In this post, you learn what is electron beam machining, how it’s done, Its working principle, advantages, accuracy and limitations.
Electron Beam Machining
Electron beam machining is the metal removal process by a high-velocity focussed stream of electrons which heats, melts, and vaporizes the work material at the point of bombardment.
The production of free electrons is obtained from thermo-electronic cathodes wherein metals are heated to the temperature at which the electrons gain enough speed to escape to the space around the cathode.
The acceleration of the electrons is carried by an electric field while the focussing and concentration are done by controlled magnetic fields.
The kinetic energy of a beam of free electrons is transformed into heat energy as a result of the interaction of the electrons with the workpiece material. EMB is, therefore, a thermo-electric process.
Read Also: What are the Types of Unconventional Machining Process?
Parts of Electron Beam Machining
The EBm machine consists of various parts, which are as follows:
- Cathode
- Annular Bias Grid
- Anode
- Magnetic Lenses
- Electromagnetic Lens
- Deflector Coils
- Vacuum Chamber
- Workpiece
#1 Cathode
The cathode has a negative charge and is used to create electrons.
#2 Annular Bias Grid
The annular bias grid is positioned near the cathode. The bias grid’s spherical design prevents the bend of electrons created by the cathode. It operates the electron gun in pulse mode and serves as a switch.
#3 Anode
The anode is positively charged and is placed after the annulus bias grid. The electron beam is drawn to an annular anode, eventually accelerating as its velocity rises. The velocity of the electron beam decreases to half that of light as it exits the anode segment.
#4 Magnetic Lenses
By using magnetic lenses, electron beams are shaped, and their deviation is reduced. Only convergent electrons can pass through it and occupy electrons with low energy deviations. The beam’s quality is enhanced by doing this.
#5 Electromagnetic Lens
As the electron beam approaches the workpiece, electromagnetic lenses are used to focus and control it. Using electromagnetic fields, these lenses bend and direct electrons toward the desired location.
#6 Deflector Coils
The deflector coil increases pore size and precisely directs the high-velocity electron beam to the desired area on the workpiece.
#7 Vacuum Chamber
The vacuum chamber is a completely enclosed space that prevents air or other gases from impacting the electron beam as it moves from the gun to the workpiece. A vacuum keeps the electrons from scattering or losing energy as they move through the chamber.
#8 Workpiece
The material being machined is known as the workpiece. Typically, it is constructed from a conductive material like metal or an alloy.
Read Also: Understand Types of Welding Rods & Their Uses [Explained in Details]
Construction of Electron Beam Machining
The figure shows the schematic layout of electron beam machinings (EBM). It includes a work table, diaphragm, focusing lens, and an electron gun. A vacuum is necessary to prevent accelerated electrons from striking air molecules.
Therefore, the entire EBM setup is contained in a chamber that maintains a vacuum of the order of 10-5 to IO-6 mm of mercury. The workpiece is placed on the table through this chamber, which also serves as a door. Then, the door is closed and secured.
Read Also: 12 Types of Forging Defects [Their Causes & Remedies]
Working of Electron Beam Machining
The figure shows the principle of operation of electron-beam machining. A beam of electrons is emitted from the electron gun, which is a triod consisting of:
- A cathode is a hot tungsten filament (2500°C) emitting high -ve potential electrons.
- The grid cup is negatively based on the Filament.
- An anode is kept at ground potential, and through which the high-velocity electrons pass.
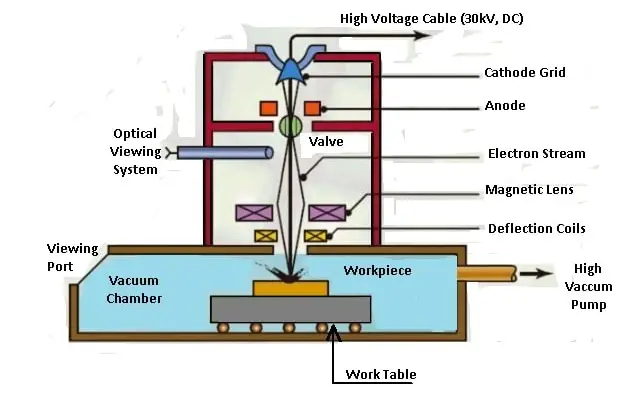
- A gun is provided with an electric current from a high-voltage dc source.
- The flow of electrons is regulated by the -ve bias applied to the grid cup.
- Electrons passing through the anode are accelerated to two-thirds of the velocity of light by applying 50 to 150 kV at the anode, and this speed is maintained till they strike the workpiece.
- Due to the pattern of the electrostatic field produced by the grid cup, the electrons are focussed and made to flow in the form of a converging beam through a hole in the anode.
- A magnetic deflection coil is used to make the electron beam circular having a cross-sectional diameter of 0.01 to 0.02 mm, and deflect it anywhere.
- The built-in microscope with a magnification of 40 on the workpiece enables the operator to accurately locate the beam impact and observe the machining operation.
- As the beam impacts on the workpiece surface, the kinetic energy of high-velocity electrons is immediately converted into thermal energy, and it vaporizes the material at the spot of its impact.
- Power density is very high (about 1.5 billion W/cm’). It takes a few microseconds to melt and vaporize the material on impact.
- The process is carried out in repeated pulses of short duration.
- The pulse frequency may range from 1 to 16,000 Hz, and the duration may range from 4 to 64,000 microseconds.
Read Also: Know About Different Types of Springs and Their Applications
Characteristics of EBM
- The electron beam machine generally works in pulse mode, and this biasing is achieved by an annular biased grid.
- Low beam currents between 200 μamp and 1 amp are possible.
- The EBM machine produced pulses with durations ranging from 50 s to 15 ms.
- It contains 100 j of energy per pulse.
- It uses voltages between 150 and 200 kV and accelerates electrons to a speed of about 200,000 km/s.
Accuracy of EBM
Tolerances are about 10% of the hole diameter or slot width. The taper of about 4° included angle is present in slots and holes, and this limits the depth-to-width ratio. A depth-to-diameter ratio can reach 20:1 with multiple pulses.
Heat-affected zones of up to 0.03 mm deep have been observed. The stock removal rate is generally in the region of 1.5 mm/s with a penetration rate of about 0.25 mm/s or faster.
Read also: Abrasive Jet Machining (AJM): Working Principle, Advantages & Applications
Design Consideration of EBM
- EBM can produce holes of diameter in the range of 100 μm to 2mm with a depth up to 15mm, i.e., with a length/diameter ratio of around 10.
- Burr formation doesn’t occur in electron beam machining
- The heat-affected zone is narrow due to the shorter pulse duration in EBM.
- Many holes are drilled per second depending on the diameter of the hole, power density, and depth of the hole. as well as material type.
- Electron beam machining does not apply cutting force on the workpiece.
Read Also: What Are Different Types of Pulleys & Their Uses?
Applications of EBM
Some typical applications of the process are:
- Drill fine gas orifices, less than 0.002 mm, in space nuclear reactors, and turbine blades for supersonic aero-engines.
- To produce wire drawing dies, light-ray orifices, and spinnerets to produce synthetic fibers.
- Produce metering holes in injector nozzles in diesel engines, etc.
- To scribe thin films.
- EBMs are used to remove small broken taps from holes.
Advantages and limitations of EBM
- EBM is an excellent method for micro-finishing. It can drill holes or cut slots that otherwise cannot be made.
- It is possible to cut any known material, metal or nonmetal, that can exist in a vacuum.
- No cutting tool pressure or wear. Distortion-free machining having precise dimensions can be achieved.
- The biggest disadvantage is the high equipment cost and employment of highly skilled operators.
- Besides, only small cuts are possible. Further, the need for a vacuum restricts the size of specimens that can be machined.
Closing It Up
That’s it. Thanks for reading. If you have any questions about “Electron-beam Machining,” ask in the comments section. If you like this article, share it with your friends.
Want free PDFs in your inbox? Then subscribe to our newsletter.
Read also: