In this article, you will learn what is brazing and soldering? Their advantages, disadvantages, and difference are explained with Pictures.
If you need a PDF file? Just download it at the end of the article.
Introduction
One of several techniques used to join two or more pieces of metal is soldering and brazing. Metal joints are made by hot-gluing two or more metal alloys together. In this case, gluing does not mean simply attaching items together, as the joint will be bonded molecularly to the alloy, increasing its strength.
Only brazing and soldering are able to produce fillets at the edges of metal joints that are smooth and shaped. In both procedures, the joint surfaces and filler metal are heated above room temperature.
The only real difference between the two metal joining methods is the temperature at which they are carried out. Unlike solder filler metals, which melt below 450 °C, brazing filler metals melt above this temperature. Here, we will discuss them in more detail.
Read More: 12 Types of Welding Processes & Their Applications [Full Guide]
What is Brazing?
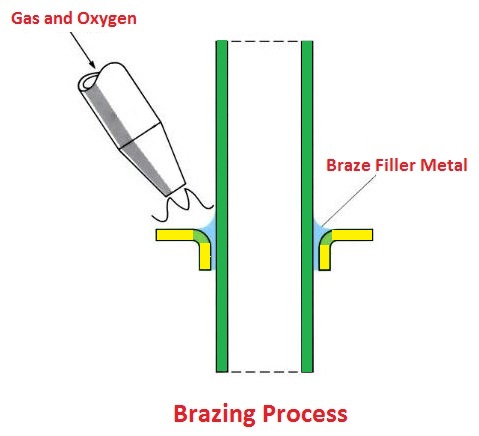
Combining two or more metal pieces together by heating them to a temperature higher than their melting point but lower than the melting point of the base metal is known as brazing. Then, a brazing alloy or filler metal is heated and melted.
By way of capillary action, this flows into the seam where the two metal pieces meet. This process is generally used for materials, including metals, ceramics, glasses, plastic, and composite materials.
This method of metal bonding is stronger than fusion welding but does not melt the parent metal of the components being joined. Therefore, this process requires more heat input than other soldering operations like mechanical fastening, adhesive bonding, solid-state joining, welding, etc.
It is frequently used in plumbing and metalworking applications, as well as in the manufacturing sectors of aerospace, automotive, and HVAC (heating, ventilation, and air conditioning).
Compared to other joining techniques like soldering, brazing has a number of advantages. In addition to joining dissimilar metals with different melting points, it can produce a strong, leak-proof joint and a tidy, attractive finish. If necessary, brazed joints can also be easily disassembled without causing any harm to the individual parts.
Read Also: Types of Welding Rods and Their Uses [Explained in Detail]
Advantages of Brazing
- This process requires less energy and heat to complete.
- This process can join dissimilar metals, including metals with different melting points.
- Brazing is a quick and affordable process for high-volume production because it can be automated.
- It enables the joining of delicate or fragile parts that other joining processes might break.
- In order to increase component life and decrease waste, brazing can be used to repair worn or damaged parts.
Disadvantages of Brazing
- Brazed joints are less strong, which makes them potentially unsuitable for high-stress applications.
- The risk of uneven heat distribution makes it unsuitable for joining very thick metal parts.
- Because brazing requires a certain level of expertise and experience to produce good results, labor and training costs may rise.
- Some joints may not be suitable, particularly those with complicated shapes or tight tolerances.
- Due to the cost of the filler metal and the requirement for specialized equipment, brazing can be more expensive than other joining methods.
Read Also: 9 Fundamental Properties of Steel [with Definition & Characteristics]
What is Soldering?
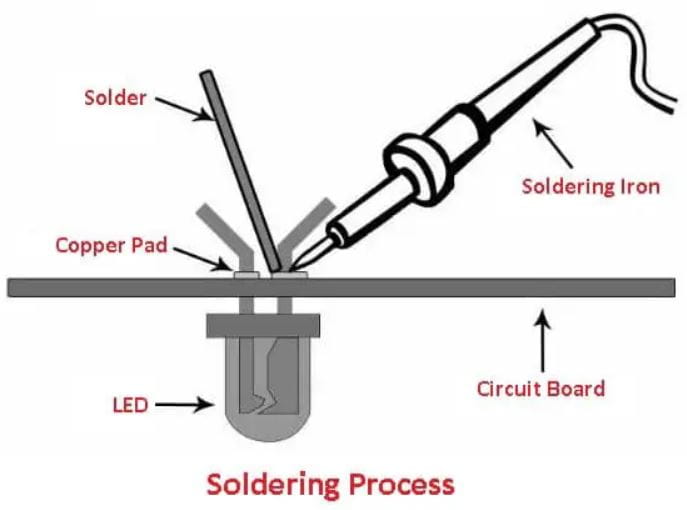
When two or more metal parts are heated to a temperature where a filler metal known as the solder melts and flows into the joint, creating a strong mechanical and electrical connection, this process is known as soldering.
A soldering iron melts the filler metal (solder) at a low temperature of up to 450°C. Since the filler metals melt at low temperatures, heat damage to delicate parts and part distortion are minimized. When solder solidifies, it bonds to the metal parts to join them.
Lead and tin alloy solder is the most popular type. In the electronics sector, soldering is widely used to connect wires, capacitors, resistors, and other components to the joining plate. It is also applied in plumbing, jewelry-making, and other metalworking processes.
The process of soldering differs from that of welding, which involves melting the base metal to create a fusion. Soldering is frequently chosen because of its adaptability to joining various metals and suitability for delicate work.
Read Also: What are the Different Types of Fasteners used today?
Advantages of Soldering
- For use in electronic circuits, soldering produces a solid, reliable bond between metal components.
- Soldering is appropriate for delicate or heat-sensitive materials because it uses a lower temperature.
- Different metals, wires, and light components can all be joined using soldering.
- Soldering is a quick and effective process that is economical for mass production.
- Soldering is a safer option than other kinds of metal joining processes because it doesn’t produce radiation.
Disadvantages of Soldering
- The strength of soldered joints is typically lower than that of other types of joints.
- Beginners may find soldering challenging because it calls for a specific level of training, knowledge, and equipment.
- Due to the solder’s low melting point, soldering is not recommended at high temperatures.
- Soldering cannot be performed on heavy metals.
- Inadequate heating could result in gaps or deformities in the solder.
Read Also: 16 Types of Welding Defects That Occur in Welding [Full Guide]
Difference Between Brazing and Soldering
While two or more metal parts can be joined using brazing and soldering, there are some significant differences between the two processes.
The following are the main differences between brazing and soldering:
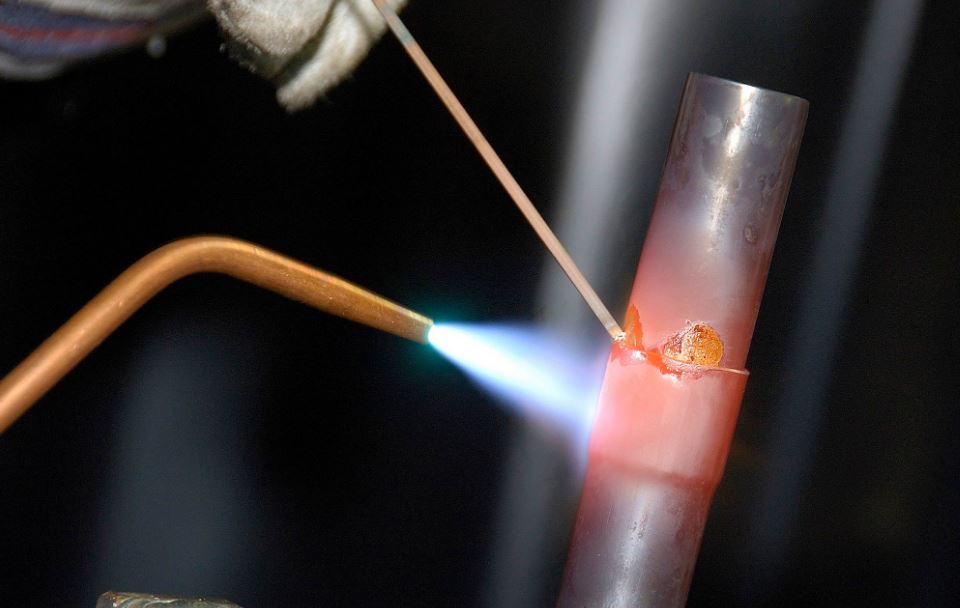
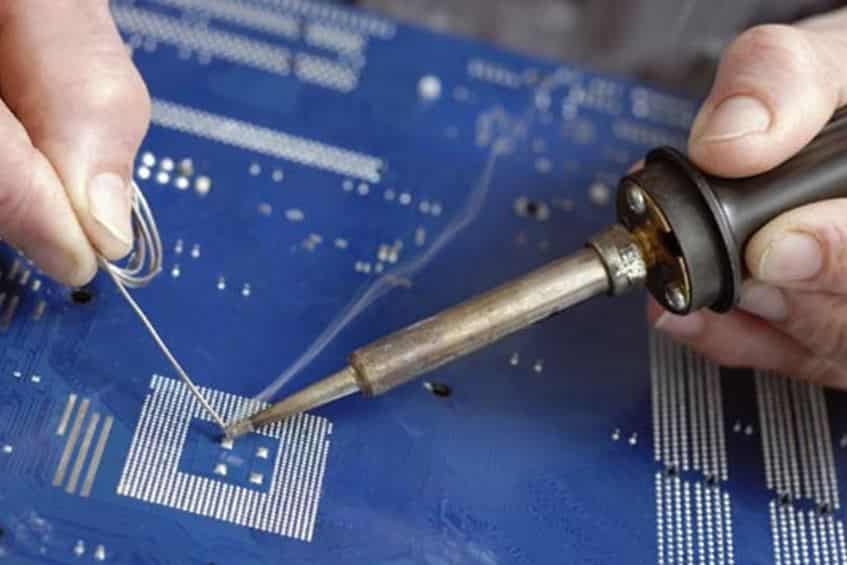
#1 Terminology
Brazing and soldering are methods for joining metals that are similar or dissimilar, but they are used in various joining conditions.
In the brazing process, a metallic filler that has been melted and poured into the joint is used to join two pieces of metal together. In soldering, a filler metal known as solder is also used to fill the joint, creating an alloy at the metal’s surface without melting the base metal.
#2 Temperature
The temperatures used for brazing are similar to the fusion temperatures used for welding. The main difference between these two metal joining techniques is the temperature at which they are conducted.
Brazing involves heating the filler metal to temperatures above 450°C (840°F). On the other hand, the soldering process uses filler alloys with melting temperatures below 450 °C (840 °F).
#3 Strength
Joints that are brazed together tend to be stronger than joints that are soldered together. As a result of the brazing process’s higher temperature, the filler metal and the components being joined can form a stronger metallurgical bond.
#4 Clearance
Soldering requires a smaller clearance between the metal parts being joined than brazing, which requires a greater clearance. It’s because brazing requires a higher temperature, which can cause the metal components to expand and contract. As a result, there needs to be a wider opening to allow for the movement.
#5 Surface Preparation
It is common for brazing to require a greater amount of surface preparation compared to soldering. To encourage strong adhesion of the filler metal, the metal surfaces that are being joined must be cleaned and roughened.
#6 Cost
The price of brazing is generally higher than that of soldering, as the higher temperatures, specialized equipment, and materials needed for brazing make the process more expensive.
#7 Application
In the electronic industry, soldering is the process that is most frequently used to create a long-lasting connection between electronic components. It is frequently used in plumbing, electronics, crafts, engine repairs, and metalworking—from jewelry to flashing. The soldering technique connects wires to leads on switches and other components.
Flux is used in brazing to facilitate wetting and remove oxides from the base material. This improves the bond between the filler metal and the metal components. Except for aluminum and magnesium, all types of metals are typically joined using the brazing process. Besides that, automobile manufacturers use it.
Read Also: Mechanical Properties That Every Mechanical Engg Should Know
Brazing vs. Soldering: What’s the Best?
According to the particular application and requirements, brazing or soldering is best. The choice between brazing and soldering will depend on a number of factors, including the metals being joined, the strength required, the temperature and environment, and the project’s budget and time constraints.
Applications like aerospace and automotive manufacturing, which call for a very strong joint, high-temperature resistance, and good mechanical properties, usually prefer brazing. Brazing is more expensive and time-consuming than soldering. Because, it calls for higher temperatures, precise clearance between the parts, and specialized equipment.
Soldering is typically preferred for applications requiring lower temperatures, lower strength joints, and greater versatility, such as electronics, jewelry making, and plumbing. Compared to brazing, soldering is simpler, quicker, and can join a wider variety of materials, including delicate parts and metals of different alloys.
So, brazing or soldering are equal in terms of their merits – the best choice is based on the specific application and requirements.
Closing It Up
That’s it. Thanks for reading. I hope I have covered everything about the “Difference Between Brazing and Soldering.” It would be helpful if you could let me know if there was anything I missed or if you have any doubts about anything I wrote. Please share this article with your friends if you find it interesting.
Want free PDFs direct to your inbox? Then subscribe to our newsletter.
Download the PDF of this article:
In our blog, you might be interested in reading more:
Hello, how come the pdfs are not downloadable
I sent you a PDF file of this article. Please check your inbox.
Thanks for another great article Yousef.
Unfortunately, the link for the PDF is not working.
Thanks for letting me know about the PDF link. I have updated the article with a new PDF link. Now you can download it.