In this article, you’ll learn what is a metal chip? How metal chips are produced? Their Conditions, Advantages? and what are different types of chips. You can download the PDF file of this article at the end.
What is Metal Chip?
The machining of metals highly depends on the types of chips it produces. When compared to the different production of metal, the metal is removed in various industries while doing the machining process is known as metal chips.
You may wonder what is actually machining process stands for? In simple words, the machining process is a cutting process in which the workpiece is cut by means of a tool to make its desired shape and size.
In this process, the excess metal of the workpiece is removed in the form of chips. The types of chips formed in the machining process depend on some basic factors. In machining, the formation of chips is a necessary index because it indicates directly or indirectly the:
- Nature and behavior of the material under the machining process.
- Nature and degree of interaction in chip interfaces.
- The amount of energy required to extract the material.
Read also: List of 13 Mechanical Properties of materials
What Are Some Conditions To Produce Chips?
- Nature of material or workpiece
- Material of cutting tool or Nature of tool
- Level of decreasing velocity and feed rate
- Machining environments like temperature
- Cutting fluid
- Dimension of tool
- Friction between tool and work metal
Types of Chips
Types of chips in metal cutting are as follows:
- Continuous chips
- Discontinuous or segmented chips
- Continuous chips with built-up edges
1. Continuous Chips
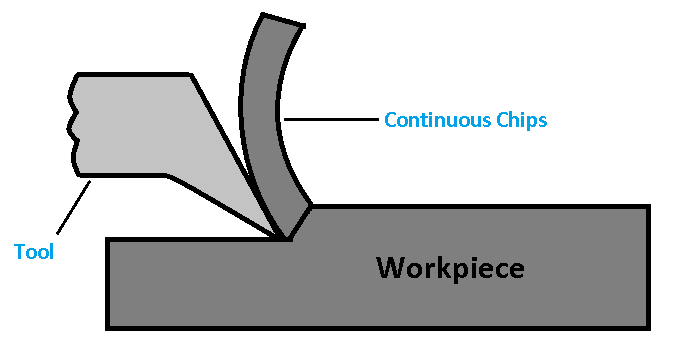
In the machining process, continuous chips are formed during the machining of ductile material with high speed and minimum friction between the tool and material. Due to continuous plastic deformation by applying the tool, this type of chip is produced.
Mild steel and copper is a ductile materials. The thickness of the chip is equal to entire the length. It commonly provides a good surface finish. The main drawback of this type of chip is difficult to handle and dispose of.
What are the situations of producing continuous chips?
- Ductile material like mild steel, copper, or aluminum is used.
- The cutting speed of the machining process is high.
- The size of the chips is small.
- Minimum friction between the chip and tool face.
- The rake angle of the tool is maybe high.
- Using the efficient type of cutting lubricant.
- Low coefficient friction of the tool.
Advantages of Continuous Chips
Following are the advantages of continuous chips:
- By using the ductile material, it provides a better surface finish.
- It takes low power consumption.
- It provides a long lifespan of the tool due to less wear and tear.
- Due to minimizing friction between chip and tool face, it requires less heat generation.
Read also: What are different operations performed on lathe machines?
2. Discontinuous or Segmented Chips
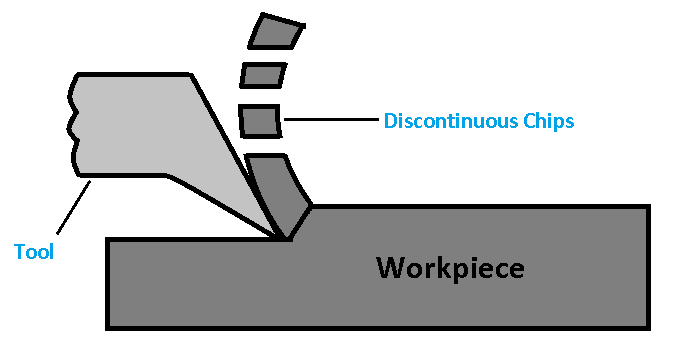
In the machining process, the chips formed in a small segment or with breakage during cutting are known as discontinuous or segmented chips. Discontinuous chips are formed by using brittle or hard material in machining.
Brass, bronze, and cast iron are brittle materials. Due to slow cutting speed and small rack angle, this type of chip is produced. These chips are made when the friction between the tool and the workpiece is high.
Discontinuous chips in ductile materials provide a poor surface finish. The discontinuous chips are easily handled and disposed of.
How do discontinuous chips form during machining?
- Due to the low feed rate in the machining process.
- The cutting speed of the machining is low.
- High friction between chip and tool face.
- Due to the large depth of cut.
- The rake angle of the tool is small.
Advantages of Discontinuous Chips
- These types of chips provide a good surface finish in brittle materials.
- It gives a long lifespan to the tool.
- It reduces the consumption of power.
Disadvantages of Discontinuous Chips
- By using ductile material, it gives a poor surface finish.
- Excessive wear and tear of equipment occur.
Read Also: Metal Casting Process: Types, Advantages, Uses [Explained]
3. Continuous Chips With Built-Up Edges
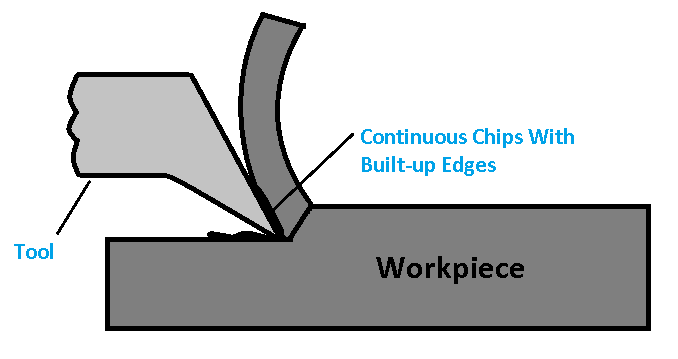
In the machining process of ductile material, continuous chips are made with built-up edges when the temperature and pressure in the cutting and friction of the chip and tool face are high.
It is almost similar to the continuous chips but it is rough due to the built-up edge. This function may cause the material to stick or weld to the edge of the tool.
You may wonder how it produces?
It is created, when the chip flows upward and friction between the interface of the chip and tool is high. The heat generated at the nose of the tool is very high, due to the high friction between the chip and the tool.
Hence, compressed metal fit to the tool nose is welded therefore it is known as built-up edges. If the chip flows through this built-up edge, it breaks and is sent away from the chip and is termed a built-up edge chip. The rest of the built-up edge adheres to the surface of the workpiece and does it thicker.
Why do Continuous Chips With BUE occur when you machine?
- By using the ductile material while machining.
- Due to the smaller rake angle of the tool.
- The cutting speed of the tool is slow.
- Lack of coolant may cause increases in friction between chip-tool faces.
- The thickness of the chip is high.
- Due to the high temperature between the workpiece and tool.
- High rate of feed of the tool.
Advantages of Continuous Chips with BUE
- Due to the high friction, while machining, it protects the tool from damage.
- Also, it increases the tool lifespan.
Disadvantages of Continuous Chips with BUE
- The drawback of this type of chip is that it provides a rough surface finish.
- It may cause a reduction in rake angle and cutting forces.
Comparison Between Continuous, Discontinuous, and Continuous chips with BUE
SI. No. | Conditions | Continuous Chips | Discontinuous Chips | Continuous chips with BUE |
1. | Material used | Ductile | Brittle or Hard | Ductile |
2. | Cutting speed | High/Medium | Low | Medium |
3. | Friction between chip and tool | Low | High | High |
4. | Rake angle | Large | Small | Small/Medium |
5. | Depth of cut | Small | Large | Medium |
FAQ
Three types of chips are produced in the metal cutting process. Continuous chip formation creates an excellent surface finish that has a positive effect on the workpiece.
Due to the high friction when machining, it prevents damage to the tool. Furthermore, it prolongs the lifetime of the equipment.
Conclusion
As you know now, the chips are made when you machine the brittle materials. These chips are formed when the friction between the tool and the workpiece is high and the cutting speed is small with a short rake angle.
That’s it. We have discussed all the types of chips that are produced during the machining. But if you still have any questions about this article you can ask in the comment we will respond to you.
If you like this article then please share it with your friends. And also you can download the free PDF file of this article by clicking below.
Lastly, subscribe to the newsletter to get notifications of our new posts. It’s Free.
You might like to explore more in our blog:
- What are the Defects of Welding? With their Causes and Remedies [PDF]
- How does Plasma Arc Welding work? Read In Detail with [PDF]
- How you can differentiate the TIG and MIG welding?
External links: