Hello readers! In this post, we’ll discuss what is a reactor? and the different types of reactors and their applications using illustrations.
You can also download the PDF file of this article at the end.
Without further ado, let’s begin discussing what is a valve.
What is a Reactor?
Reactors are vessels that act as process vessels, designed to conduct chemical reactions and to add chemicals to them. In the chemical industry, the reactor is also called the heart of the process where chemical reactions occur.
Raw materials are processed into products, which is why chemical reactors are an essential part of a manufacturing process. Reactors are important in many types of industries such as the chemical industry, polymer industry, dyes and pigment industry, color industry, pharmaceutical industry, etc.
Reactor types vary depending on the type of reaction and the characteristics of the raw materials; thus, the industry has selection criteria for different types of reactors.
Today’s post will teach us about the various types of reactors used in the chemical industry, along with some examples. So let’s get started.
Read Also: What Are The Different Types of Generators? [PDF]
Types of Reactors
In the chemical industry, a variety of reactor types are employed. In the later part of this article, selection criteria will be discussed, including which type of reactor should be used and when.
The following are the main types of reactors:
- Batch Reactor
- Continuous Stirred Tank Reactor (C.S.T.R)
- Plug Flow Reactor (P.F.R)
- Semi-Batch Reactor
- Nuclear Reactor
- Catalytic Reactor
Read Also: Understanding Types of Casting Defects [Their Causes & Remedies]
#1 Batch Reactor
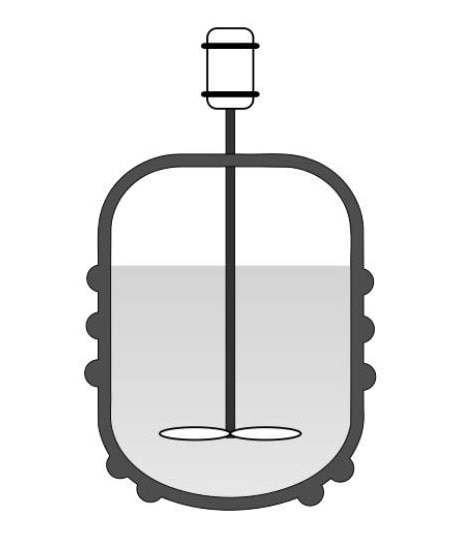
A batch reactor is a form of non-continuous reactor that consists of a closed vessel used for chemical reactions. Initially, the reactor receives the all reactants at once. In the vessel, there is an agitator that mixes the reactants thoroughly so that they react efficiently and produce products.
The batch reactor often comes fitted with cooling coils to manage exothermic processes. These types of reactors use features for heating the reaction mixture so that it can be used with endothermic processes.
It is a non-steady, transient reactor, which means the extent of conversion within the reactor varies over time. The batch reactor is highly uniform in nature, so the extent of conversion is not dependent on the location within the reactor. These are used in the pharmaceutical sector and are also employed to produce solutions, such as chemicals for dosing, etc.
Advantages and Disadvantages of Batch Reactor
Advantages | Disadvantages |
---|---|
The major benefit of using a batch reactor is its adaptability. | Batch reactors are disadvantageous because they require a lot of labor to constantly charge reactants, discharge products, and clean the reactor. |
It is possible to chemically react a wide range of reactants in the same batch reactor. | |
Batch reactors are particularly useful when a reaction creates a large number of products. | |
These are often used in laboratories to research the kinetics of liquid-phase reaction systems. |
Application of Batch Reactor
These types of reactors are used to prepare compounds for use in the reaction. In the caustic chlorine business, a batch of sodium sulfite is manufactured and used to dose in brine to eliminate free chlorine at the dichlorination outlet.
Read Also: What Are The Different Types of Valves? Explained
#2 Continuous Stirred Tank Reactor (C.S.T.R)
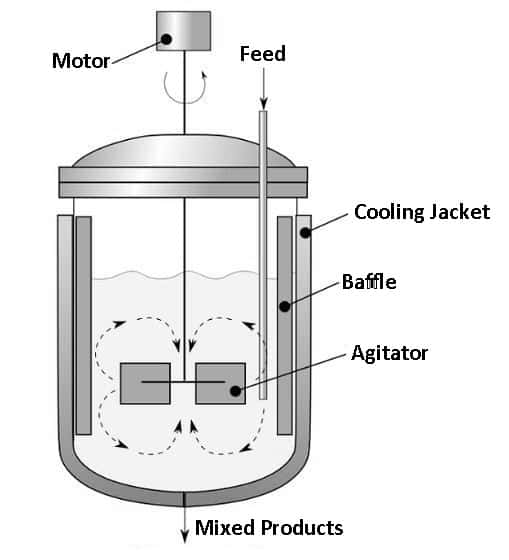
Continuous stirred tank reactors are also known as mixed-flow reactors. This reactor uses a closed tank for the reaction to take place. The tank additionally features an agitator to fully mix the reactants. In contrast to a batch reactor, it is a continuous form of equipment as implied by the name.
During the reaction, reactants enter the reactor at a specific mass flow rate, react within the vessel for a period of time dictated by the reactor’s space-time, and then products are formed. The products leave the reactor at the same mass flow rate. The time needed to process one reactor volume is one space-time.
Since the C.S.T.R. is steady-state equipment, the degree of conversion is independent of time. Due to the agitator, the concentration remains uniform throughout the reactor, so the extent of conversion is not dependent on the location.
Advantages and Disadvantages of C.S.T.R
Advantages | Disadvantages |
---|---|
The main benefit of adopting a C.S.T.R. in industries is its ability to generate a huge number of items. | A C.S.T.R.’s drawback is that it needs a very big reactor, which means it can’t be utilized for reactions with very slow kinetics. |
Because it is a continuous steady state reactor, it can run for hours on end. | The reactor’s production and operating costs may make it unfeasible. In this situation, a batch reactor is used. |
Application of C.S.T.R
CSTR reactors are widely employed in the chemical industry, particularly in continuous plants.
Read Also: Different Types of Evaporators: Their Working and Applications
#3 Plug Flow Reactor (P.F.R)
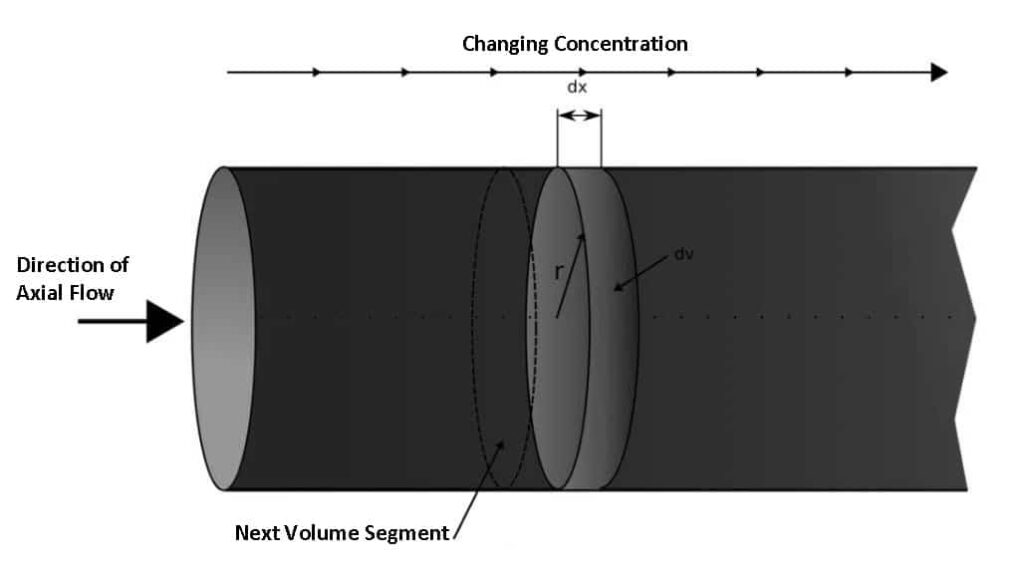
A plug flow reactor (P.F.R.) is also known as a continuous tubular reactor (C.T.R.). It is another type of reactor in which one or more chemicals are injected or pumped as a fluid through a pipe or tube.
Because the design of these reactors resembles a tube and the reaction occurs inside, they are also known as plug flow or tubular reactors. When the reagents travel through the PFR, a chemical reaction occurs.
When the reaction rate changes with respect to the distance traversed, a gradient is created; at the inlet, the rate is very high to the PFR, but as the concentrations of reagents decrease and the concentration of product(s) increases, the rate decreases.
Advantages and Disadvantages of Plug Flow Reactor
Advantages | Disadvantages |
---|---|
In terms of space time and conversion level, P.F.R. has an advantage over C.S.T.R. | One drawback is that controlling temperature gradients becomes challenging while conducting an exothermic reaction in a P.F.R. |
Compared to a C.S.T.R., the P.F.R. has a comparatively lower volume. | A P.F.R. has higher maintenance and operating costs than a C.S.T.R. |
It indicates that the reactor requires less space and that, for a given reactor volume, PFR has a greater conversion rate than CST.R. | This reactor’s shutdown and cleaning could be costly. |
The P.F.R. is frequently used to investigate the kinetics of gas phase catalytic processes. |
Application of P.F.R
PFRs are widely used in industrial processes such as chemical, pharmaceutical, fertilizer, and petrochemical manufacture. Additionally, they play an important role in polymerization procedures including those that produce polyethylene and polypropylene.
Read Also: What is a Condenser? Their Working & Applications
#4 Semi-Batch Reactor
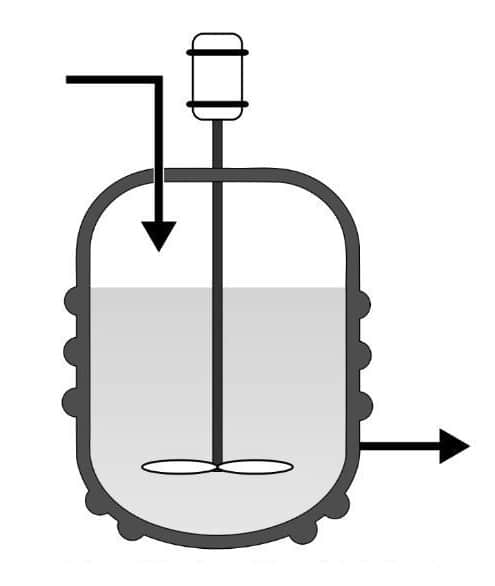
A semi-batch reactor can accept and process both continuous and batch inputs and outputs. These types of reactors combine continuous and batch processes. Raw materials and reactants are charged in semi-batch reactors. Chemicals are also added gradually over time as the process progresses.
With an agitator, the reaction mass will be stirred and uniform composition and temperature will be maintained throughout the reactor. The ability to add chemicals to a continuous process reaction is made possible by semi-batch reactions.
Semi-batch reactors also included jackets with facilities that could be used to heat or cool the reaction mass based on the needs of the chemical process.
Advantages and Disadvantages of Semi-batch Reactor
Advantages | Disadvantages |
---|---|
With a semi-batch reactor, multiple reactions can be carried out with more control over yield or selectivity. | The downside of the semi-batch process over the continuous process reactors (C.S.T.R. and P.F.R.) is that the capital expenditures per unit scale up quite significantly if we choose to scale it up. |
It is extremely useful when conducting exothermic reactions since it allows the flow rate of the other reactant to be modified. | More labor is needed to charge and discharge the reactor’s contents, clean the reactors and blades, etc. |
Read Also: How Does Air Conditioning System Work?[PDF]
#5 Nuclear Reactor
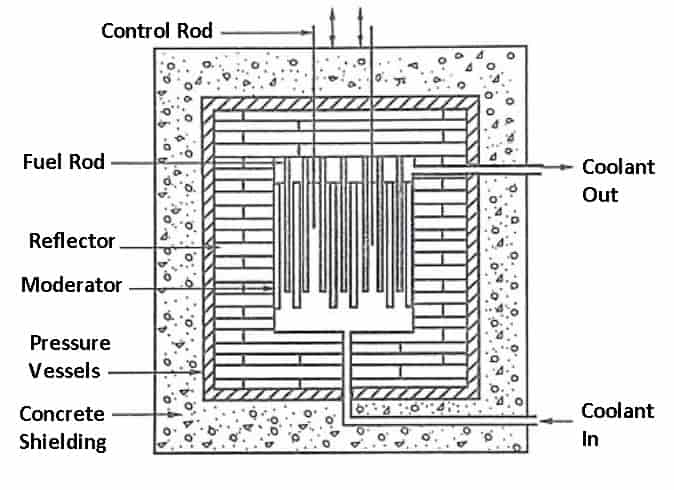
Nuclear reactors are designed to perform nuclear fission processes, which include the breaking of atoms to release energy. In this, nuclear fuel is used that is made from uranium, such as plutonium-239 and uranium-235.
These are intended to maintain the nuclear chain reactions under control. Nuclear power plants employ these reactors to produce electricity. Nuclear reactors react fuel to produce uranium dioxide powder, which is pressed and processed into hard ceramic pellets.
Then, the pellets are packed into tubes or fuel rods. The reactor’s capacity determines the number of fuel rods. Reactor vessel control rods consisting of various materials with properties to lessen the reaction are used to regulate the reaction. They are either inserted into the reactor core or withdrawn to increase the rate of reaction.
Applications of Nuclear Reaction
Nuclear reactors are employed in fundamental research, radioisotope manufacturing, radiography, neutron scattering, and material testing and characterization. They are also crucial resources for advanced training and instruction in nuclear technology for energy and other uses.
Read Also: Types of Wind Turbine: Horizontal Axis & Vertical Axis Turbine
#6 Catalytic Reactor
These reactors are driven mostly by catalysts, but also by mass and heat transfer. These are used in chemical synthesis, polymerization, hydrogen cracking, and other processes. These reactors’ common classification is determined by the catalysts’ movement pattern, which is as follows:
- Fixed Bed
- Trickle Bed
- Fluidized Bed
#1 Fixed Bed Reactor
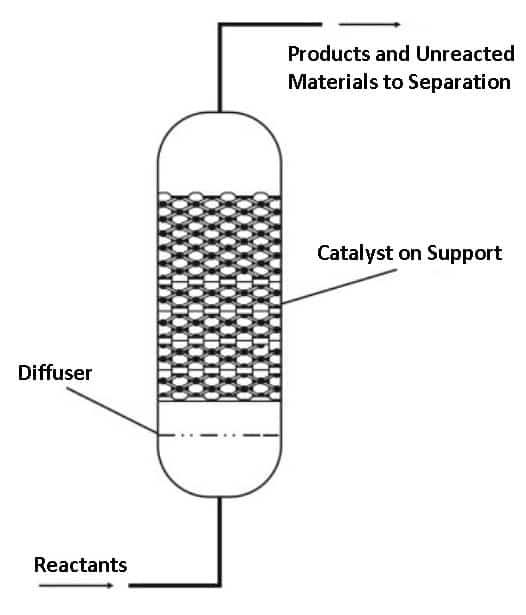
It is employed in gas-phase processes that are separately catalyzed. They can be assembled on a single tube or several tubes, depending on the needs.
Packed Beds and Multi-tube reactors are two popular types of reactors that fall under the Fixed Bed category.
#2 Trickle Bed
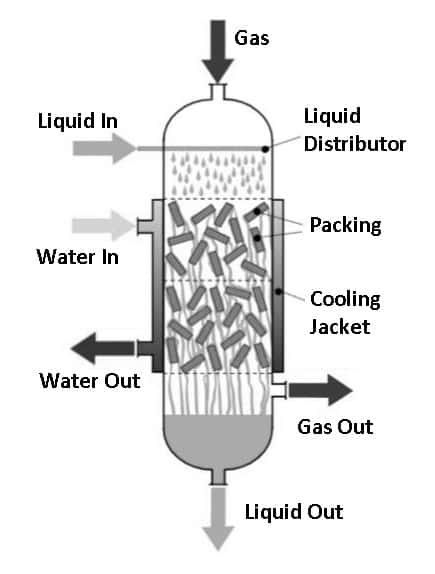
Trickle bed reactors contain a solid phase that acts as a catalyst for gas-liquid reactions. These reactions are mainly utilized for hydrogenation processes.
Liquid reactants enter from the top and flow downward, contacting the solid catalyst bed, while gas reactants enter from the cross-current direction for better contact.
#3 Fluidized Bed Reactor
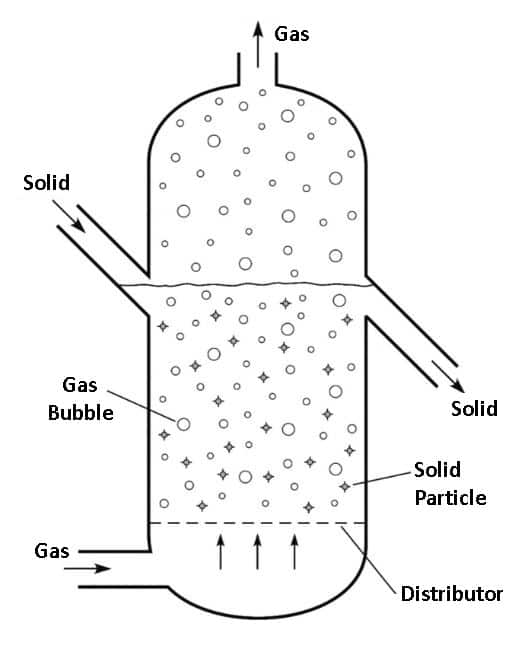
These types of reactors consist of a bed of solid particles that is supported by a gas or liquid flowing in an upward direction with such a velocity that it behaves as a fluid. The reactor used to study this phenomenon is referred to as a Fluidized Bed Reactor.
Conclusion
That’s it. Thanks for reading. I hope I have covered everything about the “Types of Reactors.” It would be helpful if you could let me know if there was anything I missed or if you have any doubts about anything I wrote.
Please share this article with your friends if you find it interesting.
Want free PDFs direct to your inbox? Then subscribe to our newsletter.
Download the PDF file of this article:
You might like to read more in our blog:
- What Are The Different Types of Furnaces?
- Understanding Different Types of Heat Exchangers
- Different Types of Refrigeration: Working, Parts, Uses
External links:
good website link
You,re welcome.