Hello readers! In this post, we’ll discuss what is a valve? and the different types of valves and their applications using illustrations.
You can also download the PDF file of this article the end.
Without further ado, let’s begin discussing what is a valve.
What is a Valve?
In simple terms, a valve is an internal component that controls and regulates the flow of fluid in a system by closing, opening, or partially cutting off the flow of a fluid for various reasons. Therefore, the valves are used to regulate the fluid’s flow and pressure within a system.
Valves are critical components in piping systems for controlling the flow of fluids, vapors, or gases. They offer an effective way to regulate the volume and pressure of gases or liquids that pass through pipelines.
It is important to understand which valve type is required for a specific application before installing it in pipework systems.
In this blog post, we’ll take a look over some of the most popular valve types used in piping and talk about how you can use them for particular applications.
If you want to learn more about valves, keep reading.
Related: What Are The Properties of Fluids? [Definitions]
Types of Valves
Following are the main types of valves:
- Gate valve
- Globe valve
- Ball valve
- Butterfly valve
- Check valve
- Plug valve
- Needle valve
- Pinch valve
- Diaphragm valve
- Solenoid valve
- Control valve
- Relief or pressure relief valve
- Piston valve
- Safety valve
- Poppet valve
- Rotary valve
- Thermostatic mixing valve
- Slide valve
- Pressure regulating valve
#1 Gate Valve
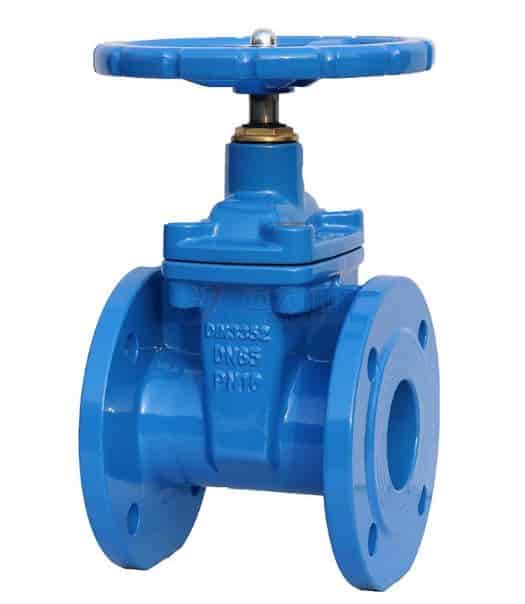
It is a valve that opens by moving a gate or barrier out of the way of the fluid. Sometimes this valve is also known as a sluice valve. It works by the disc (single disc or double disc) rotating back and forth in its body. It serves as a shut-off mechanism. Shutoff in double disc valves is good.
Gate valves can usually have rising or non-rising stems. Gate valves come in a range of sizes, from 12 mm to 300 mm and even larger. The gate valves are very compact and barely restrict fluid flow when fully open along the pipe axis.
Gate valves are lightweight, cost-effective, and provide minimal pressure drop. These valves can handle pressure up to 20 kg/cm2 and temperature up to 675 °C. Gate valves can be built from cast iron, carbon steel, stainless steel, ductile iron, bronze, and nickel alloys, among others.
There are various types of gate valves, including the following:
- Solid Wedge Gate
- Flexible Wedge Gate
- Split wedge or Parallel disks Gate
- OS & Y Gate, or (Rising Stem) of gate valves
#1 Solid Wedge Gate
The solid wedge disc type valve is very popular. These are used extensively in plants because it is very strong and has excellent simplicity. Installing this valve is incredibly flexible and can be done anywhere. This is suitable for the majority of fluids. It can be applied in turbulent flows as well.
#2 Flexible Wedge Gate
A flexible wedge gate valve is a solid disc that is one piece with a cut around the perimeter. The dimensions of this valve vary in shape, size, and depth.
The flexible wedge design is employed to reduce the complexity of the solid wedge problem. With this valve design, the seat alignment is improved and the leak tightness is improved.
#3 Split Wedge or Parallel Disks Gate
Split wedges are used to address the issues with both solid disc wedges and flexible wedge gates. It is made up of two discs connected parallel to one another.
It is usually spring-loaded and always stuck to the gate seat; there is also another type of split disk that is parallel. These are employed to control noncondensing gases and liquids at both low and high temperatures.
#4 OS & Y Gate Valve
OS & Y are also known as outside stem and yoke or outside screw and yoke. It is a valve used to regulate the water flow to fire sprinkler systems. These valves are controlled by a gate that opens and closes to control the lower into and rises out of valves.
Related: Understand The Different Types of Flow Control Valves
#2 Globe Valve
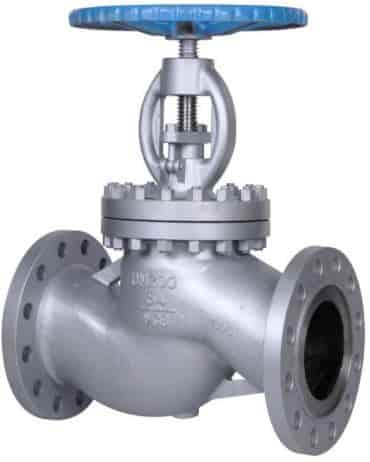
It is a type of valve used to control flow in a pipeline that has a generally spherical body with a movable plug or disc element and a stationary ring seat. It also works by a disc or plug rotating back and forth.
The name of this valve refers to the spherical shape of the body. It is divided into two halves by an internal baffle. An opening forms a seat onto which a movable plug can be screwed to close the valve.
The valve can be turned on or off manually, with power, or automatically. Globe valves come in sizes ranging from 12 mm to 300 mm. Their maximum operating temperatures and pressures are 550 C and 150 kg/cm2, respectively. The globe valve is made of carbon steel, stainless steel, ductile iron, brass, and other corrosion-resistant alloys.
Globe valves come in three different varieties:
- Z types
- Y types
- Angle types
#1 Z Type
The simplest type of globe valve design is the Z-type. A Z-shaped partition is located inside the tap of this globular body. These valves are designed to reduce manufacturing, installation, and maintenance problems. Z-type valves must be throttled because they don’t allow for pressure drop.
#2 Y Type
In order to solve the high-pressure drop issue in Z-type valves, Y-type valves were invented. Therefore, in order to simplify the Z-type problem, the Y-type is employed, where seats are angled at a 45° angle to the pipe’s axis. As a result, these valves are used in high pressure and a variety of other reproving services.
#3 Angle Type
These valves can change the direction of fluid flow by 90 degrees without the use of an elbow or an extra weld of pipe. In this valve, a disc has opened in opposition to the disk’s rise and fall. It is also capable of operating the slugging effect when fluctuating globe valves are used.
#3 Ball Valve
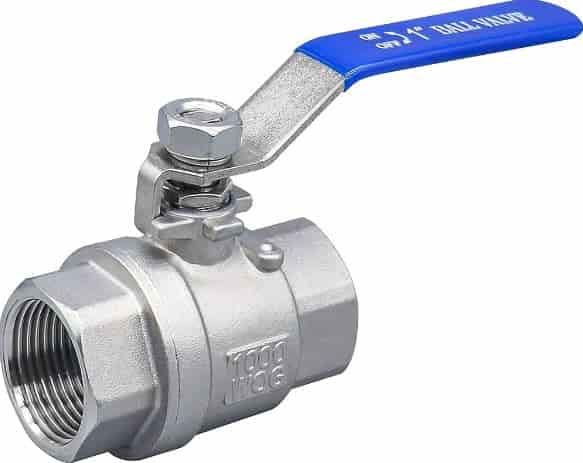
A ball valve regulates the flow of fluid through it using a hollow, perforated, and pivoting ball. A ball valve is open when its hole aligns with the flow inlet, and closed when the handle pivots it 90 degrees, blocking the flow.
In a ball valve, a ball rotates between resilient seats inside a two-way globe. It is small, low maintenance, and needs no lubrication.
It is offered in full, reduced, and venture port patterns. The ball can be rotated a quarter turn to open or close the valve. The ball valve usually provides poor throttling.
They have wide applications in industries that process chemicals. It is utilized when a combination of throttling and shutoff is necessary. The valve can be found in sizes ranging from 6mm to 900mm. It is suitable for temperatures and pressures up to 300 °C and 500 kg/cm, respectively.
There are various ball valve types, including:
- Standard
- Hydraulic
- Flanged
- Vented
- Brass ball
- PVC ball
- Stainless steel ball valve
Related: What are Pneumatic Valves? Working & Applications
#4 Butterfly Valve
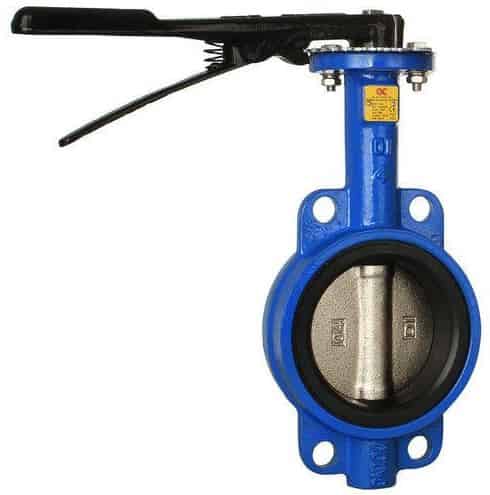
The controlling component of a butterfly valve is a disc known as a blade, vane, or flapper. This disc rotates in either a horizontal or vertical direction and permits the flow of fluid. These types of valves can be used for on/off operation or throttling at low-pressure drops.
These valves are inexpensive, simple to install, and prevent the accumulation of solids. Butterfly valves come in screw and wafer varieties. According to the design, it can be operated manually, electrically, or automatically.
Butterfly valves can withstand pressures of up to 80 kg/cm2. There are many sizes available for these valves starting at 50 mm and going up to 900 mm.
Butterfly valves come in handy when precise decisions need to be made quickly, such as in chemical and petrochemical plants and water treatment plants. They are often used in HVAC systems, which demand quick responses during temperature changes or when air ventilation needs to be adjusted.
The types of butterfly valves are as follows:
- Concentric Butterfly
- Eccentric Butterfly
- Wafer Type Butterfly
- Lug Type Butterfly and
- Double Flange Butterfly
#5 Check Valve
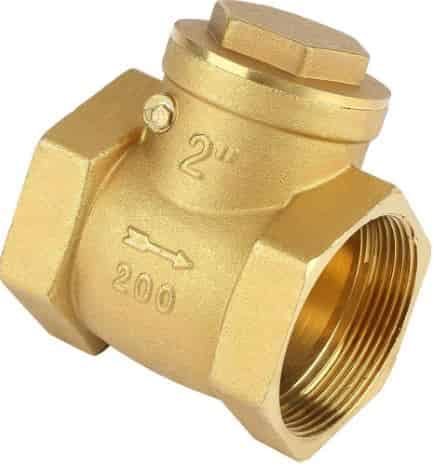
It is also referred to as a one-way valve or a foot valve. It is a valve that typically only allows liquid or gas to flow in one direction through it.
These valves are made of Inconel sheets because they are robust and chemically resistant, making them perfect for use in many global industries.
The use of check valves with pressure relief systems can ensure safety while regulating pressure and gas flow efficiently. These valve types can withstand both high and low-pressure situations. Check valves are available in both vertical and horizontal models.
The three different kinds of check valves
- Lift check valve
- Piston check valve
- Swing check valve.
#1 Lift Check Valve
This valve uses a disc, piston, or ball as a checking mechanism. It can be installed either horizontally or vertically. Lift check valves are appropriate for small pipelines and areas with significant pressure drops.
#2 Piston Check Valve
The stem controls the piston check valve. These valves come in sizes ranging from 6 mm to 600 mm and can be operated manually or by a motor. They are suitable for temperatures and pressures up to 675 °C and 170 kg/cm2, respectively.
#3 Swing Check Valve
This valve is utilized in situations with low fluid velocities and infrequent flow reversals. They are commonly used on the discharge side of pressure relief valves.
#6 Plug Valve
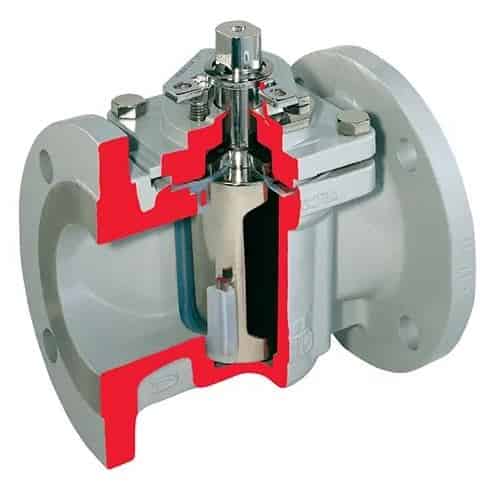
Plug valves are valves that have cylindrical or conically tapered plugs inside the valve body that can be rotated to control flow through the valve. During valve openings, fluid flows through the plugs in plug valves, which have hollow passageways going sideways.
Plug valves are easy to use and frequently affordable. Additionally, it is lightweight, requires little installation space, and has a large capacity. The materials used for plug valves include Inconel sheet, brass, aluminum, and stainless steel.
It can be applied to the handling of pulp and slurries. To change the flow direction, a plug valve can be made with one or more openings. It can be either lubricated or unlubricated.
There are plug valves in sizes ranging from 6 mm to 750 mm. They are capable of withstanding high temperatures of 300 °C and pressures of 300 kg/cm2.
Plug valves come in four different types.
- Lubricated Plug
- Non-Lubricated Plug
- Eccentric Plug
- Expanding Plug
#1 Lubricated Plug
Lubricated plug valves make use of lubricant. This lubricant is composed of a base oil and a viscosity improver that is added to reduce friction and seal ports under pressure between the face of the plug and the seat body.
#2 Non-Lubricated Plug
The non-lubricated plug has a tapered or cone-shaped body cavity that presses against a polymeric sleeve and acts as a wedge (chock). Non-lubricated plug valves are used in applications that require little maintenance.
#3 Eccentric Plug
The eccentric plug valves are used for applications that require a higher seating force and minimal friction from open to close.
#4 Expanding Plug
The expanding plug valve is used to avoid product contamination when double isolation is not necessary. This valve protects both seals from the flow path as it alternates between the open and closed positions.
Read Also: What is the Working Principle of Reaction Turbine?
#7 Needle Valve
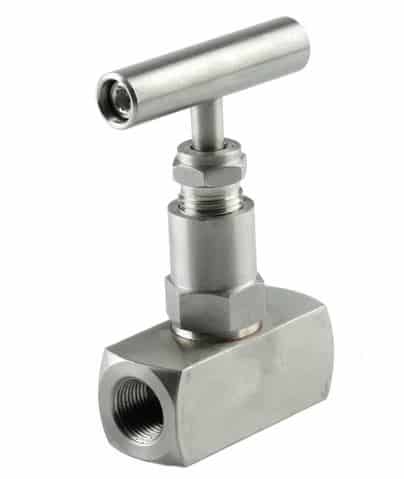
A needle valve has a tiny port and a plunger that is threaded and shaped like a needle. Generally, it can only regulate a low flow rate, but it allows precise flow regulation.
Needle valves are incredibly effective at controlling high-pressure liquids or gases, making them particularly useful in process piping systems.
This valve is employed for precise and small flows. The valve can be used in pressure and temperature ranges up to 260 C and 650 kg/cm, respectively.
Its size ranges from 3mm to 25mm. The use of needle valves reduces pressure fluctuations by controlling the actuating of air or hydraulic fluid.
#8 Pinch Valve
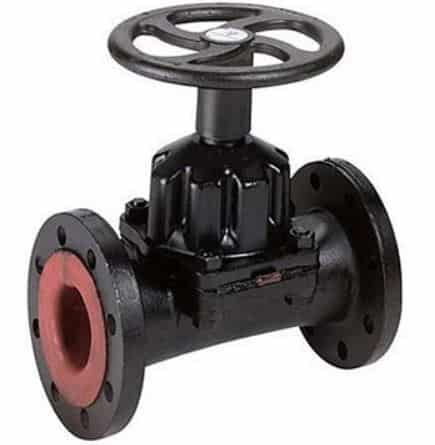
Pinch valves are full-bore or fully ported control valves that block fluid flow by creating a pinching effect. This valve can be employed for throttling and on-off operations.
The pinch valve is inexpensive to install, has little pressure loss, and requires little initial cost. It is appropriate for use when handling solid materials, slurries, and liquids.
Corrosion and contamination issues are resolved because its operation mechanism is totally isolated from fluid. It consists of replaceable sleeves that come in rubber or plastic varieties.
These valves can be made to withstand temperatures of up to 250°C and pressures of up to 20 kg/cm2. These types of valves should not be used in vacuum situations. Pinch valves use a linear motion.
Pinch valve types include the following:
- OM Mechanical Pinch Sleeves
- OV Mechanical Pinch
- VM Air Operated Pinch
- VF Air Operated Pinch
- VT Air Operated Tanker Pinch
- VMF Air Operated Pinch
- VMP Air Operated Pinch
#9 Diaphragm Valve
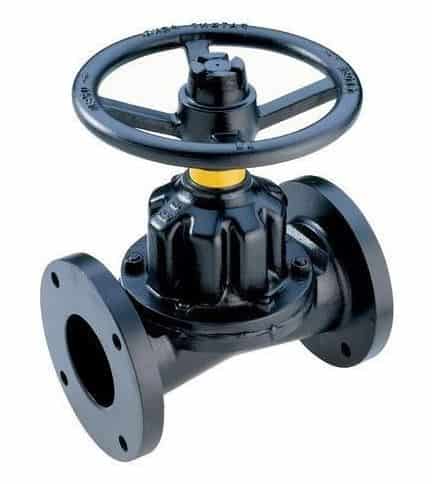
Basically, diaphragm valves are composed of a valve body with two or more ports: a flexible diaphragm, and a seat or weir where the diaphragm closes. Depending on the intended use, the valve body may be made of plastic, metal, wood, or another material.
There are two types of diaphragm valves: weir type and straight-through type. It is necessary for weir-type diaphragm valves to have relatively low thrust and shut-off strokes.
This prolongs the diaphragm’s life. The straight-through type diaphragm valve can handle slurries, viscous liquids, and fibrous suspensions.
The diaphragm is made of rubber, neoprene, or buna. It is available in sizes ranging from 3 mm to 600 mm. It can withstand pressures of up to 20 kg/cm2 and temperatures of up to 2200 C.
Read Also: What is Impulse Turbine and Pelton Wheel?
#10 Solenoid Valve
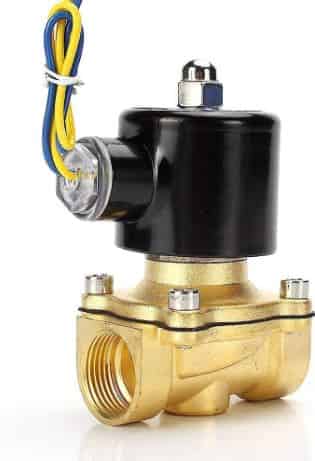
There are different types of solenoid valves depending on the type and characteristics of the electric current, the strength of the magnetic field, and the mechanism used to regulate the fluid.
The mechanism ranges from linear action, pivoted-armature actuators, rocker actuators, and plunger-type actuators.
This valve has two ports that can be used to control a flow and three or more ports that can be used to switch flows between ports. Solenoid valves are the most commonly used mechanisms for control in fluidics. They are employed to turn off, release, dose, distribute, or mix fluids.
They can be found in a variety of applications. There are many benefits to using solenoids, including fast and safe switching, high reliability, long service life, good medium compatibility of the materials used, low control power, and compact design.
#11 Control Valve
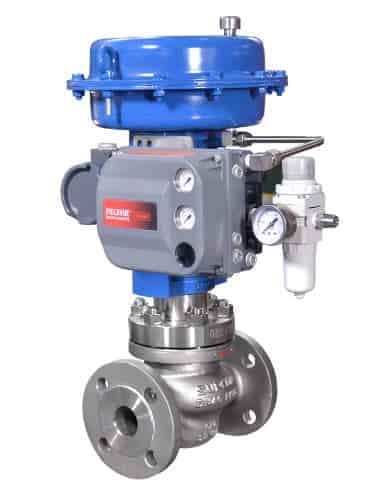
The control valve changes the flow passage size according to a signal from a controller to control fluid flow. It allows direct control of flow rate, and consequently pressure, temperature, and liquid level, in the process.
The actuator and body are the two main components of a control valve. The actuator receives the signals from the process and acts accordingly to close or open the valve. Control valves can have a butterfly or diaphragm design, as well as single or double-balanced globe plugs.
Sizes for control valves can range from 3 mm to 500 mm. They can withstand pressures of up to 4000 kg/cm2 and temperatures ranging from 250 °C to 800 °C.
#12 Safety Valve
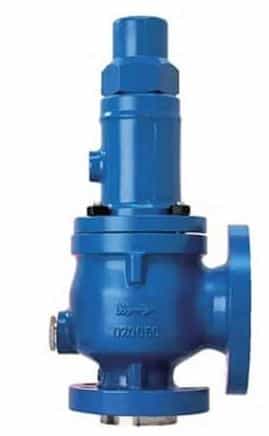
A safety valve is an emergency shutoff valve. An example of a safety valve is a pressure relief valve (PRV), which is designed to release a substance when a threshold pressure or temperature is exceeded.
A specific type of pressure safety valve are pilot-operated relief valve. During the Industrial Revolution, safety valves were initially created for steam boiler use. The early boilers that failed to use them were highly prone to explosions.
Safety valves are used in a variety of applications, such as boilers, pressure vessels, and piping systems. The main drawback of using a safety valve is that, if not maintained properly, it may malfunction.
Read Also: What are the applications of centrifugal pumps?
#13 Relief Or Pressure Relief Valve
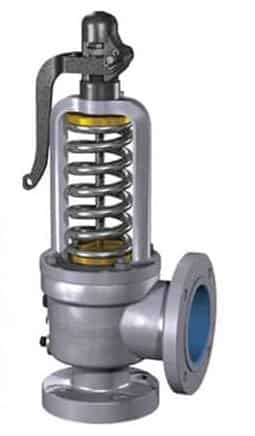
This type of valve controls or limits the pressure in a system; excessive pressure could otherwise lead to a process upset, instrument failure, explosion, or fire.
It guards against potential harm, reduces equipment failure, and regulates pressure in a system with a point of release. Relief valves can be turned on or off manually or automatically.
These valves serve as an essential safety component in a variety of industrial and commercial applications. The drawback of using relief valves is that they may not always be effective at regulating system overpressure or temperature spikes.
The types of pressure relief valves are as follows:
- Spring-loaded pressure relief,
- Balanced Bellows and Balanced Piston valves
- Safety relief
- Pilot operated pressure relief and
- Power actuated pressure relief
#14 Piston Valve
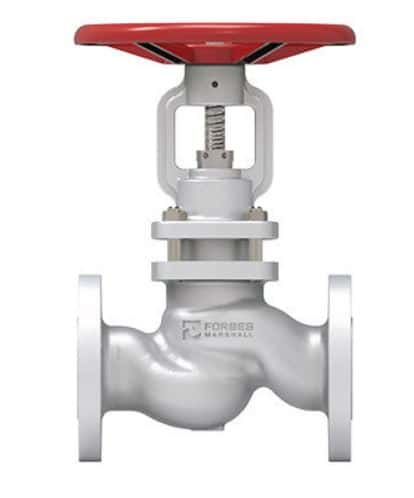
A piston valve uses the linear motion of a piston within a chamber or cylinder to control the flow of a fluid along a tube or pipe. Depending on whether they are fully open or fully closed, they control when steam, gas, and other fluid services are turned on and off.
These valves have excellent control abilities. Since the piston travels by sealing packs during opening and closing, it can also be used for liquids containing solid particles. They work well with gaseous fluids as well.
The piston valve consists of a full port made of forged steel, its maximum operating pressure is 135 bar/1973 psi, and its maximum operating temperature is 427°C/800°F.
#15 Poppet Valve
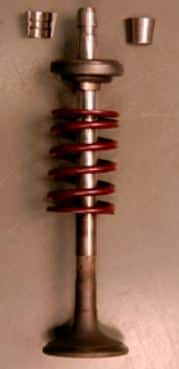
It is a valve that has many uses besides controlling the timing and volume of gas or vapor flowing into or out of an engine.
It consists of a plug that is typically shaped like a disc at the end of a shaft known as a valve stem and a hole or open-ended chamber that is typically round or oval in cross-section.
Typically, this plug’s working end, called the valve face, is ground at a 45° angle to seal against a valve seat ground into the chamber’s rim. The valve passes through a valve guide to keep the shaft centered.
Compared to other engine valve types, poppet valves have many advantages including faster response times, more performance, lower friction, less susceptibility to contamination, and lower costs.
#16 Rotary Valve
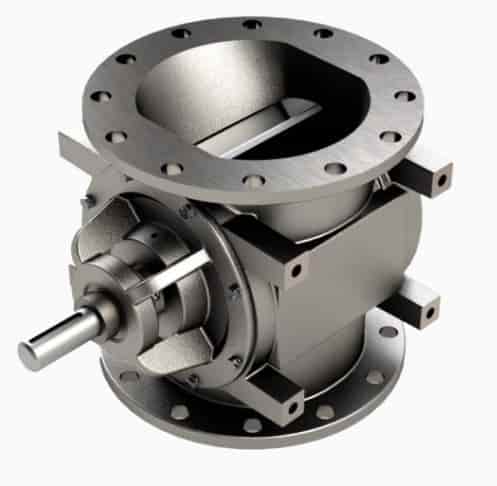
This valve controls the flow of liquid or gas through the connected pipes by rotating one or more passages in a transverse plug. The most basic type of rotary valve is a stopcock.
Its advantages include significantly higher compression ratios and rpm, meaning more power, a more compact and lightweight cylinder head, and less complexity, leading to greater reliability and lower costs.
These types of valves are primarily found in the Corliss steam engine, regulate the steam and exhaust ports of steam engines. It is also used to change the pitch of brass instruments. These valves are most often found in two-stroke and four-stroke engines.
#17 Thermostatic Mixing Valve
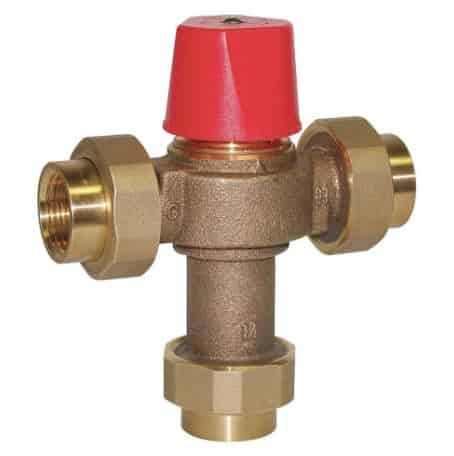
This valve mixes hot and cold water to maintain consistent, safe shower and bath outlet temperatures and prevent burning.
A wax thermostat is commonly used to regulate thermostatic mixing valves. They also shut down quickly if a hot or cold supply fails, preventing scalding or heatstroke.
A TMV works by maintaining a predetermined temperature, allowing you to take relaxing showers without being concerned about being scalded or frozen. TMVs can cost more to install than standard faucets or showers. TMVs have a shorter lifespan, just like any mechanical device.
These devices for controlling water temperature can be divided into three main categories: Heat Source, Group Control, and Point-of-Use.
#18 Slide Valve
The slide valve is a rectilinear valve that regulates the flow of steam into and exhaust out of a steam engine’s cylinder.
In this valve, the upper and lower valves were connected by a rod or spindle, and the stem or tube connecting them was hollow, so the upper end of the cylinder was used as an induction pipe. As a result, two valves could perform the tasks of four.
This valve is lightweight, has no wedging action, and has a short overall length. The powering of slide valves is simple. Large-size slide valves are used in the power industry’s main steam and feed lines to isolate different parts of the plant.
#19 Pressure Regulating Valve
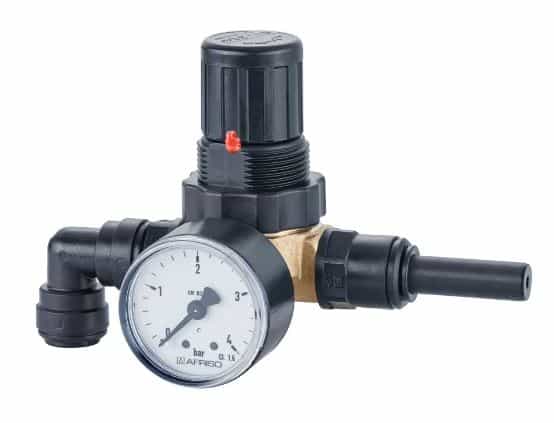
A pressure regulating valve regulates the pressure of the fluid by receiving negative feedback from the controlled pressure. These are used to control the flow of gases and liquids.
They can be independent pressure sensors, controllers, and flow valves, or they can be an integral devices with a pressure setting, a restrictor, and a sensor all in one body.
The pressure regulating valve can be divided into two categories: back-pressure regulators and pressure reduction regulators.
Pressure-reducing regulators reduce the input pressure of a fluid to a desired value at its output. Back-pressure regulators keep the set pressure in the inlet by opening to allow flow when the inlet pressure exceeds the set point.
These types of valves are made to be clog-free and are simple to install. These are capable of being built with automatic high-pressure control. A pressure regulator is typically used to protect electric heaters, as well as hot water storage and appliances.
Final Thought
That’s it. Thanks for reading. I hope I have covered everything about the “Types of Generators.” It would be helpful if you could let me know if there was anything I missed or if you have any doubts about anything I wrote.
Please share this article with your friends if you find it interesting.
Want free PDFs direct to your inbox? Then subscribe to our newsletter.
Download PDF of this Article:
You might want to read the following articles:
- Understand The Different Types of Pumps Explained
- What is Vibration? Free, Forced, and Damped Vibration
- Different Types of Welding Machines & Their Applications
External links: