in this post, you’ll learn what is NC machine and its working, types of NC system, basic components, NC coordinate system, application, advantages and more with PDF download.
NC Machine (Numerical Control Machine)
In conventional machine parameters like feed, depth of cut, and speed are manually controlled by the operator. The accuracy of the job depends essentially on the skill of the worker. These machines have the following disadvantages:
- More time consumption
- Less accuracy
- Less production
- Requires skilled labours
- More wastage of materials
Numerical control (NC) leads to the method of controlling the manufacturing operations through numerical instructions in the form of directly inserted coded in machine tools.
It is important to understand that NC is not a machining method rather, it is a concept of machine control.
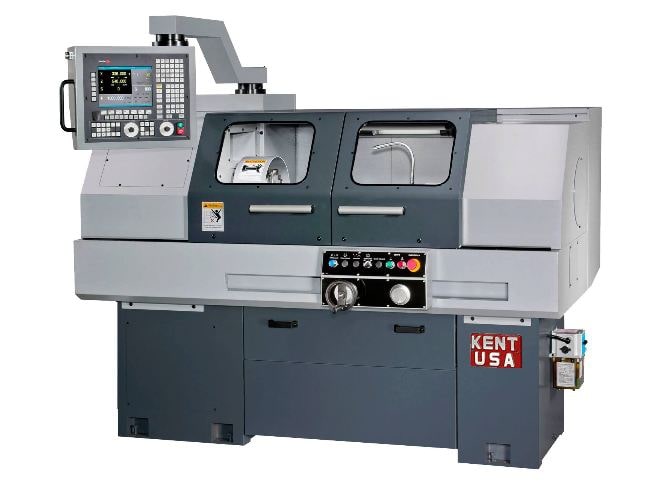
Wikipedia.org
Numerical Control (NC) A machine tool is operated by a series of coded instructions that include numbers, letters of the alphabet, and symbols that the machine control unit (MCU) can read.
These instructions are converted into electrical pulses that the machine’s motors and controls follow to perform manufacturing tasks on a workpiece.
Read also: CNC Machine: Overview, Features, Basic Elements, Working
Numbers, letters, and symbols are coded instructions that apply to specific distances, positions, tasks, or speeds that a machine tool can understand as it machines the workpiece.
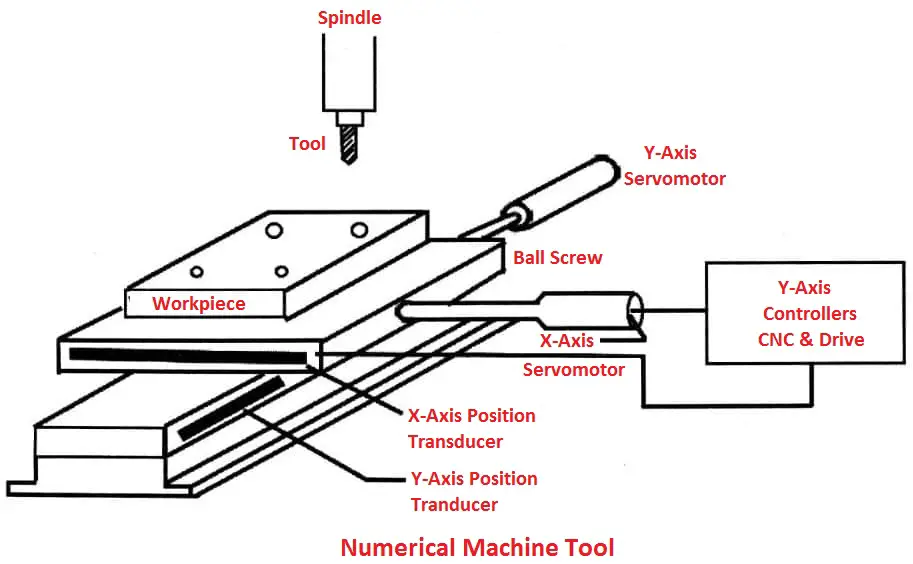
Numerical control (NC) refers to the method of controlling manufacturing operations through numerical instructions directly coded in machine tools. Numerical control (NC) can be defined as programmable automation, over which the process is controlled by numbers, letters, and symbols.
Types of NC Systems
Following are the main three types of NC system according to the machine basis:
- Point to Point
- Straight cut
- Contouring
The classification is related to the number of control over the relative motion between the workpiece and the cutting tool. Minimal control is placed on the equipment speed along with the point to point system. Contouring describes the highest level of control.
Basic Components of NC machine
The basic components are:
- Program of instructions
- Machine control unit
- Machine tool or Processing equipment or other controlled processes

The main components of NC machines are explained as follows:

1. Program of Instructions
The program of instructions is a complete step-by-step set of instructions that tells the machine tool what to do. It is coded on some type of input medium in a numeric or symbolic form that can be interpreted by the controller unit.
Today’s most common input medium is L-in-wide tape. Over the years, other kinds of input media have been used, including punched cards, magnetic tape, and even 35mm motion picture film. There are two other methods of input in NC systems that should be mentioned. The first is manual entry of instructional data for the controller unit.
This method is called manual data input, decreased MDI, and is only suitable for relatively simple jobs where the command will not be repeated. Other methods of input are through direct links with computers. This is termed as direct numerical control or DNC.
A program of instructions is prepared by a part programmer. The programmer’s job is to provide a set of detailed instructions by which to order the processing steps. For the machining operation, the processing step includes relative movement between the cutting tool and the workpiece.
Read also:
2. Machine Controller Unit
It includes electronics and hardware that read and interpret the program of instructions and convert it into mechanical functions of machine tools. This control unit controls the passage of equipment, feeds, tool-changes and other functions.
Common components of a traditional NC controller unit include tape readers, a data buffer, signal channels for machine tools, feedback channels from machine tools. Series controls to coordinate the overall operation of the foregoing elements.
- Tape reader
- Signal output unit
- Sequence coordinator
3. Machine Tool
It can be any type of machine tool or tool. The third basic component of an NC system is the machine tool or other controlled processes. It is a part of the NC system that performs useful functions. In the most common example of an NC system, one is designed to perform machining operations, with machine tools having a workable and spindle-like motor and controls necessary to drive them.
It also includes the cutting tools, work fixtures, and other auxiliary equipment needed in the machining operation Machine tools which are operated by Numerical Control must have the following special features.
- Structure
- Screw, Nuts and Guideways
- Spindle drives
- Tool changes
- Lubrication system
4. Drive Units (servo motors)
All axes of the machine driven by powerful DC servomotors mounted on preloaded ball bearings. The signals sent by the control unit actuate the servomotors, this cause different slide to move to give the desired length of travel and feed rate. The drive units usually have hydraulic DC motor or stepping motor.
5. Feedback Unit
This unit is also known as position feedback package. Feedback unit feeds back the information about the actual position of the movement to the control unit. The control unit compares the actual movements with the required movements. If there is a difference, the drive units are actuated to do the necessary correction.
6. Magnetic Box
The magnetic box receives electric signals from the control unit for all the other activities except for the servo motor drives. Spindle motor starting and stopping, selecting spindle speeds, making tool changes, control of coolant supply etc, are directed from the magnetic box.
7. Control Panel (Manual control)
Another element of the NC system, which may be actually part of the controller unit or machine tool, is the control panel. The control panel contains the dials and switches by which the machine operator runs the NC system.
It may also include data displays to give information to the operator. Although the NC system is an automatic system, the human operator is all needed to the machine on and off, to change tools, to load and unload the machine.
Read also:
- What is the Shaper Machine and Types of Shaper Machines
- Lathe Machine: Parts, Types, Operations, Attachments
- Drilling machine – Parts, Types, Operations and More
NC Coordinate System
NC systems can be divided on the number of the direction of motion instructions they are able to control simultaneously on a machine tool.
In the NC coordinate system, each free body has six degrees of freedom, three positive or negative translations along the X, Y and Z-axis, and three rotations clockwise or counterclockwise about these axes.
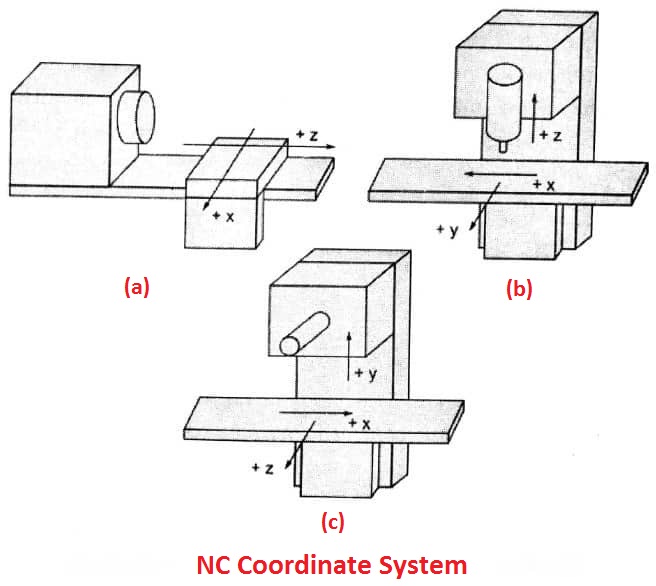
Commercial NC systems are capable of controlling simultaneously two, two and a half, three, four and five degrees of freedom, or axes. NC system controls three linear translation (3-axis system), or three linear translation and one rotation of worktable (4-axis system), are standard.
A coordinate system is applied to uniquely identify positions in the working plane or working place of the machine. The position data are always referenced to a calculated point, which is defined by coordinates.
The machine manufacturer specifies a permanent reference system for a machine the machine coordinates system. The user can freely select a separate coordinate system for each workpiece: the control is aware of the position and origin of this system with respect to the machine coordinate system. This enables the control to correctly apply for the position entries from an NC program to the workpiece.
Applications of NC Machine
NC machines are widely used in the metal cutting industry and are best used to produce the following types of product:
- Parts with complicated contours.
- Parts requiring close tolerance and/or good repeatability,
- Its parts requiring expensive jigs and fixtures if produced on conventional machines.
- Parts can undergo many engineering changes, such as during the development phase of a prototype.
- In cases where human errors could be extremely costly Parts that are needed in a hurry.
- Small batch lots or short production runs.
The NC technique has been employed to a wide range of operations, including drafting assembly, inspection, sheet metal press work, and spot welding. However, numerical control finds its major applications in metal machining processes. But it is more prominently used for various metal machining processes such as turning, drilling, milling, shaping, etc.
Machine Tool Applications (Machining applications)
- Milling, drilling, turning, boring, grinding
- Machining centres, turning centres, mill-turn centres
- Punch presses, thermal cutting machines, etc.
Other NC Applications: (Non-machining applications)
- Component insertion machines in electronics
- Drafting machines (x-y plotters)
- Coordinate measuring machines
- Tape laying machines for polymer composites
- Filament winding machines for polymer composites
Read also:
- Cutting speed, Feed, Depth of cut, Machining time in lathe machine
- 6 Different types of Shaper Machine Operations
Advantages of NC Machine
- High dimensional accuracy, reduced scrap.
- Greater flexible in operation, so a wide variety of products can be manufactured.
- Machine utilization is as high as 85 to 90% compared to conventional machines having less than 40%, increased rate of production.
- Complicated profiles can be easily programmed and machined.
- Change in design of workpieces can be easily incorporated as it requires only change in the programme.
- Better production control, the lesser requirement of jigs and fixtures.
- Reduced floor space requirement.
- Product development is easier and faster.
- A less skilled operator is sufficient
- Optimum utilization of machine
- Reduction in Labour cost.
- Details about cutting speed, feed, depth of cuts and dimensions for different operations are stored in the tape. So there is no need for manual adjustment in the machine.
It is clear from the advantages listed above that NC is appropriate only for certain parts, not all parts. The general characteristics of jobs for which NC is most appropriate are the following:
- Greater operator safety
- Greater operator efficiency:
- Reduction of scrap
- Reduced lead time for production
- Fewer chances for human error
- Maximal accuracy and interchangeability of parts
- Lower tooling costs:
- Increased productivity
- Minimal spare parts inventory
- Greater machine tool safety:
- Fewer man-hours for inspection functions
- Greater machine utilization:
- Parts are often processed in small to medium sizes.
Disadvantages of NC Machine
- The cost of the machine is very high.
- Programming training is required
- The skilled programmer is required
- Higher maintenance cost
- Higher skilled workers are needed
That’s it, thanks for reading. If you have any questions about this topic you can ask in the comments. If you like this article then please share with your friends.
Thank you for sharing..
You’re most welcome.