In this article, you will learn about broaching machines, types of broaching machines, Broaching operations, and Advantages.
What is a Broaching Machine?
Broaching is a method of removing metal by pushing or pulling a cutting tool called a broach which cuts in a fixed path.
In a broaching machine, the tool of the machine is pulled or pushed through the surfaces to be finished. With the help of broaching, finishing is done on flat or contoured and either internal or external surfaces. Broaching is limited to the removal of about 6mm of stock or less.
The term “broaching” may have derived from an ancient Roman word
The operation itself dates only to the 1850s when broaching tools called “drifts” were hammered in blacksmith shops through the work or pushed with an arbor press.
Read also: What Are The Types of Lathe Machines?
Types of Broaching Machine
Following are the types of broaching machine
- Horizontal broaching machine
- Vertical broaching machines
- Surface broaching machines
- Continuous broaching machine
Broaching machines are the simplest of all machine tools. The broaching machine consists of a broaching tool, a work-holding fixture, a drive mechanism, and a suitable supporting frame. Although the parts are few, several variations in design are possible.
There are two principal types of broaching machines: horizontal and vertical.
In addition to these standard types, there are special and continuously operating machines. Both horizontal and vertical types of machines have one or more rams depending on production demand.
Dual-ram models are arranged so that when one ram is on the cutting stroke, the other is on the return stroke; the return stroke is performed quickly to gain time, which is used to unload and load the machine.
Broaching machines usually pull or
Horizontal Broaching Machine
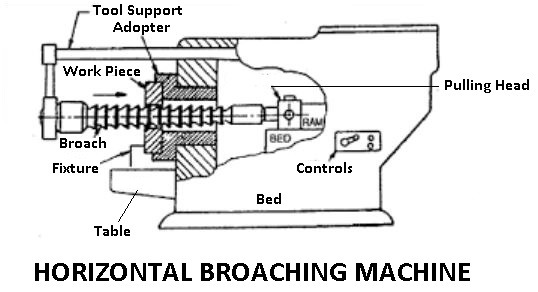
Nearly all horizontal machines are of the pull type. They may be used for either internal or external broaching, although internal work is the most common.
A horizontal broaching machine is shown in the figure. It consists of a bed or a base a little more than twice the
Horizontal broaching machines are used primarily for broaching keyways, splines, slots, round holes, and other internal shapes or contours. They have the disadvantage of taking more floor space than do the vertical machines. However, long broaches and heavy workpieces are easily handled.
Vertical Broaching Machine
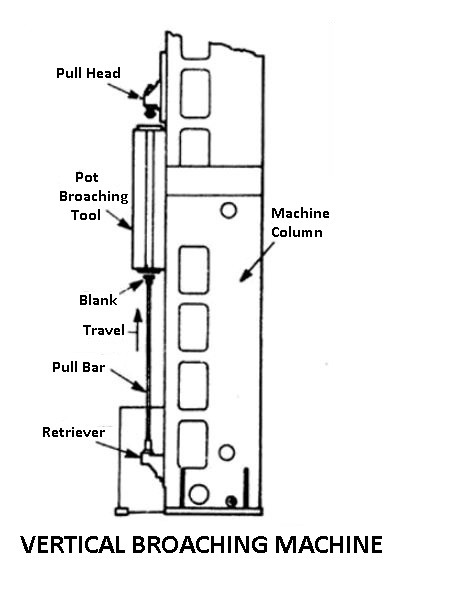
The vertical types may be obtained in either push or pull type. The push type is the most popular. A vertical broaching machine is shown in the figure.
Vertical machines are used in multiple operations since they are convenient for passing work from one machine to another. Pull down, pull up, and push down are the three kinds that are offered; pull up being the most common. Vertical machines require an operator platform or a pit and are more economical in floor space than the horizontal type.
Modern vertical broaches are offered with both hydraulic and electro-mechanical drives. But hydraulic drives are the most common because they cost less. A vertical hydraulic broaching machine is illustrated in the above figure.
Surface Broaching Machine
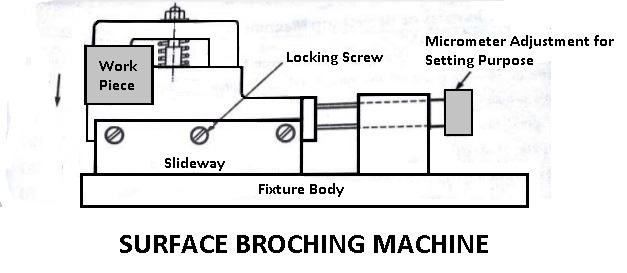
Surface broaching machines have their broaching tools attached to
On some surface broaching machines, the ram travels horizontally, on others, the ram travels vertically. When two rams are used, the machine is called a duplex broach.
Continuous Broaching Machine
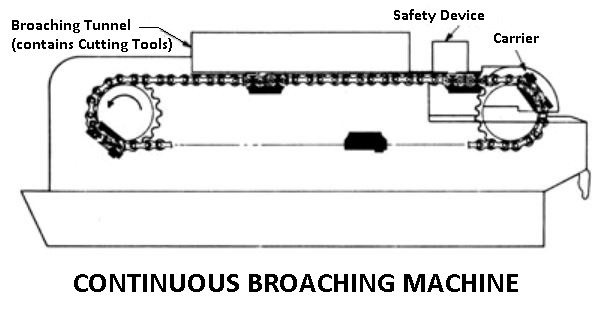
The continuous-broaching process is applied on rotary or horizontal continuous-broaching machines for the mass manufacturing of tiny parts.
In the rotary continuous broaching machines, the workpiece is loaded on the table which rotates
In the horizontal continuous broaching machines the workpieces travel as they are carried by an endless chain. The workpieces are loaded into work-holding fixtures mounted on the continuously moving chain. During the operation, the broach is stationary as before. Such machines are used for broaching small parts.
Read Also: Shaper Machine and Its Types
Broaching Methods
Following are the classification of broaching methods:
- Pull Broaching
- Push Broaching
- Surface Broaching
- Continuous Broaching
Pull Broaching
In the pull broaching the work is held fixed and the broach is pulled through the work. Usually, broaches are very long and are held in a special head. The pull broaching method is used for internal broaching but it is also used for some surface broaching.
Push Broaching
In the push broaching the work is fixed and the broach is pushed through the work. Hand and hydraulic arbor presses are commonly used for push broaching. This method is used for sizing holes and cutting keyways.
Surface Broaching
In surface broaching either the work or the broaching tool moves across the other. This method has become an important means of surface finishing. Many irregular or intricate shapes can be broached by surface broaching, but the tools must be specially designed for each job.
Continuous Broaching
In continuous broaching, the work is moved continuously and the broach is held stationary. The movement of work may be either straight horizontal or circular. The continuous broaching method is mostly used for broaching many similar works at the same time.
Broaching Machine Operations
Broaching is applied for machining various internal and external surfaces, for round or irregularly shaped holes from 6 to 100mm in diameter, and for external flat and contoured surfaces.
Certain types of surfaces, for example, spline holes, are machined at present only by broaching due to the exceptional difficulties in machining such surfaces by other methods.
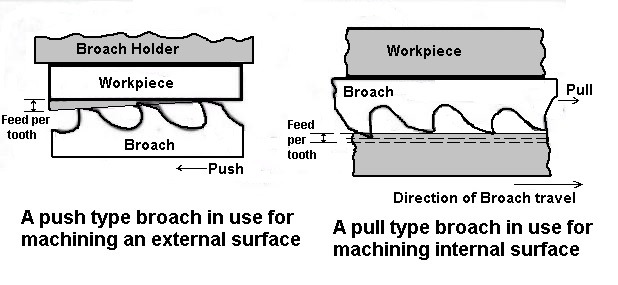
Some important broaching operations are illustrated below. Some operations are done in one pass, but some operations are arranged for repeated cuts to the design of the broach.
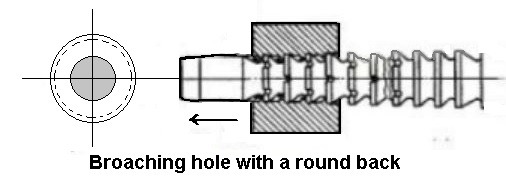
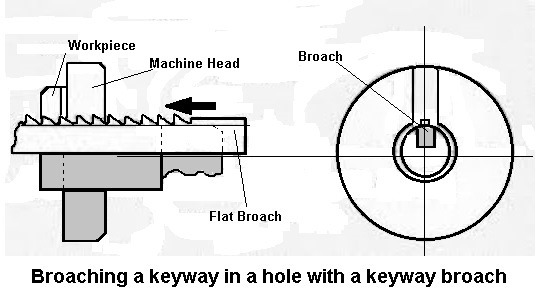
The teeth of a gear or spline may be broached all together or one or a few at a time. A comparatively simple broach can be made to cut one or a few tooth spaces. After one pass, the gear blank is indexed and more of its teeth are cut. Successive passes are made until all the teeth are finished.
Advantages of Broaching
Following are the features and advantages of the broaching:
- The rate of production is very high.
- Skill is required from the operator to perform a broaching operation. In most cases, the operator merely loads and unloads the workpiece.
- High accuracy and a high class of surface finish are possible. A tolerance of ±0.0075mm and a surface finish of about 0.8 microns (1 micron=0.001mm) can be easily obtained in broaching.
- Both roughing finishing cuts are completed in one pass of the tool.
- The broaching process is used for internal and external surface finishing.
- Any form or shape that can be reproduced on a broaching can be machined.
- Cutting fluid may be readily applied where it is most effective because a broach tends to draw the fluid into the cut.
Disadvantages of Broaching
On the other hand, there are certain disadvantages to using the broaching method. They are as follows:
- High tool cost. A broach normally does only one job and is expensive to make and sharpen.
- Very large workpieces cannot be broached.
- The surface to be broached cannot have an obstruction.
- Broaching cannot be used to remove a large amount of stock.
- Parts to be broached must be capable of being rigidly supported and must be able to withstand the force that is set up during cutting.
Application of Broaching
This is a crucial manufacturing procedure that produces items with accurate dimensions and a smooth surface. Here are a few of the applications:
- Broaching is used in the automobile industry to manufacture gear teeth.
- Additionally, keyways for pulleys are made with it.
- It is used in the casting and forging processes to create grooves.
- This is also utilized for various part machining in agriculturally oriented companies.
- It is employed to punch intricate designs into the workpiece.
Conclusion
That’s it thanks for reading. So now, we hope that we have cleared all your doubts. If you have still any doubts about the “Types of Broaching Machine” you can contact us or ask in the comments.
If you like our article then please share it with your friends.
Subscribe to our newsletter to get notified when we upload new posts.
Read More About Machines On Website:
- Milling Machine: Parts and It’s Working Principle
- 13 Difference between NC, CNC, and DNC Machine
- Press Machine & Types of Press Machines
FAQs
All tools work according to the same principle, regardless of manufacturer. The cutting tool’s centerline is inclined at a 1° angle to the workpiece centerline. As the broach is fed into the workpiece, it shears its way into the part with a scalloping effect.
Aluminum, Brass, 12L14, Alloy Steel. Stainless Steel and Titanium.
Thanks for this complete information on broaching machine.
You’re most welcome.
Hi there,
Thanks for sharing a complete information about broaching machine, their types, advantages, operations and broaching methods. your blog is very informative and helpful for us. I really like the point of “Types of Broaching Machine”. This point is clearly described with images.
keep updating…
You’re most welcome. Keep visiting 🙂