In this post, you learn what is Electrochemical Machining? Its Working principle, Advantages, Disadvantages and more.
Electrochemical Machining
Electrochemical machining is the reverse of electroplating. An electrolyte works as a current carrier, and the high rate of electrolyte flow in the tool-workpiece gap washes metal ions from the workpiece (anode) before they have a chance to plate onto the tool (cathode).
Modification of this process are used for turning, facing, slotting, tremping, and profiling operations in which electrode becomes the cutting tools. The shaped tool is made out of brass, copper, bronze, or stainless steel.
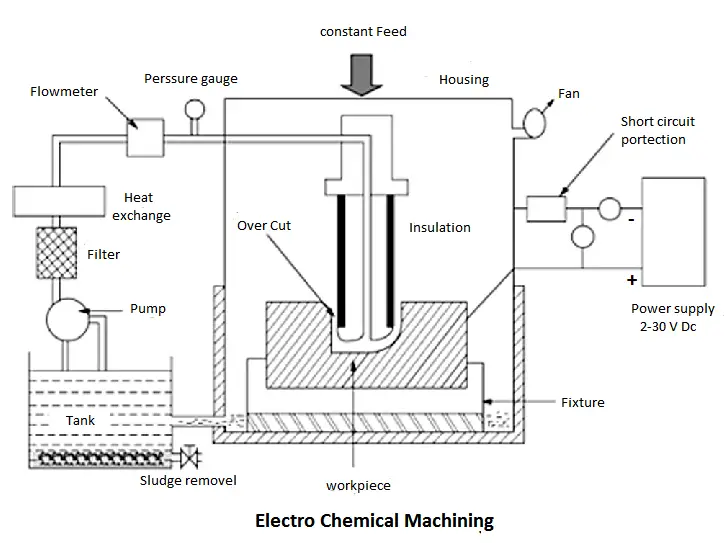
The electrolyte is an extremely conductive inorganic salt solution such as sodium chloride mixed in water or sodium nitrate. It is pumped at a high rate through the passages in the tool.
Read also: Electron-Beam Machining (EBM): Working Principle, Advantage, Limitation and Design
A DC power supply in the range of 5-25 volt. Maintains current densities, which for most of the applications are 1.5-8 A/mm2 of the active machined surface.
Machines having current capacities as high as 40,000 A and has low has 5 AR available.
The penetration rate of the tool is proportional to the current density since the metal removal rate (MRR) is only a function of the ion exchange rate. It is not affected by the strength, hardness, or toughness of the workpiece.
Read Also: What is Chemical Machining? Working Principle, Application & Advantages
Components of Electrochemical Machining
The components of an electrochemical machining are as follows:
- Power supply
- Tank
- Electrolyte
- Tool
- Mechanical system
- Pressure relief valve
- Pressure gauge
- Pump
- Filter and centrifuge
- Slug container
#1 Power Supply
The source of energy for the electrochemical machining setup is the power supply. Depending on the need, the power source is typically a DC battery with a potential difference ranging from 3 to 30V.
#2 Tank
The electrolyte, tool, and workpiece are all housed in the tank. Here is where all of the reactions happen.
#3 Electrolyte
The workpiece and tool are held in an electrolyte during the machining process, which is a salt solution. Between the workpiece and the tool, it serves as a current-carrying medium.
Along with serving as a coolant by preventing overheating of the tool and the workpiece, it also aids in the removal of waste materials from internal gaps. Sodium chloride (NaCl), sodium nitrate (NaNO3), hydrochloric acid (HCl), and other electrolytes are utilized in ECM.
#4 Tool
The tool, an electrode, is also in the desired shape for cutting the workpiece. Every ECM tool should have precise dimensions.
#5 Mechanical System
The mechanical system is one of the key components of ECM. It is employed to advance a tool at a constant velocity that is perpendicular to the workpiece.
#6 Pressure Relief Valve
The pressure relief valve opens and returns the electrolyte to the tank if the electrolyte flow pressure exceeds a predetermined threshold.
#7 Pressure Gauge
The pressure of electrolytes supplied to the tool is measured using a pressure gauge.
#8 Pump
In electrochemical machining, A and B pumps are utilized. Electrolytes are drawn from the reservoir tank using pump A. The electrolyte is supplied to the reservoir tank by pump B.
#9 Filter and Centrifuge
Before the electrolyte enters the reservoir tank, it is filtered using a filter. It avoids the buildup of extra electrolytes. A centrifuge’s job is to separate the electrolyte from the slug.
#10 Slug Container
The slug that has been separated from the electrolyte is kept in a slug container. There are many different experimental uses for this slug.
Read Also: 23 Types of Metals and Their Properties & Uses [Explained]
Working Principle of Electrochemical Machining
In essence, the electrochemical machining process relies on Faraday’s law of electrolysis. In Faraday’s law of electrolysis, when two electrodes are placed in an electrolyte, anode (+ve) and cathode (-ve), the mass of metal that is deposited on the cathode corresponding to the anode is directly proportional to the potential difference between them.
Working of Electrochemical Machining
The process of electrochemical machining begins with the tool being moved closer to the workpiece. Workpiece and tool are immersed in an electrolyte with a very small gap between them. When the potential difference (DC) is applied, the tool behaves as a cathode and the workpiece as an anode.
The process of removing metal from the workpiece begins once the electrolysis condition is met. According to the tool’s shape, metal removal occurs. The flow of electrolytes causes the material to be removed from the workpiece and settle down as a slug.
After that, the electrolyte goes through filtration. During this process, the electrolyte is centrifuged to remove the slugs. After that, any additional impurities are removed through a filter. In the event of a rise in electrolyte pressure, the pressure valve directly diverts the flow to the tank.
Read Also: Understand The Different Types of Welding Positions [Pictures & PDF]
Design Consideration of Electrochemical Machining
- It is not suited for producing sharp square corners or flat bottoms.
- Controlling the flow of electrolyte is difficult so irregular cavities may not be produced to desired shapes with acceptable dimensional accuracy.
Advantages of Electrochemical Machining
- Machining of hard and brittle material is possible with excellent quality of surface finish and dimensional accuracy.
- Complex shapes can also be easily machined.
- There is almost negligible tool wear, so the cost of tool-making is only a one-time investment for mass production.
- There is no application of force, no direct contact between tool and work, and no application of heat.
- Mechanical and thermal residual stresses are absent in the workpiece.
- Very close tolerance can be obtained.
Disadvantages of Electrochemical Machining
- All non-conducting materials cannot be machined.
- Tools material and workpiece material should be chemically stable with the electrolyte solution.
- Designing and marking of the tool is difficult, but its life is long, so recommended only for mass production.
- The accurate feed rate of tools is required.
Application of Electrochemical Machining
- This process is used to machine complex cavities in high-strength materials, particularly in the aerospace industry, for mass production of turbine blades, jet-engine parts, and nozzles.
- It is also used to machine forging-die cavities (die sinking) and to produce small holes.
- It can be used as a deburring process.
- There is no tool wear, and it can be used to machine hard (brittle and heat-resistant) materials.
- Internal finishing of surgical needles and also for their sharpening.
- Drilling of small and dipper holes with very good quality internal surface finish.
- Used for making inclined and blind holes and finishing conventionally machined surfaces.
That’s it, Thanks for reading if you have any questions about “Electrochemical machining” ask in the comments section. If you like this article share with your friends.
Want free PDFs direct to your inbox? Then subscribe to our newsletter.
Read Also: