In this post, you learn about electrochemical grinding. Its working principle, advantages, and more.
What is Electrochemical Grinding?
Electrolyte grinding is a modification of both grinding and electrochemical machining. In this process, machining is affected both by the grinding action and by the electrochemical process. Hence, in the true sense, it may be called ‘mechanically assisted electrochemical machining.
By combining the concepts of electrochemical machining and conventional grinding, ECG delivers extraordinary accuracy and productivity in material removal.
Electrochemical machining uses a cutting tool, but ECG uses a grinding wheel, making it particularly effective when grinding workpieces of high hardness.
In general, ECG is the best method for grinding materials harder than 65 HRC. Through electrochemical processes, the metal surface in this process is transformed into its corresponding oxide.
The revolving grinding wheel effectively eliminates the oxide layer, giving the workpiece its precise shaping and finishing. The reverse electroplating approach offers industries an easy solution for complicated machining requirements, producing superior surfaces.
Read Also: What is a Single Point Cutting Tool?
Parts of Electrochemical Grinding
The following are the parts of electrochemical grinding:
#1 DC Power Supply
An electrochemical grinding arrangement is powered by a DC power supply that has a high current and low voltage. Maintaining a low voltage is crucial for two reasons: it prevents overheating and ensures safety while operating.
#2 Work Table and Fixture
Securing the workpiece in place and having a strong foundation are essential for efficient machining. Fixtures are used to securely fasten the workpiece in place, and the worktable offers the required rigidity and support.
#3 Electrolyte Tank
During the electrochemical grinding process, an electrolyte tank serves as a reservoir to store the conducting solution that is used in the electrochemical process.
#4 Pump
An electrically operated pump transports the electrolyte from the tank to the nozzle, guaranteeing a constant flow throughout the procedure.
#5 Filter
To ensure the use of a pure electrolyte, the electrolyte is filtered before it reaches the machining area to get rid of minute contaminants.
#6 Pressure Gauge and Flow Meter
The pressure and flow of the electrolyte are monitored by safety devices like flow meters and pressure gauges.
#7 Nozzle
The nozzle has a decreasing cross-section size, is essential for precisely directing the electrolyte. When the nozzle is positioned correctly, the electrolyte comes into contact with the grinding wheel and the workpiece.
#8 Sleeve
To facilitate the machining process, a sleeve is employed to efficiently transport electrical energy to the grinding wheel.
#9 Grinding Wheel
The revolving grinding wheel, which is made of insulators like diamond and aluminum oxide, increases the electrolyte flow.
Since only 5-10% of the material is removed by the grinding wheel, most is removed by the electrolyte, resulting in minimal wear.
#10 Collecting Tank
The electrolyte is collected in a specified tank after use, depending on regulations and environmental factors, for appropriate disposal or possible reuse.
Working of Electrochemical Grinding
In Electrochemical grinding, the metal-bonded grinding wheel is filled with a non-conductive abrasive. The grinding wheel acts as a cathode and the workpiece acts as an anode.
The electrolyte, which is usually sodium nitrate, sodium chloride, and potassium nitrite, with a concentration of 0.150 to 0.300 kg/liter of water.
It is passed through a nozzle in the machining zone to complete the electrical connection between the anode and the cathode.
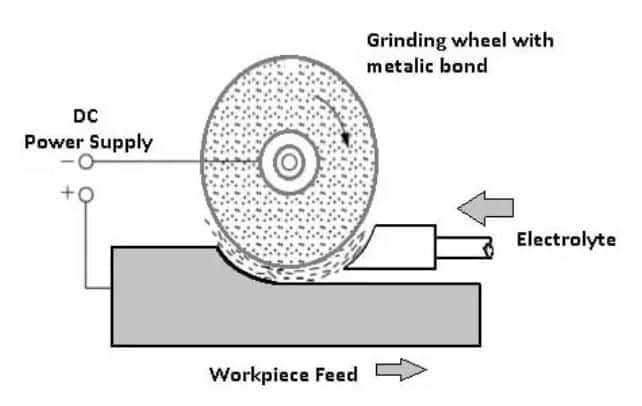
The work and wheel do not make contact with each other. Both are kept apart by the insulating abrasive particles which protrude from the face of the grinding wheel. A constant gap of 0.025 mm is maintained into which a stream of electrolyte is directed.
The electrolyte is carried past the work surface at high speed by the rotary action of the grinding wheel. With the rotation of the grinding wheel, metal is removed from the workpiece by the simultaneous electrolytic and abrasive action.
Abrasive grains on the surface of the wheel serve to act as a paddle that picks up the electrolyte and causes pressure to build at the work area.
Read also: What is the Working Principle of Laser Beam Machining (LBM)?
Wheel and Work Conditions in Electrochemical Grinding
The electrolyte is captured in small cavities of semiconductive oxide between projecting nonconductive abrasives forming electrolytic cells. When these cells come in contact with the work the current flows from the wheel to the work and this leads to the electrochemical decomposition of the work. The short-circuiting between the wheel and work is prevented due to point contact made by fine abrasive particles.
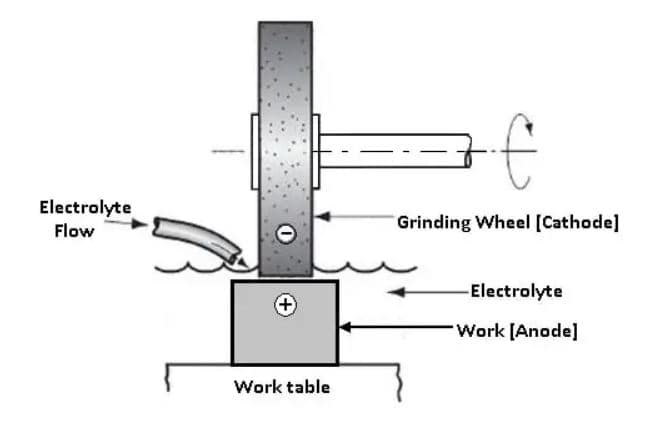
These protruding abrasive particles also remove the unactive layers formed on the work by abrasion to make the surface more receptive. It can be seen that the process is similar to conventional grinding. In that, an abrasive grinding wheel is used and the work is fed against the rotating wheel. 10% of the work metal is removed by abrasive cutting, and 90% by electrolytic action.
The grinding wheels used are of conventional shape and structure. Metal bond, diamond grit wheels are used for grinding tungsten carbide tips. Carbon bond wheels are used upon hard alloy steels such as stainless steel.
Wheel wear is negligible because the greatest part of the cutting action is electrolytic, and little dressing is necessary. The wheel, with its spindle and bearings, must be insulated from the machine frame and supplied with current through slip rings.
The machine is similar in design to a surface grinder or tool. The cutter grinder and the equipment include a tank, filter, and pump for the supply of electrolytes and a power unit for delivering a heavy DC. The current applied is in the range of 50 to 3000 A at 4 to 10 V (250 A/cm).
Read also: What are the Advantages of Ultrasonic Machining (USM)?
Accuracy
- Because there is very little abrasive action, Electrochemical grinding does not leave fine scratches which may impair the finish and leave stress raisers.
- Tolerances of about +0.02 are held on rather complex grinding operations. For closer tolerances, the proportion of material removed by abrasive should be increased.
- The surface finish is held in the range of 0.2 to 0.4 microns on carbide and 0.4 to 0.8 microns on steel.
- Sharp corners are difficult to obtain and the smallest radius of 0.2 mm cannot be avoided unless a final pass without electrolytic action is used.
Applications of Electrochemical Grinding
Any conductive material may be ground by the electrolytic process. But its most useful application is concerned with hardened steel, cemented carbides, and similar materials.
This is mainly applied to resharpening and reconditioning of carbide tools and other materials that are difficult to grind.
The grinding pressure is low. It is possible to grind and cut thin sections and thin-wall tubing of difficult materials without distortion or burr.
Advantages of Electrochemical Grinding
- Since there is no direct touch between the tool and the workpiece, the process ensures minimal dimensional errors and produces amazing precision.
- ECG makes it possible to achieve tight tolerances, which facilitates the creation of complex and highly detailed workpieces.
- Its electrochemical nature ensures that no scratches or surface imperfections are left on the workpiece.
- ECG produces far less heat energy during operation than traditional grinding techniques, protecting the workpiece from thermal damage.
- Because there is no mechanical contact, there is less chance that internal stress may develop inside the workpiece, protecting its structural integrity.
- Sharp and clean edges are produced by electrochemical grinding, guaranteeing excellent and precisely defined workpiece features.
Disadvantages of Electrochemical Grinding
- During the process, material is removed relatively slowly, typically around 15mm/s, affecting productivity for high-volume production.
- The grinding wheel and pump must both be driven, which increases energy consumption and makes the process demanding.
- The initial setup costs of electrochemical grinding are rather costly due to the significant investment required in specialized equipment.
- Due to the slower rate of metal removal, large-scale manufacturing operations may experience a limitation in the overall output rate.
- Waste electrolytes require proper disposal, making the process less environmentally friendly.
Conclusion
That’s it. Thanks for reading if you have any questions about “Electrochemical Grinding” ask in the comments. If you found this helpful share it with your friends.
Please share this article with your friends if you find it interesting.
Want free PDFs direct to your inbox? Then subscribe to our newsletter.
Read more on our blog:
- Function of the Plasma Arc Machining (PAM) Explained
- What are the components of chemical machining?
- What is the working principle of iron beam machining?
FAQs
Electrochemical grinding uses an electrolyte and a moving grinding wheel to remove material from a conductive workpiece using controlled electrochemical processes.
Electrochemical grinding is used to polish hard surfaces, create sharp objects, grind fragile items, and grind turbine blades and honeycomb structures in aerospace.
To perform ECG, you will need a DC power supply, a grinding wheel made of abrasive, copper, and resin binder, an electrolyte fluid (typically sodium nitrate), and a workpiece made of conductive and reactive materials like steel, stainless steel, chrome-nickel alloys, or high-temperature materials.
Electrochemical oxidation is removed from the workpiece’s surface by the grinding wheel’s protruding abrasive grit particles.
What are similarities between EDM and ECM
The similarity is being that both EDM and ECM are non-conventional types of machining processes. However, a major difference is that EDM relies on spark erosion to remove the material, whereas ECM uses electrolysis to locally dissolve the metal.
Inter electrode gap in ECG is controlled by
It’s a controlling the size of diamond particle in the wheel