In this article, you will learn what are different Lathe Attachments and Accessories for lathe machine and also you can download the PDF file of this article at the end.
Lathe Machine
A lathe is a machine that holds the workpiece on a chuck and tool on a toolpost, the lathe machine rotates the workpiece about an axis to perform different lathe operations such as turning, facing, chamfering, thread cutting, knurling, drilling and more with tools that are applied to the workpiece to design an object with symmetry about that axis.
Read more on: 22 Different Types of Lathe Operations
Lathe Accessories
The following are the different lathe accessories:
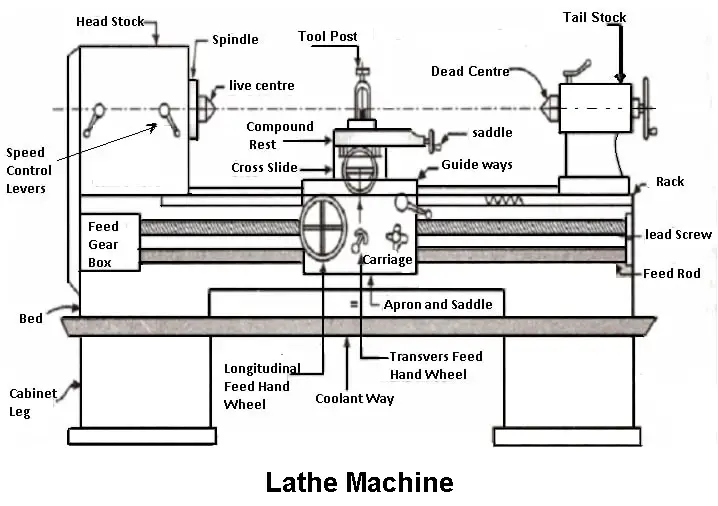
- Centres
- Chuck
- Catch plate or carriage
- Face plate
- Angle plate
- Mandrel
- Rests
Lathe Attachments
Following are the 5 different types of lathe attachments:
- Taper Turning attachments
- Grinding attachments
- Gear cutting attachments
- Milling attachment
- Thread chasing dials
Centres
The most common methods of holding the workpiece in a lathe are between the two centres i.e. live centre and dead centre. The different types of centres are used for different types of workpieces and also for specific purposes. The important types of centres used as shown in the figure below.
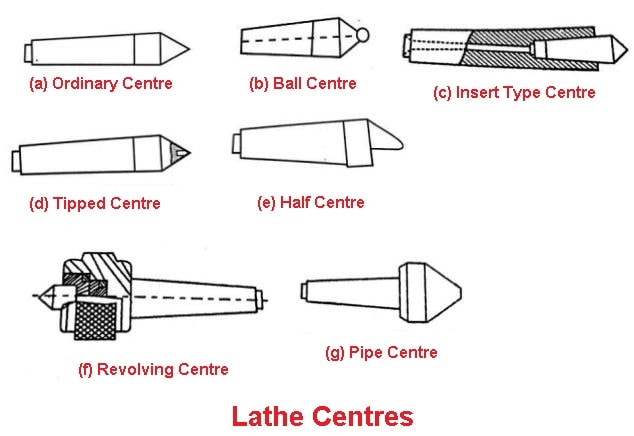
1. Ordinary Centre
This type of centre is used for general purposes and for small operations.
2. Tipped Centre
This is very important of all other centres and here the tip is made of hard material. These hard materials will resist deflection, wear, and tear.
3. Ball Centre
This type of centre is used to minimize wear and strain while taper turning by set over method.
4. Insert Type Centre
This type of centre is used for the economic purpose and here we can replace only the high-speed steel “insert”, instead of replacing the whole centre.
5. Half Centre
This is very similar to ordinary centre expect that little, less than half of the centre has been grounded away.
6. Pipe Centre
The pipe centres are used for supporting the open end of pipes. They are commonly used in production works.
7. Frictionless Centre
This is used in the tailstock, it has the capacity of bearing high-applied force and this can rotate the centre along with the job or workpiece. This can operate at very high speed.
The centres mentioned above will withstand the higher temperature during the working and the centres h=generally have an included angle ranging from 60° to 75°.
Read Also: 14 Different Types of Lathe Cutting Tools
Chucks
Chucks are genrally used to support and hold the workpiece in order to carry out different operations in lathe. The different types of chucks are as follows
- 3 jaw universal chuck
- 4 jaw independent chuck
- Combination chuck
- Magnetic chuck
- Collet chuck
Now let us discuss some of the important chucks briefly.
1. 3 Jaw Universal Chuck
The 3 jaws, which are generally made of high quality steel, are arrogated at an angle of 120° to each other. During the operation, the jaw teeth are made to mesh with scrawl spiral teeth (Bevel’s teeth).
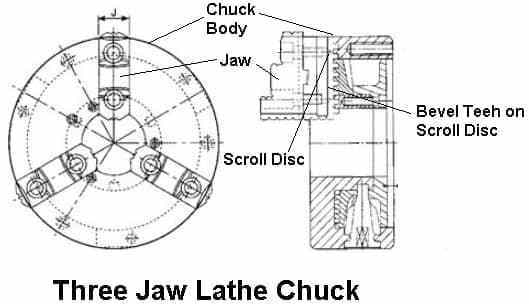
The meshing causes a moment of all 3 jaws either towards or away from the chuck centre, depending upon the direction of rotation of bevel pinion. The pinion is performed by square end key “chuck key”. 3 jaw universal chucks are used for workpieces of circular and hexagonal shapes.
2. 4 Jaw Independent Chuck
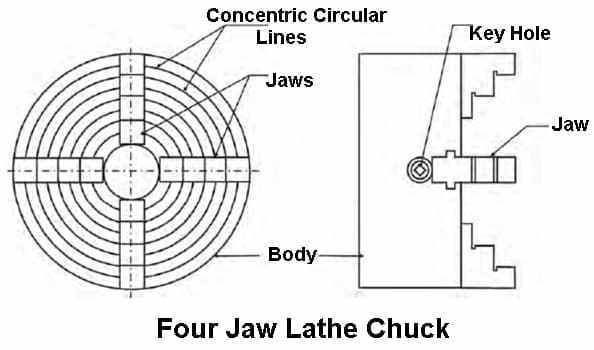
The arrangement of 4 jaw independent chuck, which has 4 jaws, located at an angle of 90° to each other. Here all the four jaws are operated independently with 4 screws in place of scroll disk used in 3 jaw chuck. Hence it is called as 4 jaw independent chuck. This type of chuck is generally used to hold irregularly shaped workpieces.
3. Combination Chuck
The arrangement of combination chuck, which combines the characters of universal chuck and independent chuck. This type of chuck can be used either as self-centring chuck or an independent chuck.
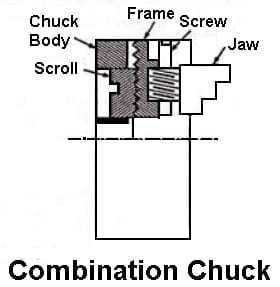
It has both the independent screws and the scroll disk. In this chuck, the jaws can be either moved separately by operating the screws or simultaneously by operating scroll disk. It can be used for regular as well as irregularly shaped workpieces.
Read Also: 7 Different Lathe Machine Chucks: It’s Parts, Working with [Images]
Catch Plates or Carriers
Carriers and catch plates are used to drive a workpiece when it is held between two centres. Carriers are driving dogs attached to the end of the workpiece by a setscrew. Catch plates are bolted to the nose of the head stock spindle.
A projecting pin from the catch plate or carrier fits into the slot provided in wither (anyone) of them. The projecting pin of a single pin catch plate drives the straight end or tail of the carrier attached to the workpiece.
Two pins of a double pin catch plate engage with the double tail or double slotted carrier and provide uniform drive. The bent tail type is used with a faceplate or slotted catch plate.
Face Plate
It is a circular plate threaded at its center with plain and T-slots which are machined rapidly. It is fitted to the lathe spindle with its central threaded portion. The job on the workpiece is held by the face plate using bolts and clamps in the slots.
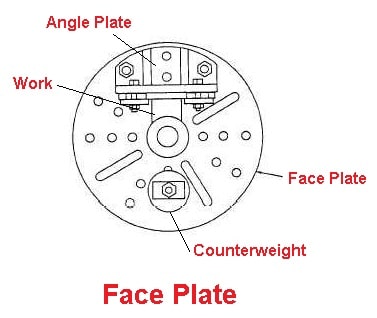
The faceplate is suitable to hold both regular and irregular shaped workpieces, which cannot be help conveniently by chucks or on centres.
Angle Plate
It is a cast iron plate with two faces that make them at exactly the right angle to each other. Holes and slots are provided on both the faces so that it may be clamped on a faceplate and can hold workpieces on the other face by bolts and clamps.
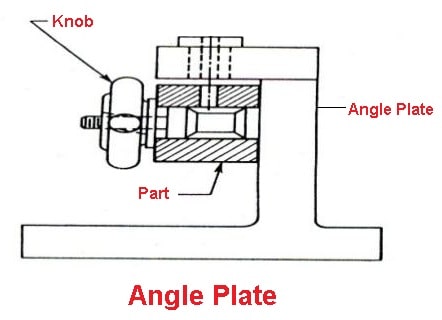
Angle plates are used with faceplate when the holding surface of the workpiece should be kept horizontal. For example, in machining, a flange of a pipe elbow this plate is used. When eccentric jobs are bolted to the faceplate, a balance weight or counterweight must be added.
Mandrels
The Mandrels are steel shapes that are useful for holding rotating previously drilled or stepped turned or bored workpieces, for further operations. Mandrels have got flattened ends for easy gripping by the carriers.
Different types of mandrels are used to suit the job or workpiece requirements. The commonly used mandrels are,
1. Plain Mandrel
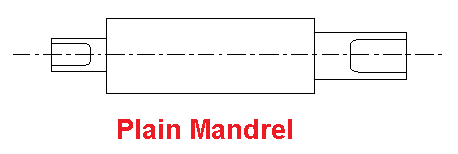
Whenever the parts of the workpiece are plain in nature, this type of mandrel is used.
2. Step Mandrel
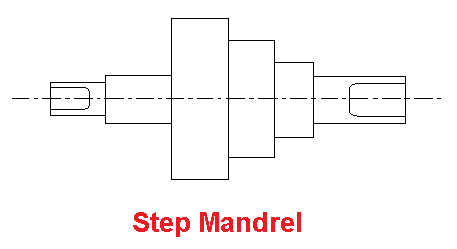
Whenever the inner portion of the workpiece is in the form of steps, in that case, to hold the workpiece rigidity, this type of mandrel is used.
3. Cone Mandrel
Whenever the part of the workpiece is conical in shape, in that case this type of madrel is used.
4. Screw Mandrel
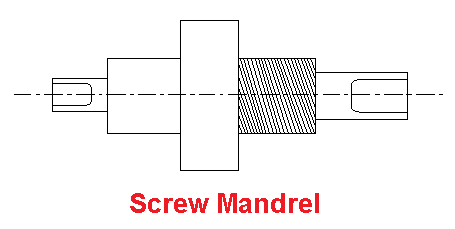
Whenever the inner part of the work piece is threaded, then this type of mandrel is used.
5. Gand Mandrel
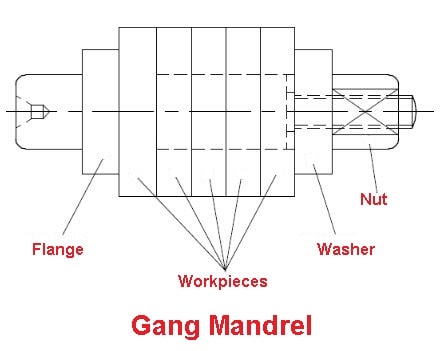
It has a fixed collar at one end and movable collar at the other end, which is threaded in nature. This type of mandrel is used for holding a set of hollow workpieces between the two collars of which one is fixed and other is movable.
Rests
It is a supporting structure used in the lathe to support long jobs or workpieces. It is located in the intermediate position between the centres. This prevents bending of the workpiece or job due to its own weight and vibration. It is used the length is 10-12 times the diameter of the workpiece.
1. Steady Rest
It is a cast-iron structure with machined base, which can slide on lathe ed base. It can be clamped like a tailstock in any position between the centres and support workpiece. The upper semicircular body of the steady rest is hinged, so as to move the job or the workpiece without completely removing the rust.
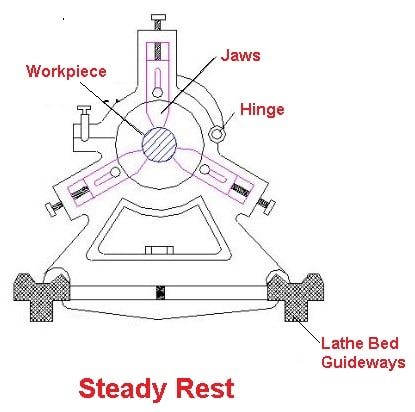
The steady rest has got 3 screw type jaws which are placed at an angle of 120° to each other. These screw type jaws can be radially moved to support and hold the job. If the length of the workpiece is too high, one more steady rest can be used.
In addition, to supporting the workpiece or the job between the centres, rest can also be used to support the free end of a job during operations like drilling, reaming, boring, and tapping.
