In this article, you’ll learn what are Casting Defects? How do they occur? what are the causes and remedies for the casting defects.
You can also download the PDF file of this article at the end.
What are Casting Defects?
Casting is the process by which a liquid material is poured into a mold containing a hollow cavity of a desired shape, and then cooled. The cooled part, also known as a casting, is removed or broken from the mold to complete the process.
This process involves applying high pressure to the molten metal. Due to this, it is prone to several unwanted phenomena which may compromise the quality of the final products. These are called casting defects, causing significant problems for manufacturers.
Castings can contain a variety of defects, each with its own characteristics, causes, and remedies. Identifying the causes and defects of casting is crucial. Therefore, you can prevent these imperfections proactively and deliver high-quality products.
Here are specific examples of defects that can appear in casting process, along with the causes and remedies of each type of defect. So let’s get started.
Read Also: Different Types of Pattern in Casting Process (Explained)
Types of Casting Defects
Following are the major types of casting defects:
- Mismatch
- Swell
- Pinholes
- Blow holes
- Open holes
- Cut and washes
- Fusion
- Drops
- Metal penetration
- Shrinkage defect
- Run out
- Slag inclusion
- Hot or hard spot
- Hot tear or crack
- Col shut
- Dirt
- Misruns
- Honeycombing or Sponginess
- Fins and burns
- Warpage
#1 Mismatch
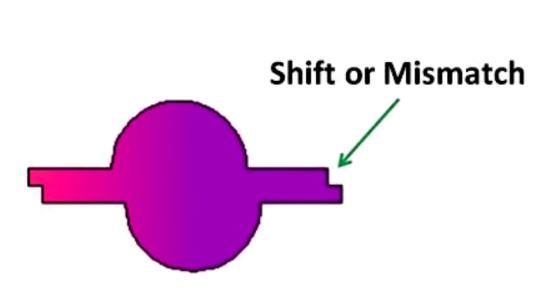
Also known as shift, it is a casting defect usually caused by misalignment of the mold’s top (cope) and bottom (dope) parts. Sometimes it may occur due to misalignment of the core at the parting line.
There are mainly two types of mismatch: mold shift and core shift. Mold shift indicates mold misalignment and is often visible as horizontal displacement. Whereas core shift is caused by misalignment of the core, which appears as a vertical displacement.
Causes | Remedies |
---|---|
Improper alignment of top and bottom parts during mold practice. | Confirming proper match plate pattern alignment and mounting. |
Caused by loose box pins and incorrect pattern dowel pins. | Using the proper molding box and closing pin. |
Also, by misalignment of the flask. | Inspecting the alignment of the flask. |
#2 Swell
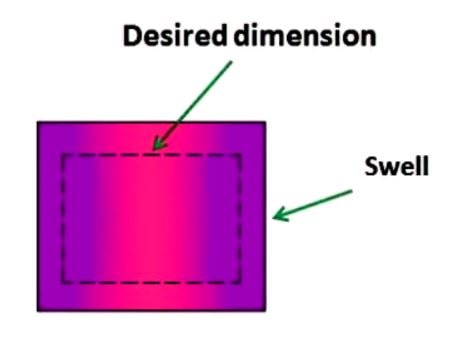
Swell refers to the enlargement of the mold cavity. This is due to the pressure of the molten metal, resulting in local or overall elongation of the casting product. It usually takes the shape of a slight, smooth bump on the surface of the casting. Consequently, its feeding and machining requirements will increase, resulting in wasted metal.
Causes | Remedies |
---|---|
Inappropriate ramming of the sand mold. | It can be prevented by using a strong, properly rammed mold. |
Due to low-strength mold. | Molds are designed to withstand the pressure of the molten metal to prevent rearward movement of the mold wall. |
#3 Pinholes
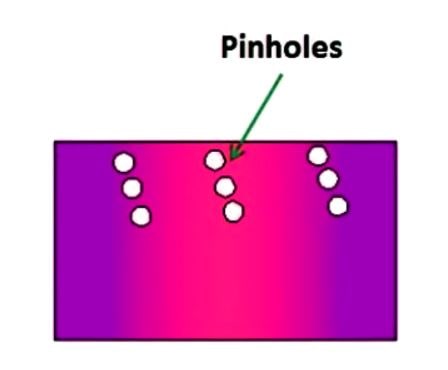
Pinholes are also casting defect that occurs at the top of a die-cast part. These are small holes of about 2 mm, usually found in poorly ventilated pockets on the upper surface of the workpiece.
These holes are clearly visible, meaning that no special equipment is required to identify them. Generally, they appear in large numbers either on top of the casting or just below.
#4 Blow Holes
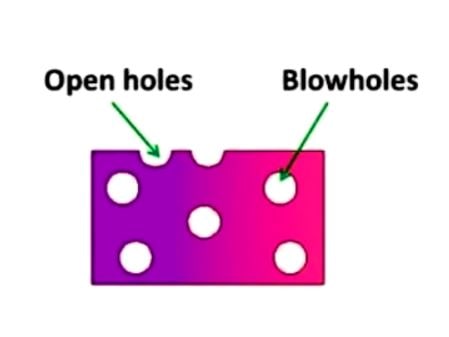
Blow holes are large holes that form inside a cast workpiece. Blowholes are formed when gases entrapped on a casting’s surface after solidifying form a rounded or oval cavity. These holes are not visible to the naked eye. To detect them, you will need X-ray, ultrasonic, harmonic, or magnetic analysis.
Causes | Remedies |
---|---|
Molding sand is extremely damp. | Molding sand should have a controlled moisture content and be kept at the desired level. |
Due to the low permeability of the sand. | The sand used must have high permeability. |
Poor venting is provided. | A sufficient venting facility should be provided. |
Read Also: 23 Types of Metals: Their Properties & Applications [Explained]
#5 Open Holes
When the metal is cast into a mold, open holes appear on the surface of the metal due to the entrapment of air. This type of casting defect is round or oval on the surface of the casting. It often has a smooth surface with a bright yellow or white color.
After casting, you can identify gas porosity defects by visual inspection. In addition, to check for this defect on non-machined surfaces, you need an X-ray device.
Causes | Remedies |
---|---|
Insufficient venting of mold and cores. | Enhancing solidification by lowering the metal temperature during casting. |
Bad drying of mold and cores. | Dry the molds and cores before use and store. |
Exceeding moisture content of molding sand. | Incorporate good fluxing and melting practices. |
Poor gas permeability of sand. | Improving permeability of mold and cores. |
#6 Cut and Washes
Cuts and washes are areas of excess metal that appear when molten metal erodes the molding sand. In castings, cuts are low projections that decrease in height as they extend along the drag face.
In this case, the sand does not have enough strength to resist erosion. Cuts and washes usually tend to the side where the liquid metal pressure is higher.
Causes | Remedies |
---|---|
This may occur due to the high-velocity flow of the molten metal, resulting in excess metal passing through the gate. | Make sure to check the proper design of the gating system. |
It can also be caused by excess metal in some regions of the mold. | Improving core and mold strength. |
Adding more additional binder to the facing and core sand. |
#7 Fusion
It is also a casting defect usually observed when grains of sand mix with the flowing liquid metal. As a result, a thin layer of hard, vitreous crust forms firmly attached to the casting. This is mainly due to the low refractoriness of sand. The low refractoriness of sand prevents it from resisting the liquid metal’s high temperatures.
Causes | Remedies |
---|---|
When sand lacks refractoriness. | Improving the refractoriness of the molding material. |
Exceeding the metal pouring temperature. | Lowering the pouring temperature of molten metal. |
By adding metal to grains of sand. |
#8 Drops
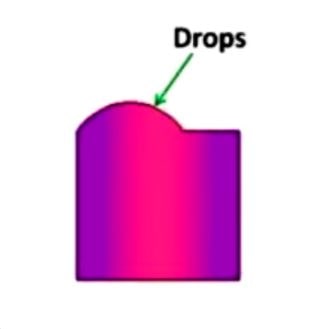
This mainly occurs when the casting is still in liquid condition. A drop-casting defect occurs when cracks appear on the top surface of the sand, causing sand pieces to fall into the melting metal.
Thus, an unusual and irregularly shaped projection is formed on the surface of the casting. In addition, it can also cause the metal surface to be dirty and unusable.
Causes | Remedies |
---|---|
The strength of the sand is low. | Using sand that has higher strength. |
Poor fluxing of the molten metal. | Cleaning of molten metal contaminants with proper fluxing. |
Due to soft ramming. | High-strength sand should be used with proper hard ramming. |
Lack of reinforcement of sand projection in the cope (Facing). | Supporting the sand projections with gaggers or nails. |
Read Also: Different Types of Dies used in Manufacturing (Complete Guide)
#9 Metal Penetration
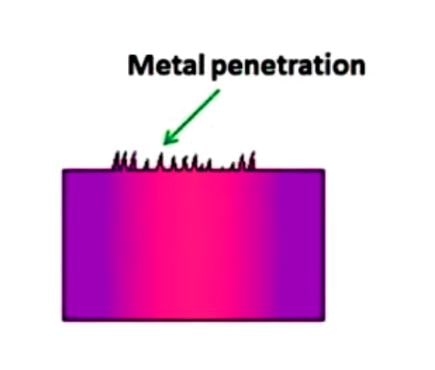
These defects can be observed in situations where molten metal enters openings or gaps in the molding sand. As a result, this results in a rough and uneven surface finish of the casting, which is clearly visible.
It is mainly because the grain size of the molding sand is too coarse, which prevents the proper flow of the liquid metal to the mold. Thus, it will acquire a rough and irregular surface, reducing its aesthetics.
Causes | Remedies |
---|---|
Due to high permeability and low-strength sand. | This can be prevented by using high strength, small grain size, and low permeability sand. |
Silky or soft ramming of sand. | Ensuring the hard ramming of sand. |
Absence of mold wash. | Provide a barrier against metal penetration by coating the surface of the mold with a mold wash. |
#10 Shrinkage Cavity
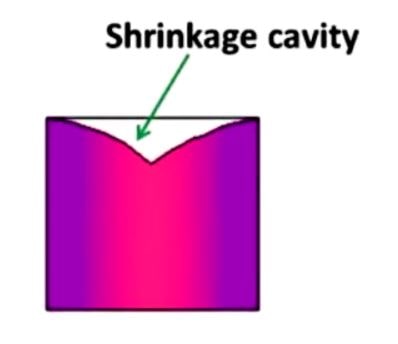
When holes are created in the casting due to volumetric contraction, this is sometimes referred to as shrinkage cavities.
Causes | Remedies |
---|---|
Due to uncontrolled solidification of molten metal. | Applying the principle of directional solidification to mold design. |
Mainly because the pouring temperature is too high. | Use of chills (a device used to promote solidification in a specific part of the metal casting) and padding. |
#11 Run Out
There is a phenomenon known as run out, which occurs when liquid metal leaks out of the mold, causing a casting to be incomplete or missing.
Causes | Remedies |
---|---|
A faulty mold usually causes this. | Replacing defective molds before casting. |
An incorrect flask is responsible for this defect. | Ensuring casting mold design with precision. |
#12 Slag Inclusion
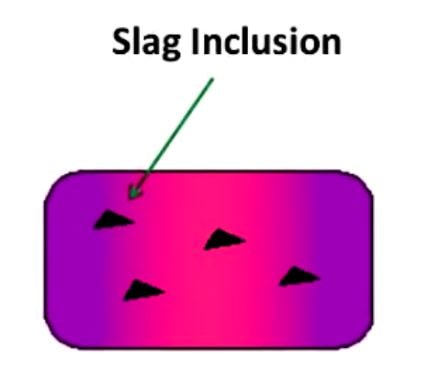
As a result of the pouring of molten metal containing slag particles into the mold cavity and the solidification of the molten metal, slag inclusions occur. The defect is usually found on the surface of the casting. This lowers the mechanical properties of the final product.
The appearance of the defect is a ribbon-like entrance or pocket with sharp edges and irregular shapes. Many other types of inclusions are available to look for, such as sand, nails, dirt, or oxides. It is only a few millimeters thick. You can easily see them without using any tools.
Causes | Remedies |
---|---|
Slag particles are involved in the pouring and solidification of liquid metal. | This can be prevented by regular die cleaning. |
Due to a wrong gating system design. | Using the proper design of the gating system. |
During the solidification process, insoluble intermetallic compounds are formed. This causes them to separate into a residual liquid. | This can be avoided by using clean molten metal. |
Using alloy that has not completely dissolved in the melt. | Analyze the changes in metal alloys with a small piece of alloy material. |
Read Also: 10 Different Types of Corrosion in Metals [Prevention Methods]
#13 Hot or Hard Spot
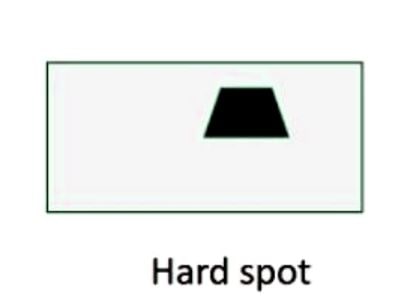
These types of casting defects occur when an area on the casting cools faster than the surrounding material. A hot spot refers to a part of the casting that is harder than its surrounding area. It is also referred to as a hard spot in some cases.
Causes | Remedies |
---|---|
This is due to the rapid cooling of an area of the casting compared to the surrounding material. | This can be prevented by utilizing proper cooling methods. |
Changing the chemical composition of the metal can resolve this defect. |
#14 Hot Tear or Crack
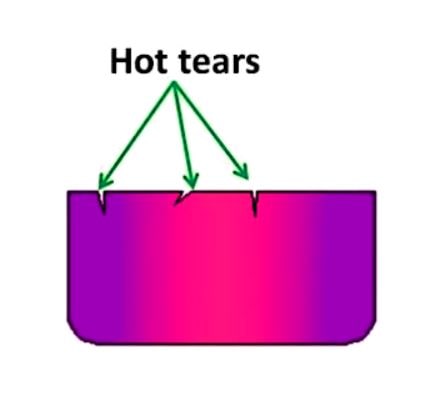
During the cooling process of the molten metal, residual stress (tensile) in the material causes the casting to fail. In this case, the failure of the casting looks like a crack, which is called a hot tear or crack.
This defect is usually observed during the solidification of the metal casting. Some cracks are obvious and can easily be seen with the naked eye, while others may require specialized equipment. This is commonly noticed as irregular or linear patterns on die-cast parts.
Causes | Remedies |
---|---|
This is due to thermal contraction on the surface of the metal. | Eliminating residual stress from the casting metal. |
Bad metal pouring temperature. | Ensuring uniform thickness throughout the material. |
The placement and solidification process of the gates may be improper. | Using standard methods of solidification and placing gates correctly. |
#15 Cold Shut
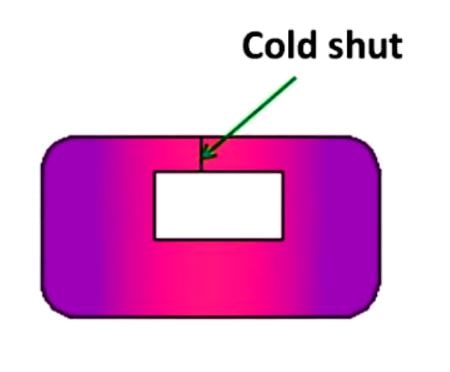
Cold shut is also a type of crack with rounded edges. Two streams of molten metal enter the mold from two gates, and when these streams meet at a junction with low temperatures, they do not fuse and form a cold shut. It is visible with the naked eye and often causes the cast to reject, creating a weak spot.
Causes | Remedies |
---|---|
Due to the wrong design of the gating system. | Optimizing gating systems and ensuring proper metal flow. |
This is due to the low temperature of the liquid metal. | Enhancing gas permeability of mold. |
Lack of fluidity of molten metal. | This is avoided by increasing the pouring temperature of the metal. |
#16 Dirt
Dirt can also cause serious casting defects. Dirt defects result from the embedding of dust and sand particles in the casting surface.
Causes | Remedies |
---|---|
This is due to improper maintenance and sand washing. | Using the proper operation of the mold to avoid crushing. |
Slag particles are present in the molten metal. | Adequate fluxing should be accomplished to remove the impurities of the slag. |
Read Also: Understanding Different Types of Welding Joints
#17 Misruns
Misruns are related to cold shut which occurs when the liquid metal is too cold to flow to the ends of the mold cavity before freezing and solidifying. In this case, the liquid metal does not fill the mold cavity. Misruns refer to the empty part or space in the mold.
Causes | Remedies |
---|---|
This is mainly due to the lack of fluidity of the molten metal. | Improving the fluidity of molten metal. |
Imperfect design of the mold and gating system. | Correcting the design of the mold and gating system. |
#18 Honeycombing or Sponginess
A type of casting defect that occurs when there is a collection of small cavities present within the metal casting that are close to each other, and appear in close proximity to one another.
Causes | Remedies |
---|---|
Caused by mechanically frozen impurities in the suspension of molten metal. | Restricting the entry of dirt and scurf into the molten metal. |
Inadequate skimming in the ladle. | Removing slag material from the molten metal by skimming it thoroughly in the ladle. |
#19 Fins and Burns
Fins and burns are one of the most commonly occurring casting defects. Also known as flash, it is unwanted and additional material attached to the casting metal. It is typically formed by a thin sheet of metal that forms at the edges of the parting line. It is a waste material that turns into slag after melting.
Causes | Remedies |
---|---|
Due to the wrong combination of mold and core. | The accurate assembly of the mold and cores can prevent it. |
Insufficient weight of mold. | Make sure the weight on the top part of the mold is sufficient so that the two parts fit tightly together. |
Inappropriate clamping of the flask. |
#20 Warpage
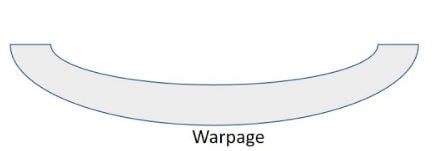
In casting, warping refers to an undesirable deformity that can occur over the course of time, which can impact the shape and dimensions of the final product as a result. This usually occurs during or after solidification. It causes the metal to be rolled into flat or large sections.
Causes | Remedies |
---|---|
Caused by different rates of solidification of the different sections. This creates tension in the surrounding walls. | Normalizing type of heat treatment can dismiss residual stresses in casting. |
Large and flat sections are more prone to such types of casting defects. | This can be prevented by proper casting design. |
Closing It Up
I hope I have covered everything about this article “Casting Defects“. If I missed something, or if you have any doubts, let me know in the comments. If you liked this article, please share it with your friends.
Want free PDFs direct to your inbox? Then subscribe to our newsletter.
Download PDF of this article:
You might like to read more in our blog: