In this article, you’ll learn what is Sprocket? And their Working, Applications, and Types of Sprockets. You can also download the PDF file of this article at the end of it.
What is Sprocket?
A Sprocket is commonly a wheel with teeth that lock onto a chain. When the sprocket rotates, the teeth hold the chain and move the other parts attached to the chain. This operation provides simple and controlled rotational movement of large equipment and machinery.
A sprocket is manufactured with metal or reinforced plastic to handle the force of the moving chain. These components are compared to gears, which serve the same wheel-shaped design with teeth.
Sprockets make direct contact with a variety of chain rings or unlike gears which interlock together to transfer rotational movement. Instead of gear systems, most sprockets operate in bicycle chain assemblies.
Sprockets are parts that are made with specific chain rings to correctly fit and handle specific loads. Choosing incorrect sprockets can cause you heavy loss and teeth will chip or breaks. On the other hand, the sprockets in their chains can move without breaking, even in heavy-duty conveyor system applications.
Read Also: 14 Different Types of Washers and How To Use Guide ? with [Pictures & PDF]
Classification of Sprockets
Sprockets are classified according to type A, type B, type C, and type D, which are described below:
1. Type A
This sprocket is flat and has no hub on it. These are typically mounted on the flanges or hubs of the equipment. They drive through a series of holes that are plain or thin.
2. Type B
This sprocket made with a hub on its one side. This allows the sprocket to fit closely to the machinery on which it is mounted. Due to this, it reduces a large overhang load on the bearings of the equipment.
3. Type C
Type C sprockets are made with a hub on its both side of the plate. It is typically used in such applications where the pitch diameter is large and there is more weight to support on the shaft. Larger loads require bigger hubs.
4. Type D
These sprockets use a Type A sprocket mounted on a solid or split hub. The sprocket is easily splinted for removal and bolted to the hub. No need to remove bearings and other equipment because without it the speed ratio can be changed.
Types of Sprockets
Following are the main types of sprockets:
- Chain sprockets
- Duplex sprockets
- Industrial sprockets
- Drive sprockets
- Triplex sprockets
- Shaft sprockets
- Simplex sprockets
- Single pitch and double pitch sprocket
- Drum sprockets
- Steel split sprockets
- Idler sprocket
- Bushed sprocket
- Multi-strand sprocket
- Quick disconnect sprocket
- Taper-lock sprocket
- Double plus sprocket
1. Chain Sprocket
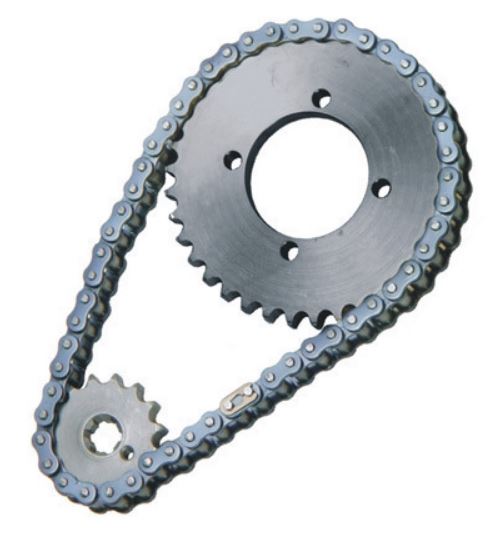
These are the most common types of sprockets used. They work only with chains designed by rollers interconnected by pins.
Roller chains provide a gap that fits the teeth of the sprocket to transfer rotary motion. These are used in transmission equipment applications.
2. Duplex Sprocket
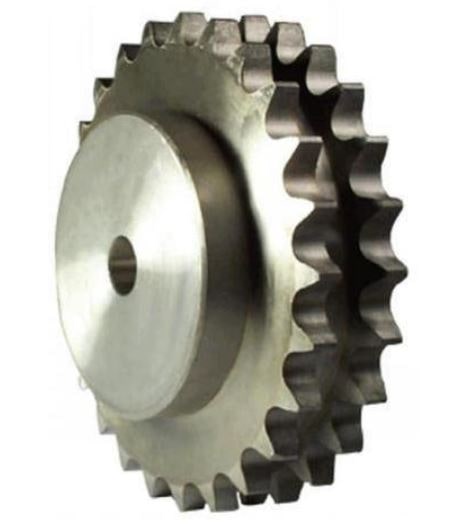
The duplex sprockets are usually made of mild steel and sometimes of stainless steel in many different sizes. It mainly consists of double-strand sprockets from the outer diameter of 2″ to 120″ in the plate.
It is maybe of a single hub or double hub as per the required specifications. And Induction/Flame hardened teeth Duplex Sprockets are also available.
3. Industrial Sprocket
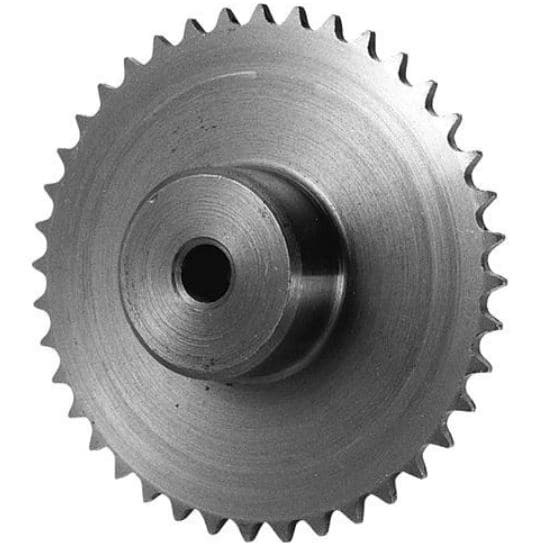
The industrial sprockets are commonly made of graded stainless steel, mild steel, and cast iron because they give high tensile strength and efficiency.
Different types of sprockets can be manufactured by their originator to achieve greater efficiency. They are generally used with timing belts, have flanges to keep the timing belt centered.
4. Drive Sprocket
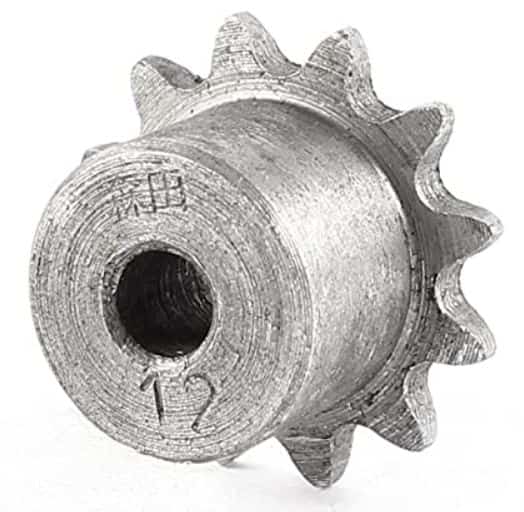
The drive sprockets are a common type of sprockets. These are usually provided with shaft import power. They are available with a smaller diameter.
5. Triple Sprocket
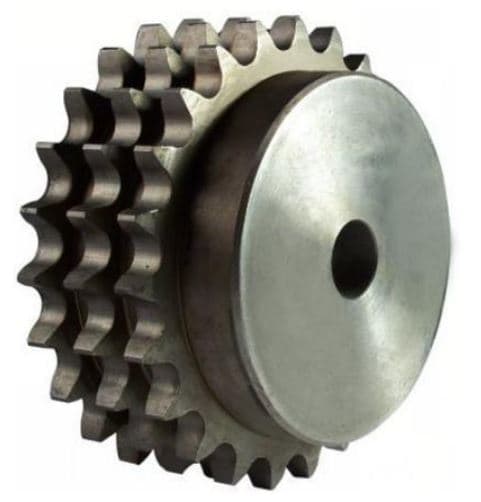
The triple sprocket is a triple 18 tooth taper bushed type sprocket that uses bushing. It is constructed using high-quality mild steel and fabricated with high precision tolerances for optimum long-term performance. These sprockets are consist of heat-treated hardened teeth that further improve the working and durability.
6. Shaft Sprocket
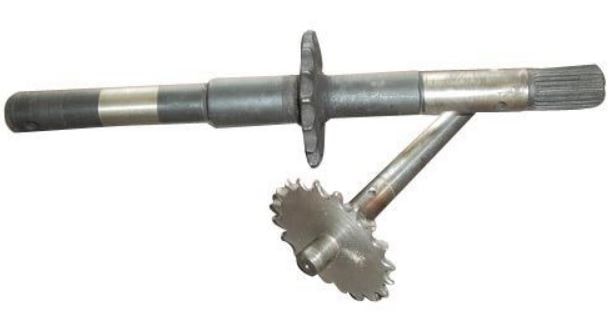
It is a type of sprocket, typically made of welded steel, either in one piece or with replaceable tooth segments for the drive and tail sections. They are commonly used for ash handling applications. These types of sprockets are available with any number of teeth or hub designs.
7. Simplex Sprocket
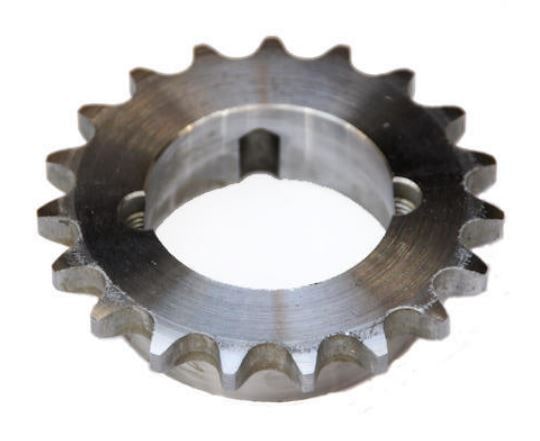
It is divided by a gear in which the sprocket is not directly joined together, and in that, it is separated by a pulley. They are commonly made of teeth and smooth pulleys. The simplex sprockets usually do not have a flange.
8. Single Pitch and Double Pitch Sprocket
Pitch sprockets are available with single pitch and double pitch sprockets. The single-pitch sprockets have teeth that enable the chain’s roller pin to fall into each tooth. Whereas the double pitch sprocket has teeth that allow the pin to fall into each gap. This type of sprocket is used in conveyor systems because they require precise product placement.
9. Drum Sprocket
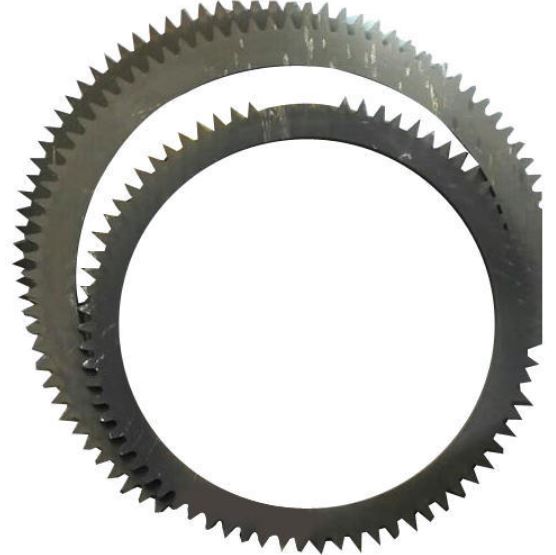
These sprockets are stronger and thicker sprockets that focus on reducing contact pressure through the increased surface area. Teeth, plates, and hubs are used very wide to reduce wear. Drum sprockets are used for heavy-duty and industrial applications.
10. Steel Split Sprocket
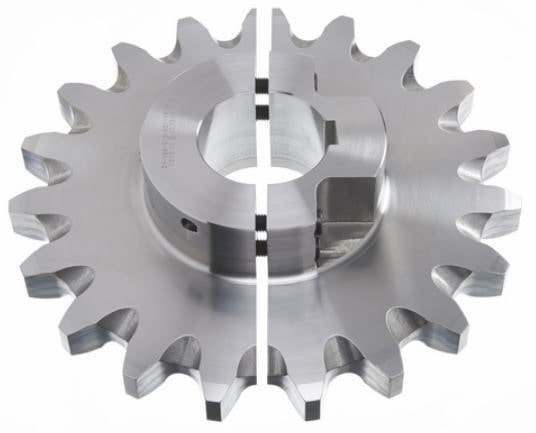
Several sprockets are required by loosening the chain, putting the sprocket, and tightening the chain again. Because, a steel-split sprocket consists of two parts that are split through the center and bolted back together, helping easy fitting into a system.
11. Idler Sprocket
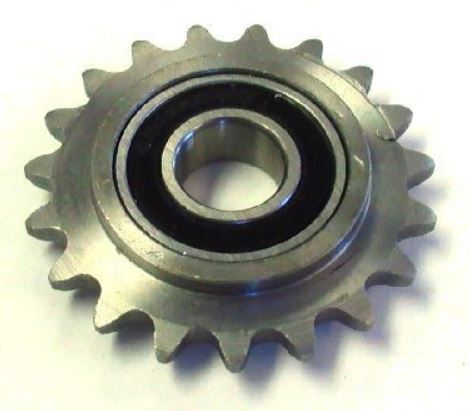
It is used where long lengths may cause chain slack, there is a non-adjustable drive shaft, or the chain is guided around an obstacle. The use of an idler sprocket stops chain whipping and uneven load distribution.
12. Bushed Sprocket
These sprockets provide support, such as anchor bolts, to assure that the flange holds to the sprocket. Heavy lifting industry systems often require bushing sprockets.
13. Multi Strand Sprocket
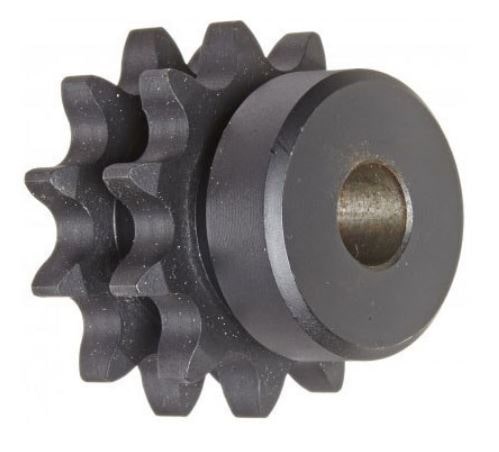
Multi-strand sprockets are used where high torque and power are required, or two or more items are being driven by a drive shaft. These are available with 40 to 160 chain pitches with plain, finished, taper-locked, or QD style hubs.
12. Quick Disconnect Sprocket
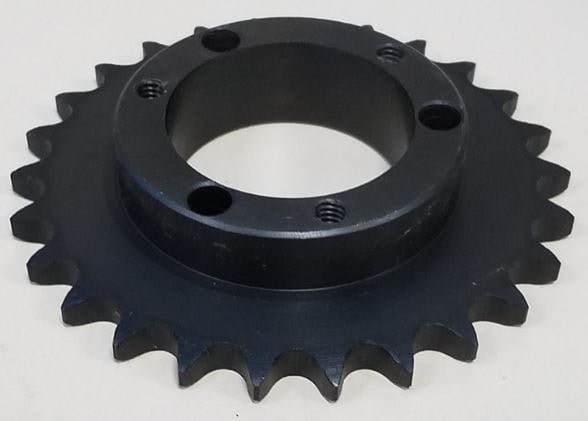
These sprockets are used in high working load and high clamp loading on shaft. QD sprockets are flanged with anchor bolts around the perimeter.
15. Taper Lock Sprocket
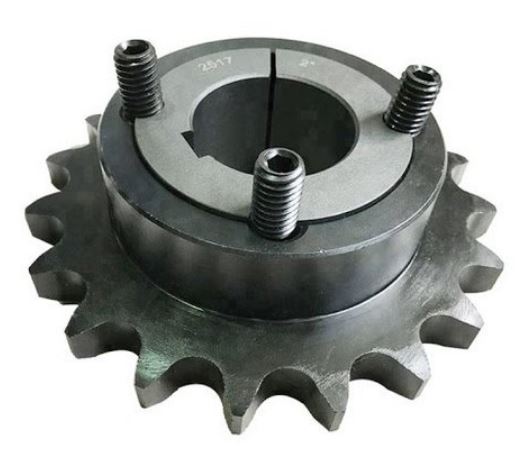
This sprocket uses a split through the taper and flange to give a clamp on the shaft. The taper-lock bushing is held in place with the set screw on the sprocket.
16. Double Plus Sprocket
The Double Plus sprocket is specifically designed with the Double Plus chain. They are used in conveyor applications where the product is moving at high speed to power the conveyor.
Applications of Sprockets
There are several types of sprocket available, each applied on different types of machinery to run on movement in various applications. Following are the common applications of sprockets:
The sprockets are used in agricultural and farming equipment applications. These are also employed in automotive equipment. It is used in chain-driven machinery, such as conveyor belts and other factory systems.
Sprockets are very useful in pulleys, shafts, and other power transmission equipment. Are also used in-vehicle systems, such as bicycles and motorcycles.
Conclusion
Almost all industries use sprockets because they do not have slip and creep issues and are even more efficient than belt drives. They are capable of working effectively at high temperatures.
Now, I hope that I have covered everything about sprockets. If you have any doubts about this article on “Types of Sprockets” you can ask in the comments. If you liked this article, please share it with your friends.
Subscribe to our newsletter to get notification when we upload the latest posts.
Download the PDF File of this article
You might like to read more:
- Types of Punches and How to Use? Explained with Picture & PDF
- Types of Nail Guns [Complete list] When and How to Use with PDF
- What is Vice? It’s Parts, Construction, Diagrams, and More
FAQ
Sprockets are classified into four types but the most commonly used sprockets are: Chain sprockets, Duplex sprockets, Industrial sprockets, Drive sprockets, Triplex sprockets, Shaft sprockets, Simplex sprockets, Single pitch and double pitch sprocket, Drum sprockets
Steel split sprockets, Idler sprocket, Bushed sprocket, Multi-strand sprocket, Quick disconnect sprocket, Taper-lock sprocket, and more.
The sprockets are used in agricultural and farming equipment applications. These are also employed in automotive equipment. It is used in chain-driven machinery, such as conveyor belts and other factory systems.
These are the most common types of sprockets used. They work only with chains designed by rollers interconnected by pins. Roller chains provide a gap that fits the teeth of the sprocket to transfer rotary motion.