thus, as the rings move down they rub off the oil that has been left on the cylinder wall by the oil control rings. During the compression stroke when the rings move upward, they tend to skate over the oil film on the cylinder wall. Thus, less oil is sent up into the combustion chamber.
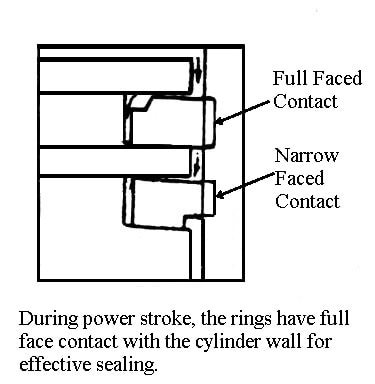
During power stroke as shown in the figure, the combustion pressure causes to untwist the rings, thus they have full-face contact with the cylinder walls for effective sealing. During the exhaust stroke, the same action takes place as in the compression stroke.
2. Headland Rings
A headland ring is a special type of compression ring, having an L-shaped cross-section. It covers or shields the headland area of the piston. This is the area of the piston between the top ring groove and the head of the piston.
This area holds a certain amount of air-fuel mixture that does not burn because the cylinder wall and piston cool this air-fuel mixture below the combustion point. This unburned air-fuel mixture passes out of the engine and can produce smog.
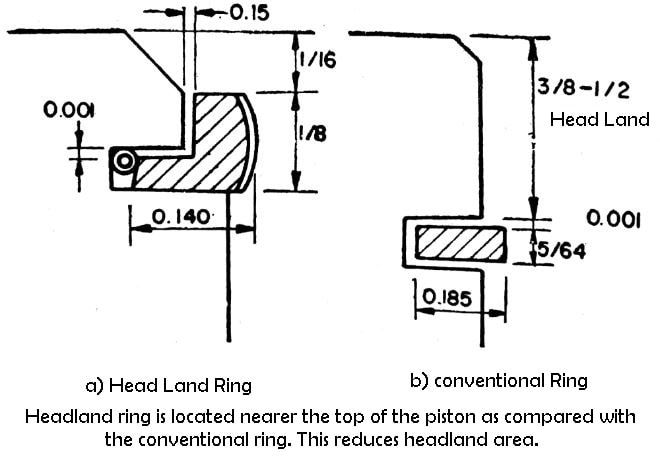
By the use of a headland ring on the piston of the special type having a chamfered top, this space is eliminated so that the amount of unburned air-fuel mixture exhausted from the cylinder is reduced. This increases horsepower by up to 10 %.
The headland ring also has the advantage of good sealing during the power stroke. As combustion starts, the pressure acts quickly on the upper lip of the ring, forcing out thus having good sealing with the cylinder wall.
Why Two Compression Rings?
Usually, two compression rings are installed on the piston. During the power stroke, the pressure increases as high as 70 kgf/cm2, and would be difficult for a single compression ring to hold this much pressure.
If there are two rings, this pressure will be divided between the two rings. The load on the upper ring is reduced so that it does not press quite so hard on the cylinder wall. Wearing of ring and cylinder is also reduced.
Oil Control Rings
Some connecting rods have an oil-split hole that splits oils from the oil pan on the cylinder wall during each revolution of the crankpin. For more oil reach the cylinder wall that is needed. It must be scraped off and returned to the oil pin. Otherwise, it will go into the combustion chamber and burn.
This would increase oil consumption so that the engine would require the addition of oil at frequent intervals. Also, the burned oil would foul the spark plug, increase the possibility of knocking, and hamper the action of compression rings.
Instead of having a cooling, sealing, cleaning, and lubricating effect on the cylinder walls, the oil must be removed from the cylinder wall every time so that it may not enter the combustion chamber. This is done by the oil control ring.
1. One Piece Slotted Cast Iron Type
These types of piston rings have slots between the upper and lower faces that carry on the cylinder wall. The oil scraped off the cylinder wall moves into the slots in the back of the oil ring grooves in a piston and from there, it returns to the oil pan.
Some rings of this type are installed with expander rings. The expander spring increases the pressure of the ring on the cylinder wall which improves the oil scraping effect.
2. One Piece Pressed Steel Type
A One-piece pressed steel-type oil control ring is mostly used in an engine with worn cylinder walls. It is made of pressed steel instead of cast iron. It can seal against only one side of the ring groove in the piston at a time, thus leaving an open path through which oil can pass upward toward the combustion chamber.
3. Three Piece Steel Rail Types with an Expander
In a three-piece steel rail-type oil control ring, the expander spring forces the rails not only upward into contact with cylinder walls but also upward and downward against the upper and lower sides of the ring grooves in the piston. This provides a more effective seal at these three vital points to provide effective oil control.
Why Only One Oil-Control Ring?
Usually, four-piston rings were installed on the long skirt pistons of earlier passenger car engines. The lower two rings were oil-control rings. However, the use of lower hood lines reduced the number of rings to three.
Because two compression rings are necessary to withstand the high combustion pressure, hence there remains only one oil control ring. It is possible to use one oil-control ring because of manufacturing improvements and the more effective action of the modern oil-control ring.
Ring Coating
To prevent rapid wear, various coatings are used on the compression rings. The coating also affects wear-in. The term wear-in means rapid removal of irregularities of new rings. When new, the rings and cylinder wall have certain irregularities and do not fit perfectly, however, after some time, these irregularities are worn away so that a much better fit is obtained.
Relatively soft substances such as graphite, phosphate, and iron oxide, which wear rapidly, are often used to coat the rings and thus help this wear-in. The rate of wear in the cylinder bore can be considerably reduced by chromium-plating the top ring rather than the bore. A chrome-plated ring, however, must not be used in conjunction with a plated bore or hardened linear.
Ring coating also has good oil-absorbing properties. They “soak up” some oil, thus improving ring lubrication. The coatings also tend to prevent ring scuffing. The scuffing results from metal-to-metal contact, high local temperatures, and actual small-area welding of the ring and cylinder wall metal.
Although the weld breaks by further movement of the piston scratches are left. The coating prevents such scuffing because a weld cannot take place unless there is actual iron-to-iron contact.
Piston Ring Material
The piston rings are made of fine-grained alloy cast iron. This material possesses excellent heat and wear-resisting quantities inherent in its graphitic structure.
The elasticity of this material is also enough to impart radial expansion and compression which is required for assembly and removal of the ring, and especially to enable it to exercise flexible pressure on the cylinder walls.
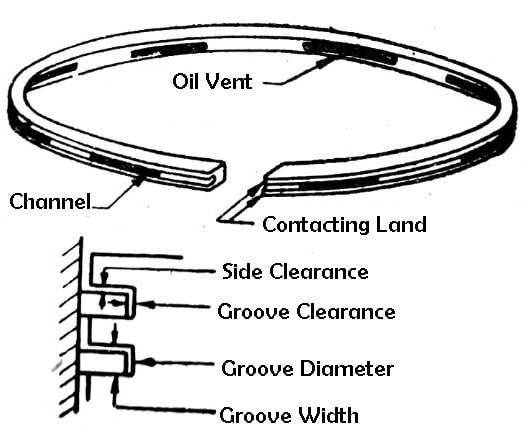
The piston rings are split so that they can be expanded and slipped over the piston head and into the recessed grooves cut in the piston. The rings usually have butt joints, but in some heavy-duty engines, the joint may be angled, lapped, or of the sealed type.
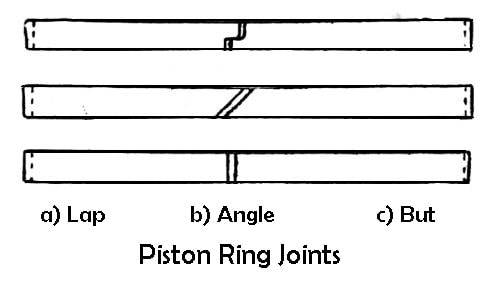
The outer diameter of the ring is somewhat larger than the cylinder bore and the split point is open. When it is installed, it is compressed thus giving it an initial tension, the joint is nearly closed. When in position, it is pressed tightly against the cylinder wall.
Piston Ring Gap [Clearance Measurement]
Piston rings have a gap so that they may be installed into the piston grooves and removed when worn out by expanding them. The gap ensures radial pressure against the cylinder wall thus having an effective seal to prevent leakage of heavy combustion pressure.
This gap must be checked if it is too great due to cylinder bore wear, the radial pressure will be decreased. To check this gap clean the carbon from the ends of the ring and then check it with feeler gauges. This gap may be in the region 0-178-0-50 mm governed by the diameter of the bore but it exceeds 1 mm per 100 mm of bore diameter, new rings must be fitted.

The gap between the ring and the groove in the piston should also be checked by feeler gauges. This gap is usually 0-038-0.102 mm for compression rings and a little less for the oil control rings.
Wear in the piston ring grooves makes the rings rise and fall throughout the movement of the piston, so creating a pumping action and resulting in heavy oil consumption. Excessive gas blow-by and loss of compression will also take place if this gap is too much.
During service, the piston ring may have lost some of its elastic properties due to which radial pressure will be reduced on the cylinder wall. This property can be checked by pressing together a worn and a new ring, as in the figure, and observing whether the gap of the worn ring closes more than the new ring.
How to Remove & Fit the Piston Rings?
The piston rings should be carefully removed from the piston either with a special removal and installation tool or with three brass strips. The tool expands the ring so that it may be easily removed from the piston. In the latter case, three strips are spaced around the circumference of the piston, and the rings are fitted over them.
The strips can be withdrawn and the ring is dropped into the groove. A ring compressor is used to compress the rings for inserting it into the cylinder while assembling the piston and cylinder. The gaps of the rings should not be in line, but they should be staggered to prevent the compression from having a direct path to leak by the piston skirt.
Life of a Piston Ring
A piston ring’s lifespan is based on its type, the engine size it is installed on, and the state of both the ring and the liner during operation.
The total life of a piston ring can reach up to 24,000 hours for a big two-stroke engine with a bore of about 900mm, and up to 16,000 hours for smaller engines with a 500mm bore.
Piston Pin
The piston pin connects the piston and the small end of the connecting rod. The piston pin is generally hollow and made from case-hardened steel heat-treated to produce a hard wear-resistant surface.
There are three different methods of connecting the piston and connecting the rod by the piston pin.
- The pin is fastened to the piston by set screws through the piston boss and has a bearing on the connecting rod, thus permitting the connecting rod end to swivel as required by the combined reciprocating and rotary motion of the piston and crankshaft. As shown in the figure.
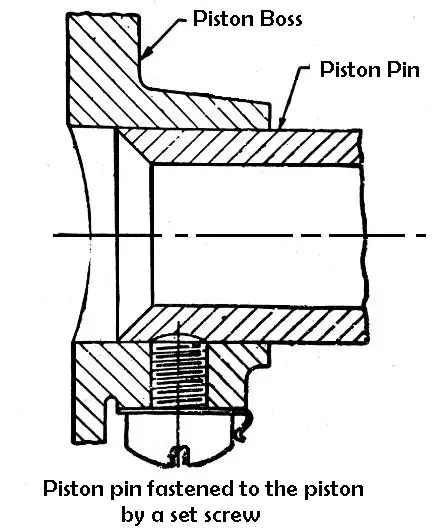
2. The pin is attached to the connecting rod with a clamp screw. In this case, the piston bosses form the bearing. A suitable slot is made on the circumference of the piston pin in which the clamp screw is fitted. As shown in the figure.
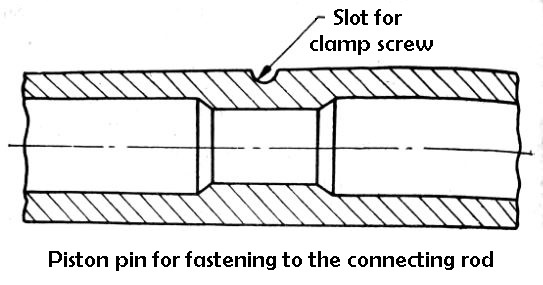
3. The pin floats in both the piston bosses and the small end of the connecting rod. It is prevented from coming in contact with the cylinder wall by two lock rings fitted in grooves in the outer end of the piston bosses, these rings are called circlips.
This method is now most generally used. In this case, a bushing of phosphor bronze or aluminum is used in the small end of the connecting rod. The bush develops very little wear and renewal only at long intervals.
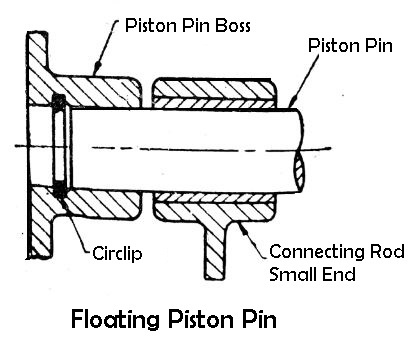
Piston Pin Fitting
Piston pins may be selectively fitted and, if supplied with the piston, are not interchangeable. In very heavy alternate loading of the piston pins of compression ignition engines, special care is taken to avoid the risk of fatigue cracks.
The external bearing surface is finished to a very high degree of accuracy to ensure the correct fit in the piston and connecting rod. The piston pin should be inspected for wear, cracking, or pitting. circlips should always be renewed, and where soft-end pads are fitted, check that they are not loose or cracked.
If you have still any doubts about the “Types of piston rings” you can contact us or ask in the comments.
Finally, subscribe to our newsletter to get notified when we upload new articles.
Download the PDF file of this article:
Read Next:
- What are the 18 Different Properties of Lubricants?
- Three Major Types of Governors Used in Engine
- 6 Main Types of Shock Absorbers
FAQs
The combustion chamber is sealed by piston rings. In both cases, they are set precisely to apply the correct pressure to the cylinder wall or liner, ensuring the oil film is consistent. This guards against wear and supplies enough lubrication.
Typically, steel and cast iron are used to make piston rings. One key need for the materials used in their manufacture is wear resistance. Wear resistance is an essential requirement for the materials used in their production.
One compression and one scraper are used in most two-stroke engines, however, most four-stroke engines use three piston rings (two compressions and one scraper).
The efficiency of piston rings is checked by removing the engine’s cylinder heads and closing one cylinder with a pressure cap. The cylinder is filled with a fluid under pressure, and the amount of time needed for the pressure to release is tracked.
I love the way you explain engine issues. Even layman could understand how engine works
Thank you! Simplifying complex topics is the goal.
Thanks a lot.
I am not a mechanic but my car (merca nezian) has been giving me trouble with low pressure, engine light on, and blue smoke form the exhaust. Why in such problem, visited many mechanics but could not find solutions until I came across your page. It has been so rewarding since than.
You’re welcome! Glad I could help. If you have more car questions in the future, feel free to reach out anytime.
It’s very interesting and I really loved the way you are making people to learn through social media. I also did mechanical engineering but I would like to learn more thanks.
Thanks for your feedback. Keep visiting 😉