In this article, you’ll learn what is a crankshaft? how does it work? Its types, parts, functions, and more are explained in detail with diagrams.
Also, you can download the PDF file of this article at the end of it.
What is Crankshaft?
A crankshaft is an essential part of the power transmission system. In which, the reciprocating movement of the piston is converted into a rotating movement by using the connecting rod.
A crankshaft consists of crankpins, crank webs (crank arms or cheeks), balancing weights, and main journals. The large end of the connecting rod is attached to the crankpin of the crankshaft.
During one stroke, the center-to-center distance between the crankpin and the crankshaft is half the piston displacement. Thus, one complete revolution of the crankshaft makes two strokes of the piston.
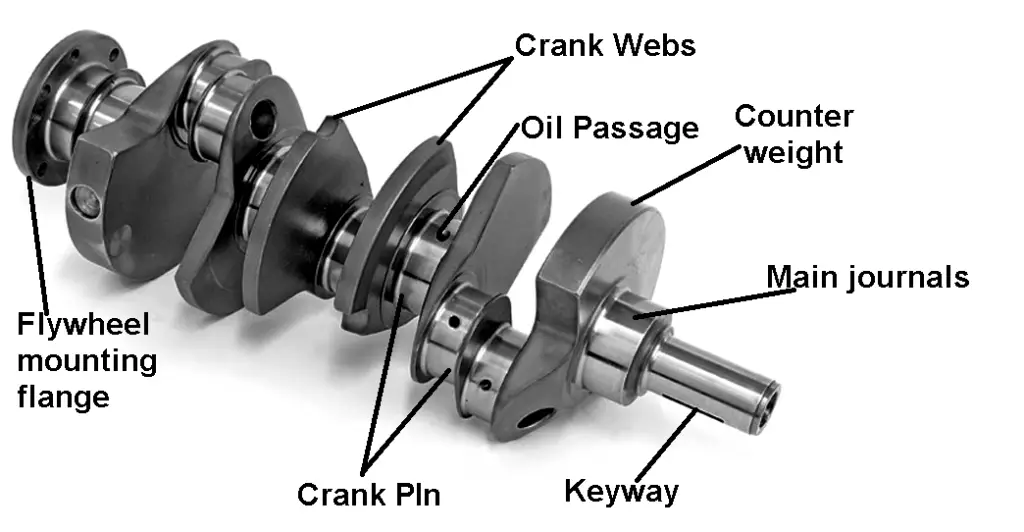
You might to read this: What is Fuel Injection System? And Types of Fuel Injection
Parts of Crankshaft
The following are the main parts of a crankshaft with its diagram:
- Crankpin
- Main journals
- Crank web
- Counterweights
- Thrust washers
- Oil passage and oil seals
- Flywheel mounting flange
#1 Crank Pin
The crankpin is a mechanical part of an engine. It allows the connecting rod to be attached to the crankshaft very firmly.
The surface of the crankpin is cylindrical to give the rotative force to the large end of the connecting rod. These are also known as connecting rod journals.
#2 Main Journals
Journals have been attached to the engine block. These bearings hold the crankshaft and allow it to rotate inside the engine block.
This bearing is such as a plain bearing or journal bearing. The main bearings vary from engine to engine, often according to the forces given by the engine.
#3 Crank Web
The Crank web is the most essential part of the crankshaft. The crank web connects the crankshaft to the main bearing journals.
#4 Counterweights
The counterweights are a type of weight that applies the opposite force. This provides balance and stability to the crankshaft. These are mounted on the crank web.
The reason for installing counterweights in the crankshaft is they can eliminate the reaction caused by rotation. It is very helpful for achieving a higher RPM and makes the engine run easily.
#5 Thrust Washers
At some points, two or more thrust washers are provided to stop the crankshaft from moving lengthways. These thrust washers assemble among the machined surfaces in the web and the crankshaft saddle.
With the help of thrust washers, they can easily maintain the gap and help to reduce the lateral movement of the crankshaft. In many engines, these are made as part of the main bearings. Usually, older types use separate washers.
#6 Oil Passage and Oil Seals
Crankshaft oil passage passes oil from main bearing journals to the big end journals. Normally the hole is drilled on the crank web. When the crankpin is upward, the combustion force pushes the connecting rod downward, and oil can enter between the journal and the bearing.
The crankshaft has some extent beyond the crankcase on both ends. This causes oil to leak from these ends. So, to prevent oil from these openings, oil seals are provided. There are two main oil seals connected at the front end and rear end.
- Front-End Oil Seals: They are similar to rear-end oil seals. However, its failure is less destructive and more easily accessible. The front oil seal will be set behind the pulley and timing gear.
- Rear End Oil Seals: These are placed within the main journals and flywheels. It is pushed into a hole between the engine block and the oil pan. The oil seal has a shaped lip that is kept tightly into the crankshaft by a spring called a garter spring.
#7 Flywheel Mounting Flange
In most cases, the crankshaft attaches to the flywheel through the flanges. The diameter of the crankshaft wheel end is larger than the other end. This gives a flange face to mount the flywheel.
Check out this: 15 Essential Parts of Car Wheel Assembly & Its Function
Construction of Crankshaft
The crankshaft consists of main bearings, which are also called main journals. The crankshaft is supported by the main bearing on the main journals. A balanced load is provided in the opposite direction of the crankarm for equilibrium.
A crankshaft is usually manufactured of alloy steel by casting or forging process. It is machined and grounded to give suitable journals for the connecting rod and main bearing.
It must be strong enough to take the thrust of the pistons during the power strokes without excessive distortion. Also, it should be carefully balanced to eliminate undue vibration resulting from the weight of the offset cranks.
The crankshaft has drilled oil passages through which oil can flow from the main bearing to the connecting rod bearing.
Function of Crankshaft
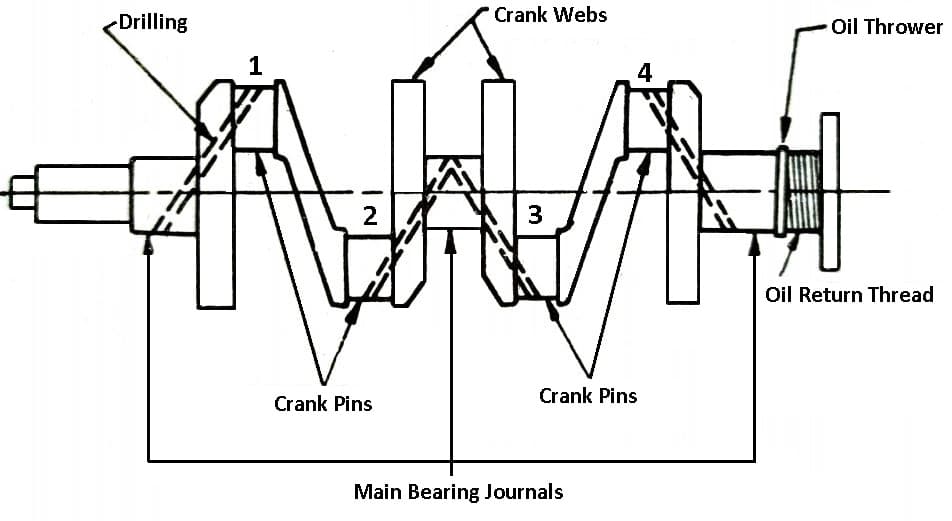
The front end of the crankshaft carries a gear or sprocket, vibration damper, and fan belt pulley. A gear or sprocket operates the camshaft, and the vibration damper is provided to control torsional vibration.
The fan belt pulley drives the engine fan, water pump, and generator with a V-belt. Rear-end of the crankshaft carries the flywheel. The inertia of the flywheel tends to keep the crankshaft turning at a constant speed.
The number of main bearings varies with the design of the engine and cylinders. The more main bearings, the less the possibility of vibration and distortion of the crankshaft of a given size.
The bearing shall be sufficient to support the shaft and give one of the greatest stiffness between each crankpin. A compromise is to have 3 main bearings on a 4-cylinder engine and 4 on a 6-cylinder engine.
