In this article, you will learn what is Extrusion Process and its working principles, types, applications, and advantages with PDF.
What is an Extrusion Process?
The extrusion is a process in which the metal is subjected to plastic flow by enclosing the metal in a closed chamber in which one hole is provided through a die.
The material is commonly treated so that it can sustain plastic deformation at an adequately rapid rate and may be removed from the hole in the die.
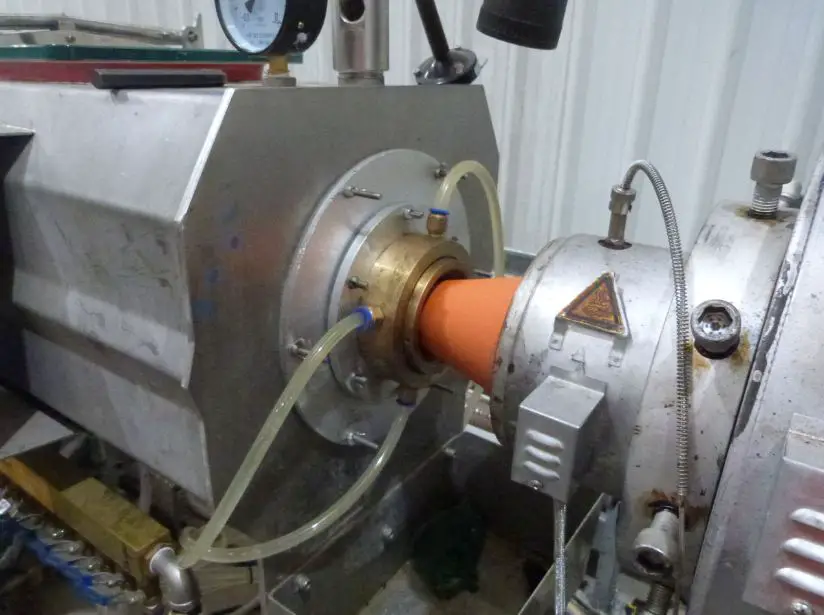
In the process, the metal allows the opening provided in the die and comes out as a long piece with the same cross-section as the die opening. The metal piece provided will have a longitudinal grain flow.
The method of extrusion is most generally used for the production of solid and hollow sections of nonferrous metals and alloys e.g., aluminum, aluminum-magnesium alloys, magnesium, and its alloys, brass, copper, bronze, etc.
And some steel products are also made by extrusion. The stock or the material to be extruded is in the shape of cast iron ingots or bullets. Extrusion may be done hot or cold.
Read Also: 14 Different Types of Lathe Cutting Tools
Working of Extrusion Process
Extrusion is a compressed metal forming process. In this process, a piston or plunger is applied to apply a compressive force to the workpiece. Initially, a billet or ingot (standard-size metal workpiece) is provided.
This billet is heated in hot extrusion or remains at room temperature and is located in an extrusion press (The extrusion press is like a piston-cylinder device in which the metal is placed in a cylinder and pushed by the piston. The upper part of the cylinder is fitted with a die).
Immediately, a compressive force is applied to this part by a plunger fitted in the press which forces the billet to die. The die is the small opening of the needed cross-section.
This high compressive force allows the work metal to flow through the die and change into the desired shape. Finally, the extruded part is removed from the press and heat-treated for better mechanical properties.
Read Also: What is Gear Cutting? Its Advantages & Disadvantages
Types of Extrusion
Extrusion processes can be classified as follows:
- Hot Extrusion
- Forward or Direct extrusion
- Backward or Indirect extrusion
- Cold Extrusion
- Hooker extrusion
- Hydrostatic extrusion
- Impact extrusion
- Cold extrusion forging
#1 Hot Extrusion
The hot extrusion is the most popular method for developing objects with a fixed cross-sectional profile. The extrusion process is performed at an increased temperature, which maintains the materials from process hardening along with making the procedure of pushing the material through the die simpler.
In general, large quantities of hot extrusion are performed using horizontal hydraulic presses that belong to a range of 250 – 12,000 tons. Here, the pressure range is 30 to 700 MPa (4,400 to 102,000 psi), so lubrication is required.
That lubrication can be obtained by glass powder in case of greater temperature extrusions and oil or graphite for all the lower temperature extrusions.
Although hot extruded material is greatly preferred, hot extrusion has a couple of limitations associated with it which are the cost of extrusion machines and their maintenance. There are two different two types of hot extrusion are as follows.
Types of Hot Extrusion
- Forward or Direct extrusion
- Backward or Indirect extrusion
Forward or Direct Extrusion
In this process, the material to be extruded is in the form of a block. It is heated to a required temperature and then it is transferred inside a chamber as shown in Fig.
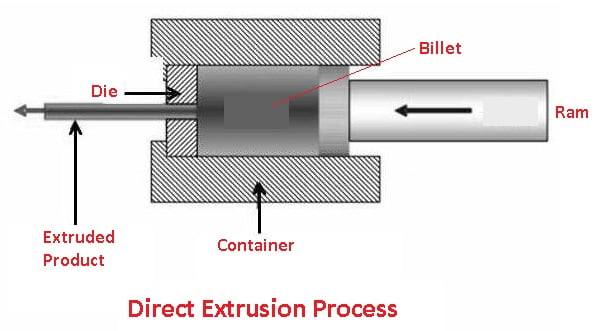
In the front portion of the chamber, a die with an opening in the shape of the cross-section of the extruded products is fitted. The block of material is pressed from behind using a ram and a follower pad.
Since the chamber is closed on all sides, the heated material is forced to squeeze through the die-opening in the form of a long strip of the required cross-section. The process seems simple but the friction between the material and the chamber walls should be overcome by suitable lubrication.
When extruding steel products, the high temperature at which the steel has to be heated makes it difficult to find a suitable lubricant. The problem is determined by applying molten glass as a lubricant. When the lower temperature is used, a mixture of oil and graphite is used as a lubricant.
Backward or Indirect Extrusion
The arrangement is done as given in the fig. The block of heated metal is inserted into the chamber. It is enclosed on all sides by the container walls except in front Where a ram with the die presses upon the material.
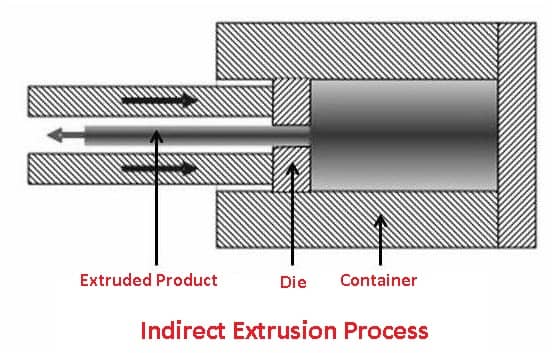
When the ram presses backward, the material has to flow forward through the opening in the die. The ram is formed hollow so that the bar of extruded metal may pass over it unhindered.
This process is called a backward extrusion process as the flow of material is in a direction opposite to the movement of the ram. In the forward extrusion process, the flow of material and ram movement were both in the same direction.
Read Also: 16 Types of Milling Operations Explained
#2 Cold Extrusion
With the help of extruders and extrusion machines, the process of cold extrusion is carried out at room temperature or moderately high temperatures. These devices or machines have been specially developed based on innovative extrusion technology.
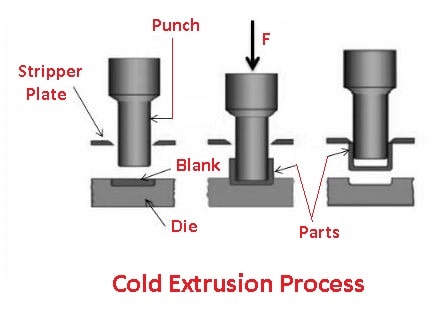
The cold extrusion can also be described as the method of shaping a cold metal by striking a slug. This strike is performed with a punch (in a closed cavity), which pushes the metal in an upward direction around the punch. This process is also called cold pressing, cold forging, extrusion pressing, and impact extrusion.
Types of Cold Extrusion
- Hooker extrusion
- Hydrostatic extrusion
- Impact extrusion
Hydrostatic Extrusion
In hydrostatic extrusion, a billet is always surrounded by a pressurized liquid, except when it is in contact with a die.
The temperature range for this process is limited by the fluid’s stability, however, it can be done in warm, cold, or hot settings. During hydrostatic extrusion, the hydrostatic medium needs to be contained, necessitating the use of a completely sealed cylinder.
Hooker Extrusion
These types of extrusion is also known as the extrusion-down method. It is used to create small, seamless, thin-walled aluminum and copper cylinders.
There are two steps in this process. In the first stage, the blank is turned into a cup-shaped piece. In the second stage, cup one’s walls thinned and grew longer.
Impact Extrusion
Impact extrusion is a type of extrusion used to make metal products with the use of a press. It can be completed with a hydraulic or motorized press. But the press has to be used to drive a metal bullet through a die.
As the metal slug passes through the die, it gets bent. This enables manufacturers to produce new goods and items that have the same dimensions and shape as the die that they utilize.
Impact extrusions require a mechanical or hydraulic press, which is used by manufacturing enterprises. The metal slug is in between a strike and a die. When the punch is lowered onto the metal slug, the press is activated, forcing the metal slug through the die.
The metal slug will then take on the physical attributes of the die. The metal slug is forced into the die and then released by an ejector.
Read Also: Different Types Of CNC Machine [Complete Guide]
Advantages of Extrusion
Some advantages of the extrusion process are described below:
- The complexity and range of parts that can be produced by the extrusion process are very large.
- Dies are relatively simple and easy to make.
- The extrusion process is complete in one pass only. This is not so in the case of rolling.
- The amount of reduction in extrusion is very large indeed.
- Large-diameter, hollow products, thin-walled tubes, etc are easily produced by the extrusion process.
- The extrusion process can be easily automated.
- Good surface finish and excellent dimensional and geometrical accuracy are the hallmarks of extruded products.
Disadvantages of Extrusion
The following are the disadvantages of extrusion:
- Changes in the size of the product.
- Product limitations can be achieved due to only one type of cross-section at a time.
- The high initial cost of the setup.
Application of Extrusion
The following are the applications of extrusion:
- The extrusion is generally used in the production of tubes and hollow pipes.
- Aluminum extrusion is utilized in structure work in various industries.
- This process is used in automotive industries to produce frames, doors, windows, etc.
- Extrusion is widely used for the production of plastic goods.
Conclusion
That’s it, Thanks for reading. I hope you find this article helpful then please share this with your friends. If you have any questions about “Types of Extrusion” ask in the comments I’ll respond to you.
Want free PDFs direct to your inbox? Then subscribe to our newsletter.
Download PDF of this article:
Read Next:
- Types of Reamer Tools and Their Applications
- 16 Different Types of Milling Cutters
- Press Machines and Types of Press Machines
External Links:
FAQs
Extrusion is the process of forcing a material through a die to form an object with a desired shape. The die is a tiny disk with a predetermined size and shape. When the material is compressed through the die, it forms the required shape. Steel is commonly used to make the die.
Extrusion processes are categorized in a variety of ways; they can be classified as direct or indirect based on the direction of extrusion. Another classification is based on the extrusion process’s operating temperature—cold, warm, or hot.
It is often used in the manufacturing of hollow tubes and pipes. Many businesses employ aluminum extrusion for structural work. In the automotive industry, extrusion is utilized to make frames, windows, doors, and other products.
1. Melting of the Raw plastic materials.
2. Filtration of the melted plastic materials.
3. Sizing of the molten plastic.
4. Workup Process.
5. Cooling of the processed raw material.
Its very usefull to improve her basic knowledge and more information of ext skills.
Thanks for your feedback.