In this post, you learn what is chemical machining and why it is used. Also, chemical machining working principles, processes, advantages, and applications.
Furthermore, you can also download the PDF file of this article.
What is Chemical Machining?
Chemical machining is the material removal process for producing desired shapes and dimensions. It is done by selective or overall removal of material by a controlled chemical attack with acids or alkalies.
The metal is slowly converted into metallic salt by chemical reaction and is finally removed in this form. Areas from where the material is not to be removed are protected by an etching-resistant material, known as ‘maskant or ‘resist’.
Almost all materials, from metals to ceramics, can be chemically machined. The component to be machined is first cleaned in trichloroethylene vapor or a solution of mild alkaline solution at 80 to 90 °C, followed by washing in clean water.
One of the roughest methods is to coat the component all over by spraying or dipping. This removes dust and oil. The cleaning ensures good adhesion of the coating or masking agent.
After cleaning, the component is dried and coated with the maskant material, which may be cut and peeled, photoresist, or screen-print type. Finally, the metal is removed by etching.
Read Also: What are the Different Types of Metals and Their Uses?
Construction of CMP

#1 Chemical Reagent (Etchant)
The chemical, sometimes referred to as the etchant, is the essential part of chemical machining. It is responsible for removing material from the workpiece.
It dissolves as a result of a chemical response it has with the specific area of the workpiece material. The choice of etchants depends on the composition of the workpiece.
#2 Cooling & Heating Coil
This part is essential to the chemical machining setup because it keeps the chemical or etchant at the ideal temperature during the machining operation.
#3 Stirrer
The stirrer is an essential component of the setup because it makes it easier to thoroughly mix the chemical or etchant, which guarantees consistency and effectiveness in the chemical machining procedure.
#4 Mask
Maskant is a type of masking substance that is used to shield the surface of a workpiece from chemical etching.
Chemical Machining Working Principle
The chemical machining working principle is chemical etching. The part of the workpiece whose material is to be removed is exposed to a chemical known as enchant. The enchantment removes the metal from the chemical attack. The method of making contact with material by the enchant is masking.
Read Also: Different Types of Power Hammers Used in Forging
Working of CMP
The following is an explanation of how chemical machining operates:
Cleaning
The workpiece is thoroughly cleaned in this first phase with a solvent to get rid of any dust and oil impurities. This cleaning is required to ensure adequate masking, as dust and oil pollutants might block the masking process.
Mashing
Masking is the process of adding a maskant or cover to the cleaned surface of a workpiece. In the next steps, this maskant does not react with the chemical or etchant.
It prevents the covered area of the workpiece’s surface from dissolving when the chemical machining process is underway.
Scribing
In this step, the areas of the workpiece surface that are going to be machined are specifically cleaned of the maskant. This is done before the workpiece is submerged in the etchant or chemical.
Etching
In this step, the workpiece is submerged in the etchant or chemical. When the maskant is not present on the exposed workpiece surface, the chemical reacts with it, dissolving that particular area of the workpiece.
De-Masking
As a result of the etching process, any remaining maskant is removed, revealing the final machined piece.
Chemical Machining Process
The process can be applied to different types of operations such as milling, blanking, and engraving. The different chemical machining processes can be classified as:
- Chemical milling
- Chemical blanking
- Photochemical machining
- Chemical engraving
- Chemical polishing
Chemical machining for some special purposes can also be achieved by using a jet of reactive gas, e.g., chlorine on the machining zone. This is known as Gaseous Chemical Machining or Hot Chlorine Machining and can be used for deburring of metal parts.