To reduce vibration in the engine, the crankshaft and flywheel are balanced separately. They are often tested for balance when mounted together. Balancing is necessary to prevent damaging the engine, especially the bearings.
Read Also: What is Single Cylinder Engine? Its Parts, Working [Petrol & Diesel]
Types of Crankshafts
The following are the types of crankshafts:
- Fully built shaft
- Semi built shaft
- Welded shafts
- Solid single-piece shaft
- Forged crankshaft
- Cast crankshaft
- Billet crankshaft
#1 Fully Built Shaft
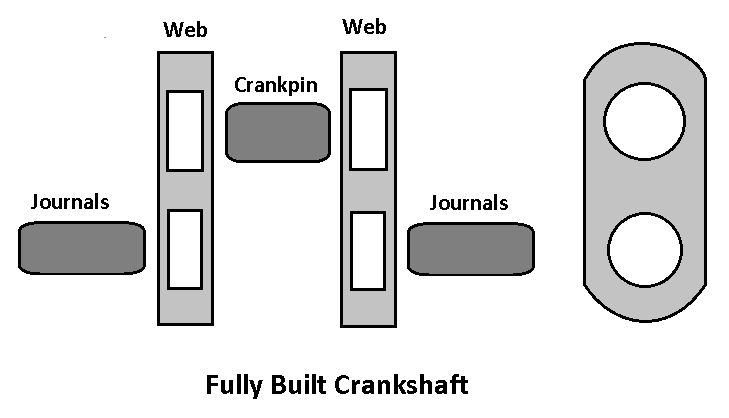
These types of crankshafts are made by assembling parts by parts together. In this, all the components are shrink-fitted after the fabrication process. This type of crankshaft is used in old engines.
It consists of a separate crank web, crankpin, and main journals. This crankpin and journals are machined and bored in the crank web. They are slightly smaller in diameter.
The crank webs were heated and fit into the crank pins and journal holes (which expanded in size due to heat). As the crank web cools, the diameter of the borehole will try to shrink back to its original size.
#2 Semi-Built Shaft
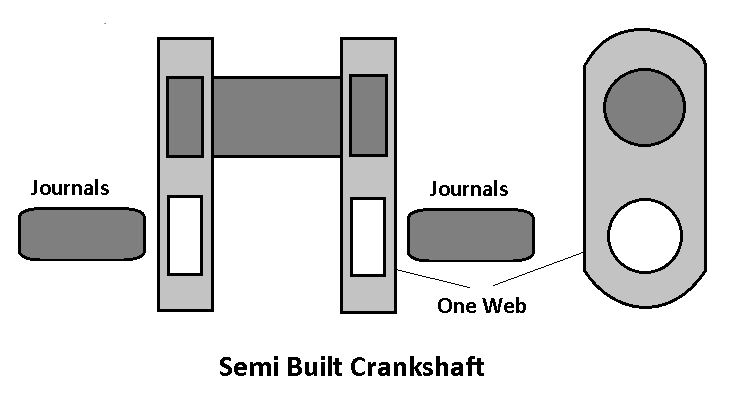
These types of crankshafts are not made by assembling various parts compared to a fully built shaft. Crank webs are completely forged and are shrink-fitted to the general bearings.
The crankpins are further machined to provide a smooth surface finish. The benefit of using this shrink-fitting method is to make two webs and crankpins with a single forging. The crank webs are reduced in thickness. A hole is bored through the crankpin, reducing the weight without compromising its strength.
The semi-built crankshaft is lighter than the fully-built crankshaft. The crankshaft can carry high loads and can therefore withstand high shear and bending stresses. These types are also found in some high-speed engines.
#3 Welded Shaft
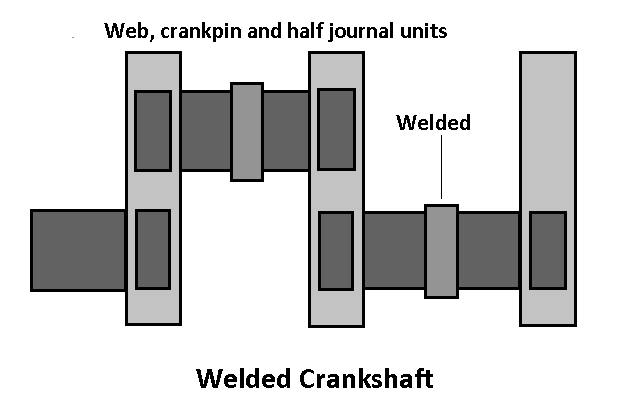
These welded shafts are manufactured by assembling the crank web, crankpin, and main journals on both sides. These are forged and then welded together by the submerged arc welding process.
After welding, the journals were stress-free and mechanized. Due to the use of continuous grain flow, the webs can be made thinner. That may lead to a smaller crankshaft.
The welded crankshaft allows considerable savings in weight. The width and thickness of the webs are reduced. Thus, providing longer bearing lengths.
#4 Solid Single Piece Shaft
These types of crankshafts are made by forging or casting processes to form single-piece shafts. They are utilized both in low-speed engines and high-speed engines.
It is built in more than one part and bolted together with bolts on integral flanges. This is designed to endure the load during firing and cyclic tension. The crankshaft is stressed due to misalignment, torsional vibration, and axial vibration of the main bearings.
#5 Forged Crankshaft
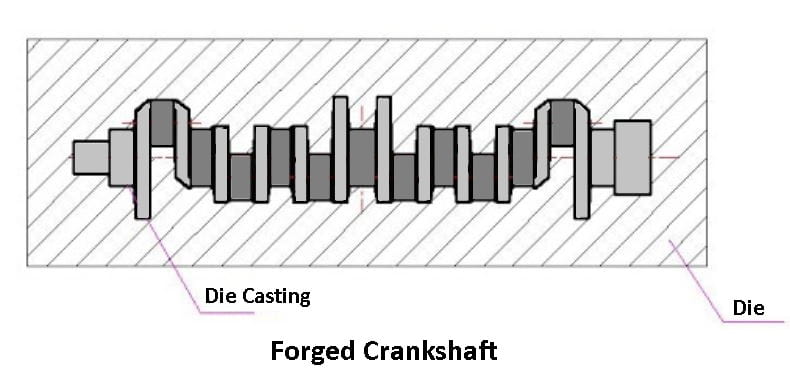
These are much stronger than cast cranks. Forged cranks are typically used in high-stress engines and some 16-valve engines. They are designed in completely different ways.
A set of dies is formed to the approximate size of the crank. These dies rest in a large hydraulic press which has a clamping force of several tons. Once the die is closed, the metal is pressed very tightly.
These types of crankshafts are stronger and more durable. Forged crankshafts react to heat treatment and thus give better dimensional stability.
#6 Cast Crankshaft
These types of crankshafts have been used for a long time. They are commonly found in various diesel and petrol engines. Generally, they are made up of malleable iron by the casting process.
They are cheap to make and work well, making them a common choice for manufacturers. Cast crankshaft withstands loads from all directions because the metal grain structure is uniform and random.
#7 Billet Crankshaft
A billet crank may be the best type of crank for your engine. Steel is commonly used to make such cranks. This includes nickel, chromium, aluminum, molybdenum, and other elements.
Billet cranks are familiar because of the shortest machining time of the crankshaft. They further need minimum balance due to the uniform design of the material.
Faults of Crankshaft
Problems on the crankshaft appear very rarely. It occurs when the engine is undergoing extreme conditions. The engine parts are robust. But they involve some basic faults:
- Worn journals
- Fatigue
#1 Worn Journals
It usually occurs when there is not enough oil pressure available. If the crankshaft makes contact with the journal-bearing surfaces, it gradually increases clearance and worsens the oil pressure.
If not taken care of it, worn journals can cause serious problems for the engine. This destroys the bearings and causes heavy damage to the engine.
#2 Fatigue
This occurs when the constant force on the crankshaft leads to breakage. This issue usually occurs on the fillet where the journal and web are involved.
A smooth surface of the fillet is necessary to avoid weak spots that cause fatigue cracks. The cracks can be inspected using Magna-fluxing on the crankshaft.
You might like this: Understand The Working of Air Brakes
Materials Used To Make Crankshaft
Steel is typically used for crankshafts because of its high strength and hardness. Compared to other materials of the same price, steel has a very high fatigue strength.
The following are some of the materials used to make crankshafts:
#1 Manganese-molybdenum steel
Manganese-molybdenum steels are used to produce crankshafts through the forging process. They are affordable crankshafts. For medium-duty petrol engines, these are utilized.
It contains 97.82% iron, 0.3% molybdenum, 0.38 carbon, and 1.5% manganese. Manganese-molybdenum steel has a Brinell hardness rating of about 250 BHN.
#2 Nickel-chromium-molybdenum Steel
These steels are used in diesel engines because of their extremely high fatigue strength. It has 2.5% nickel, 0.31% carbon, 0.65% chromium, 0.5% molybdenum, and the rest is iron. This steel has a Brinell hardness of 300 BHN.
#3 Chromium-molybdenum Steel
Medium- and heavy-duty petrol and diesel engines use this steel. It comprises 1.2% chromium, 0.4% molybdenum, 0.3% carbon, and the remaining part is iron. The Brinell hardness of chrome-molybdenum steel is approximately 280 BHN.
#4 Nodular Cast Iron
It is a perlite-filled grey cast iron with graphite nodules. Due to their high ductility, these are also called ductile cast iron. In this, around 3-4% of the substance is carbon, while 1.8-2.8% is silicon. Nodular cast iron has a Brinell hardness range of 200–300BHN.
Advantages of Crankshaft
- It is more effective.
- The crankshaft ensures the smooth operation of an engine.
- It offers more torque.
- By using this, engine power is increased.
Disadvantages of Crankshaft
- Bearings can fail.
- The overall cost of production is high.
- The crankshaft heats up as a result of the increased friction.
Applications of Crankshaft
The crankshaft is commonly used in an engine for converting the reciprocating motion into a circular motion, making the use of energy or power much easier.
A crankshaft is the heart of the internal combustion engine. The crankshaft is liable for the proper operation of the engine. In some circumstances, it also saves energy to move the piston for compression, suction, and exhaust strokes.
Wrapping it up
A balanced crankshaft can keep your engine running smoothly, provide more power, less waste of energy, and reduce engine vibration. It is mainly employed to convert linear motion to rotational speed.
I hope that I have covered everything about crankshafts. If you have any doubts about this article on “crankshaft parts and function” you can ask in the comments. If you liked this article, please share it with your friends.
Finally, Subscribe to our newsletter to get a notification when we upload the latest posts.
You can download this article in a PDF file by clicking here.
Read More In Our Blog:
- Engine Valves: Types, Working and Valve Mechanism
- What are the types of Gaskets? And Its Uses in Car Engine
- Three Major Types of Governors Used in Automobile Engine
FAQ
The crankshaft is a crucial part of the power transmission system. In this, the reciprocating motion of the piston is turned into rotational motion by applying a connecting rod. The crankshaft must have high fatigue strength and wear resistance to ensure a long life.
The crankshaft is mostly used in an engine for transforming the reciprocating motion into a circular motion, making the use of energy or power much easier. It rotates inside the engine block by the use of main bearings.
A crank is an arm attached at a right angle to a rotating shaft by which circular motion is received from the shaft. When it is used with a connecting rod, it converts circular motion into reciprocating motion or vice versa.
Following are the main types of crankshaft: Fully built shaft, semi-built shaft, Welded shafts, Solid single piece shaft, Forged crankshaft, Cast crankshaft, and Billet crankshaft.
Very informative
Thank you.
Wow. Very clear explanation of the various parts and manufacturing processes. Very helpful to a fellow engineer (HVAC) just learning about the internals of engines. Thank you very much for making this available.
You’re most welcome.
Thank you for this information. It is really helpful ,l appreciate it .You have my gratitude and honor ,once more thank you
You’re welcome and thanks for reading
Everything explained is perfect, thank you…
You’re welcome