In this article, you’ll learn what is forging? How does it work? Types of forging, Operations, Advantages, Disadvantages, and more.
What is Forging?
Normally work relating to iron is known as blacksmithy. Forging means giving the desired shape to any job of metal by heating or cooling it and then striking it either with an ordinary hammer or by using any special machine meant for this purpose.
Small forging jobs can be done by striking it with a hammer but heavy jobs for forging are done only by machines. Forging can be done in three different ways.
Types of Forging Methods
Following are the three types of forging methods:
- Hand forging
- Machine forging
- Drop forging
#1 Hand Forging
To give shape to a job by striking it with a hammer is called hand forging or smithing.
#2 Machine Forging
To give the desired shape to a job with the help of a forging machine is called machine forging. Press machines, rolling machines, and various kinds of power hammers are included in this category.
#3 Drop Forging
For jobs of the same size and similar shape, drop forging process is used. The top dye is raised to an adequate height through the mechanical device and then dropped to hit the hot metal kept at the bottom dye. Thus, the hot metal takes the shape of the dye. Wrench and other ordinary things are made through drop forging.
It is not possible to change the shape of metals when they are cold. It is, therefore, necessary to heat the metal in fire. By heating the metal, it becomes soft and acquires the property of plasticity. As such, it can be bent or molded in any shape.
Read Also: 9 Types of Sheet Metal Operations with Diagrams
Types of Forging
Following are the two major types of forging:
- Hot forging
- Cold forging
Some other types of forging
- Open die forging
- Closed die forging
- Press forging
- Upset forging
- Roll forging
Forging Operations
Following are the different types of forging operations:
- Cutting operation
- Upsetting operation
- Drawing out operation
- Jumping operation
- Bending operation
- Fullering operation
- Edging operation
- Punching or Drifting operation
- Setting down operation
- Forge welding operation
- Swaging operation
Before performing any other operation related to forging it is essential to make markings on the metal according to the drawing. For this purpose brass rules, tri-square, center punch, etc. are used.
1. Cutting Operation
To make small of long metal rods and plates is known as cutting. This can be done both in cold or hot condition. For cold metals, the chisel of cutting angle is used. For hot metals, the chisel of cutting angle is used. Metal beyond the thickness of 20mm should be cut only after heating it.
2. Upsetting Operation
This operation applied to increase the cross-sectional area of the stock over the length extension. The offsetting force is used in a direction parallel to the long axis to achieve the length, for example, the development of the bolt head.
3. Drawing Out Operation
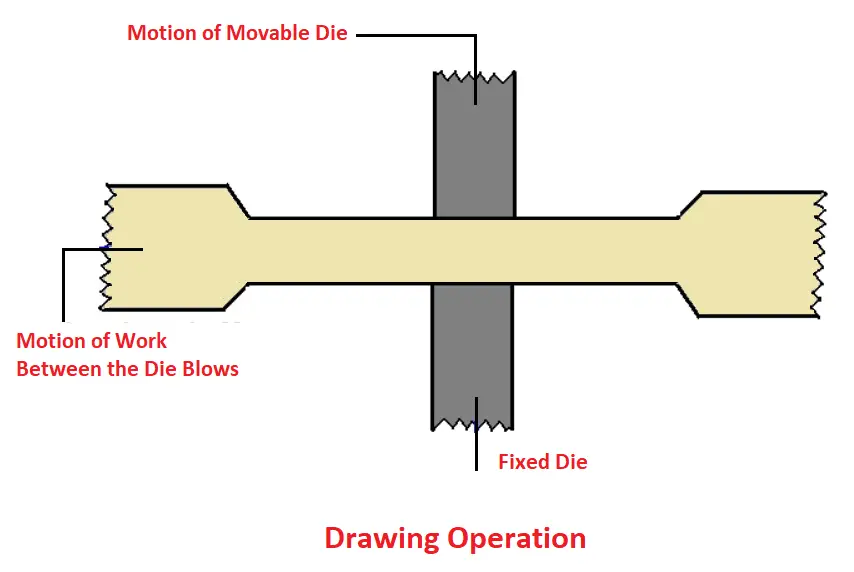
To increase metals length is called Drawing out. This has been shown in the figure. The metal is heated at a temperature between to and the hammer is struck at the beak of the anvil. Fuller is also used for this purpose.
4. Jumping Operation
To shorten and thicken a piece of metal after heating it is called jumping or upsetting. By jumping the length of the metal can be reduced to almost half. Jumping is done is three ways:
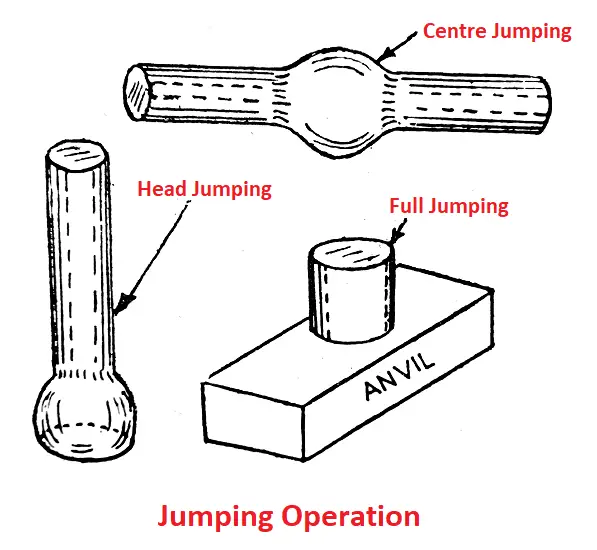
- Head jumping: This has been shown in figure. Jumping of one end of a round rod is called “Head jumping” such as rivet head.
- Centre jumping: This has been illustrated in figure. In this category. Jumping is done in any other part except the two corners of the round metal rod. Example: Tap handle.
- Full jumping: This has been shown in figure. The metal is completely heated and its length is reduced.
5. Bending Operation
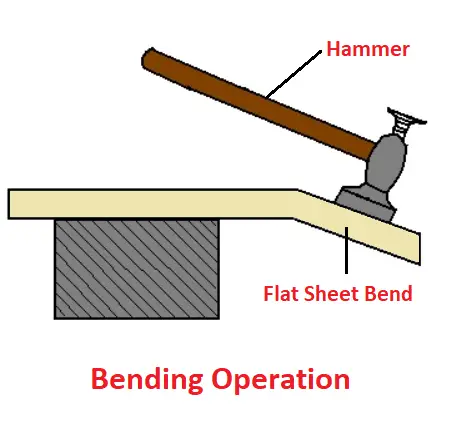
To turn or bend a piece of metal in round or angular form is called “bending”. This has been shown in the figure below. Round rings etc. are made through this operation.
6. Fullering Operation
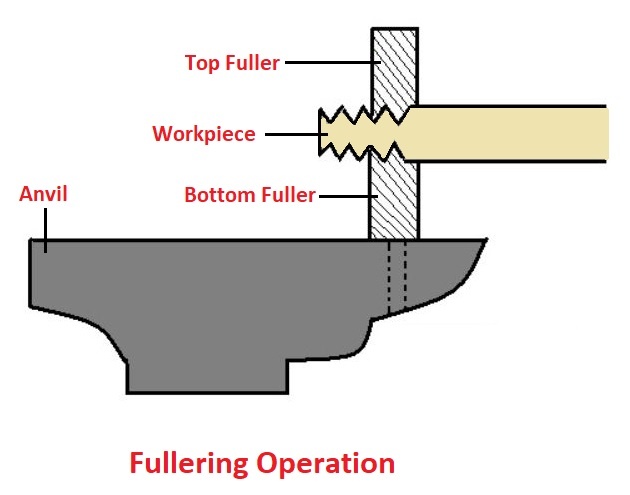
This forging operation is by placing the bottom fuller into an angle hole with hot metal, the top filler is then placed on top of the metal, force is applied through the top filler with the help of a sledge hammer.
7. Edging Operation
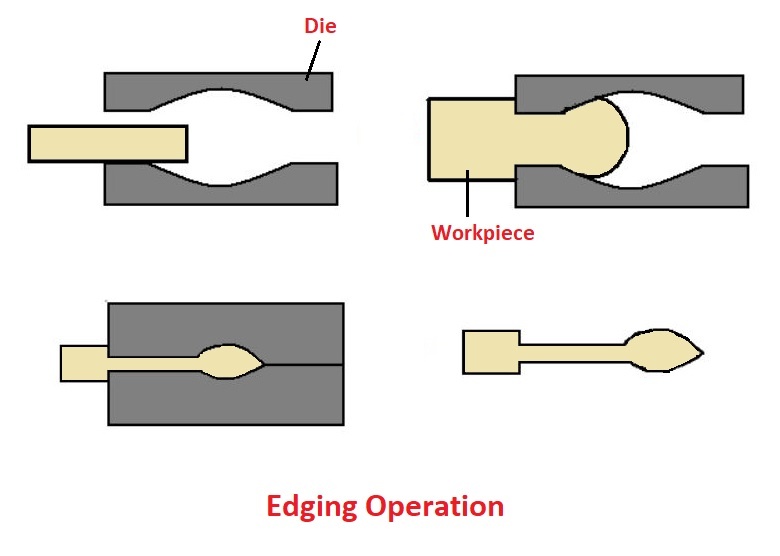
This forging operation is performed by striking or forcing the metal plate to the desired shape. The workpiece is forced between two die edges.
8. Punching Operation
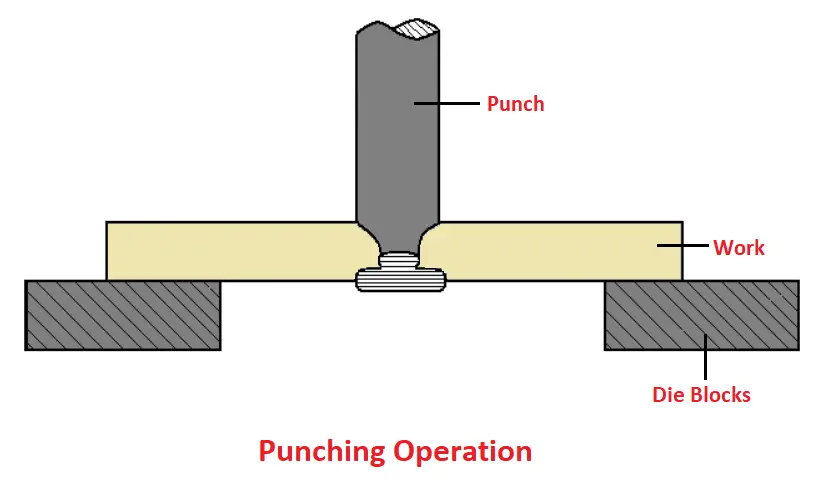
This has been shown in the figure. In this operation, the hole is made in hot metal with the help of a punch. For punching, the job is first placed on the punch hole of the anvil or a nut etc., and the hole is made with punch or holes already made by drift are enlarged.
9. Setting Down Operation
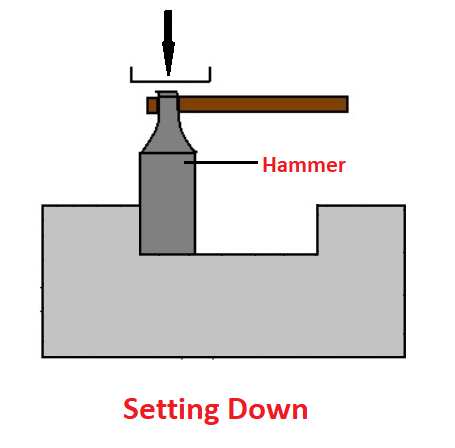
This is the finishing process. The ends and corners of forged metals are made plain and to bring roundness when their seams are closed. Swage and set hammers are used for this purpose. Apart from this, twisting an also done to provide strength to a job.
10. Forge Welding Operation
Under this process, the parts of metals are brought to a suitable temperature in a furnace and welded by pressure or blows. For forge welding, the ends of the pieces of metals are made scarf through jumping.
11. Swaging Operation
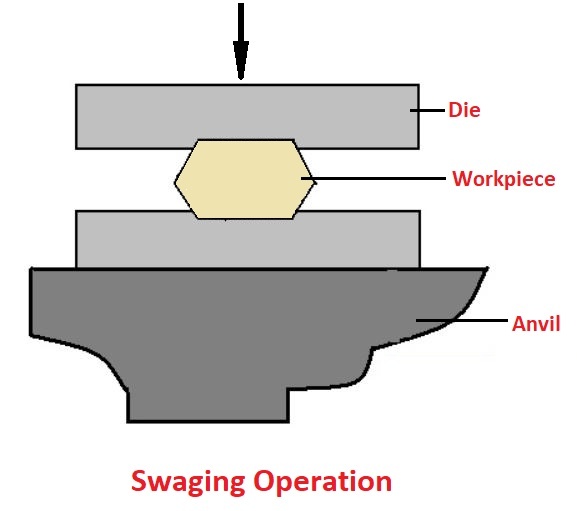
Swaging is done to decrease and complete work for the desire shape and size, usually either round or hexagonal. In this operation, the top and bottom pairs are added for small jobs, where the swag block can be used for larger jobs.
Advantages of Forging
- Tensile strength of the metal is reduced and it acquires the property of plasticity which enables us to give the desired shape to the metal.
- With the help of the properties of plasticity and malleability, drawing out, jumping and bending operations can be easily performed.
- It is easy to give a finish to a forged job because its shape is almost ready and it takes less time.
- After forging on a hand metal, other machine activities can be easily carried out on the job.
- There is little wastage of metal.
- Structure of metal becomes proper through hot forging.
- There is little scope of stresses and cracks on the metal.
Disadvantages of Forging
- When the metal is heated oxidation takes place, which harms the metal.
- Brittle metals cannot be forged.
- Finishing is not possible in the forging process.
- There is a change in jobs size.
Conclusion
So now we hope that we will clear all your doubts about forging. Still if you any doubts about “Forging or types of forging” you can ask in the comments. If you like this article please share it with your friends.
That’s it. Thanks for reading. If you have any questions about any topic ask in the comments section below.
Subscribe to our Newsletter to get notification of new posts.
Download PDF of this article:
You may be interested in reading these articles:
- Milling Machine: Main Parts and It’s Working Principle
- Metal Saw Machine and Types of Sawing Machine
- 6 Different types of Shaper Machine Operations
External Links:
- Forging Process – an overview | ScienceDirect Topics
To produce Spannners and wrenches of Non-Sparking material—-Aluminium Bronze and Berrylium Copper—–Which method is better—- Either forging or Casting ?
Forging is stronger than casting because forged parts have higher tensile and fatigue strength resulting in a much longer lifetime than cast parts.
How to download pdf
Hello there, I updated the article with the PDF file. Now you can download it.