Chemical Milling
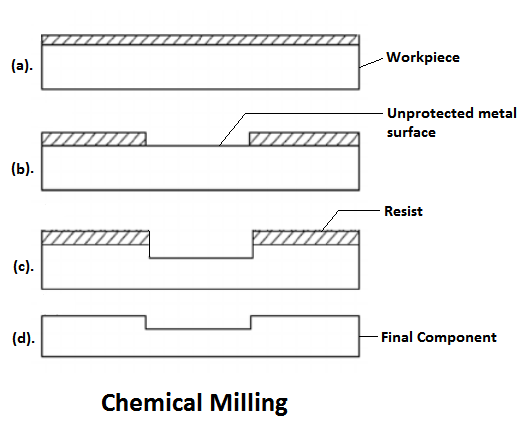
Chemical milling is sometimes called chem milling, contour machining or etching. It is used to produce shapes by selective or overall removal of metal parts from relatively large surface areas.
The main purpose is to achieve shallow but complex profiles and reduction in weight by removing unwanted material from the surface as in the skin of an aircraft. The components are cleaned and degreased by immersion in trichloroethylene vapor. Or some alternative chemical cleaner followed by washing in clean water.
Read Also: Types of Screws & Their Uses [Pictures & Names]
Chemical Blanking
Chemical blanking, chem-blanking, photo forming, photofabrication, or photo etching is a variation of chemical milling.
In this process, the material is completely removed from several areas by chemical action. The process is used mainly on their sheets and foils. Almost any metal can be worked by this process. However, it is not recommended for materials thinner than 2 mm.
Photochemical Machining
PCM is an innovative technology for producing stress-free and crack-free components, making it perfect for machining minute details on a workpiece.
This process is an advanced chemical machining method that combines Chemical Machining (CHM) for material removal with a photo-resistive mask for precise design.
Chemical Engraving
Chemical engraving is used to precisely replicate designs, including brand names, serial numbers, or titles, on a workpiece.
Chemical Polishing
it is carried out with a lighter, diluted chemical reagent to produce fine finishing or deburring of a workpiece.
Read Also: What are Different Types of Chips In Metal Cutting?
Application of Chemical Machining
- CHM has been applied in a number of usages where the depth of metal removal is crucial to a few microns, and the tolerances are close.
- The surface finish obtained in the process is in the range of 0.5 to 2 microns.
- Besides, it removes metal from a portion of the entire surface of formed or irregularly shaped parts such as forgings, castings, extrusions or formed wrought stock.
- One of the major applications of chemical machining is in the manufacture of burr-free, intricate stampings.
Advantages of Chemical Machining
The following are the advantages of chemical machining:
- It is capable of producing highly accurate metal pieces.
- It can machine a wide range of sizes and forms.
- All sides of the workpiece are machined simultaneously.
- This procedure is possible for less experienced workers.
- It may attain a high level of surface polish.
- It has a high degree of machining precision.
Disadvantages of Chemical Machining
The following are the disadvantages of chemical machining:
- In this process, the chemical solution used is hazardous to people’s health.
- The procedure moves at a slow speed.
- Because the chemical is toxic, it is essential to take the necessary safety precautions.
- When doing this process, ventilation, and protective gear are crucial.
- Despite the possible health hazards, the technique has special benefits for precision production.
Closing It Up
That’s it. Thanks for reading if you have any questions about “chemical machining” ask in the comments. If you found this post helpful, then please share it with your friends.
Want free PDFs direct to your inbox? Then subscribe to our newsletter.
Download PDF of this article:
Read more articles on the machining process:
FAQs
Chemical machining is a reductive manufacturing technique that uses chemicals to remove material from a workpiece in specific areas, allowing for the creation of complex patterns and structures.
The chemical machining process is typically carried out in five steps: cleaning, masking, scribing, etching, and demasking.
Chemical machining is used to achieve fine finishes, deburr, contour shape, and produce precision metal parts.
Chemical blanking uses a suitable etching solution to produce machined features on thin plates and foils, which were generally produced by mechanical blanking presses.
Hello, thanks a bunch for these incredible insights. Short, sweet and detailed at the same time. Kindly send me this PDF.
You’re welcome. The PDF file has been sent to your inbox.