2. Follower Rest
It is a C-shaped cast iron structure having 2 adjustable jaws. The follow rest is fastened to the lathe carriage and moves along with it. The function of a follow rest is to support the job in such a way that it prevents deflection of the job when cutting action takes place.
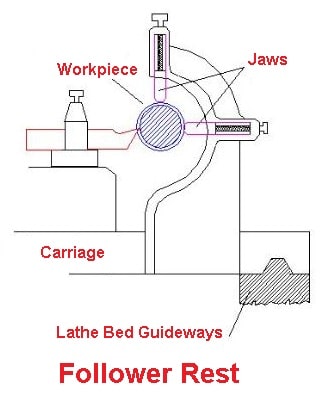
Initially, a portion of the job is machined and the follow rest is set so that it provides the bearing support. The tool is set slightly in advanced position than the jaws so that the jaws always move on the machined surface and provide continuous bearing support to the job. This type of rest is used generally for finished turning operations.
Taper Turning Lathe Attachments
Many modern lathes have a taper bar behind the bed. The spindle can be set at different angles to the spindle. The bar has a sliding block that, during taper turns, is attached by a link behind the cross-slide. The lead screw of the cross-slide is delivered so that it does not control the setting of the depth of cut and the slide is now independent.
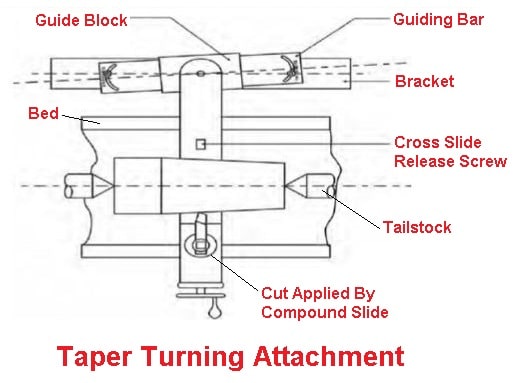
When the saddle is pushed along the bed, the cross-slide follows the taper bar, so that the tool travels parallel to the bar and a taper is obtained. The top slide is rotated by 90° at right angles to work so that it can be used to utilise the depth of cut.
Grinding Lathe Attachments
The lathe can be used for re-sharpening millers and milling cutters, for grinding hard bushes and shafts, and many other grinding operations, with the help of a good electric grinding attachment. V bed ways of lathe bed must be covered with thick cloth or canvas to shield them from dust and grit from the grinding wheel, and lathe spindle bearings must also be protected.
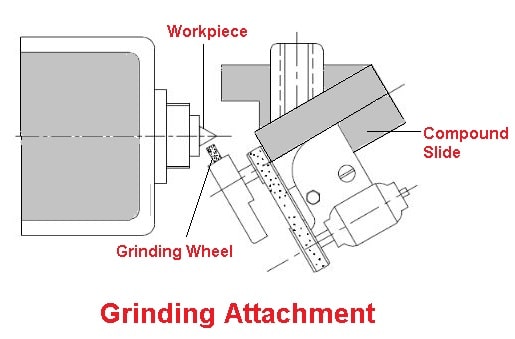
A large, powerful grinder is satisfactorily used for external grinding. The wheel must be 100 mm in diameter and the grinder must be located directly on the compound rest of the lathe.
Gear Cutting Lathe Attachments
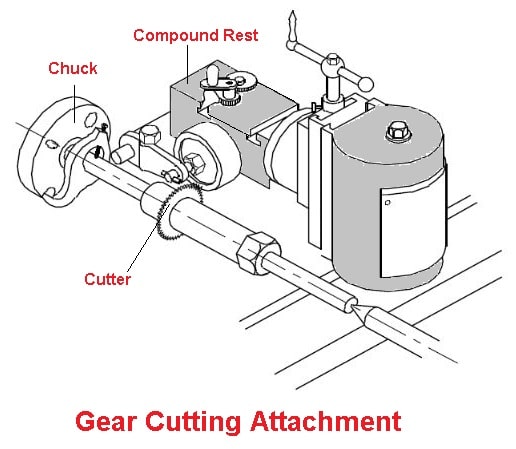
The gear cutting attachment on the lathe will cut the spur and bevel gears. It may also be possible to perform linear indexing, external keyway cutting, splining, slotting, and all routine dividing head light milling tasks. This gear cutting attachment is very beneficial for cutting small gears and for light machining.
Milling Lathe Attachments
This attachment is mounted on a cross-slide of a lathe in place of compound rest. The milling attachment works at right angles to the milling cutter, which is fastened to the chuck or collet. The milling cutter and the indexing head are attached on the compound rest.
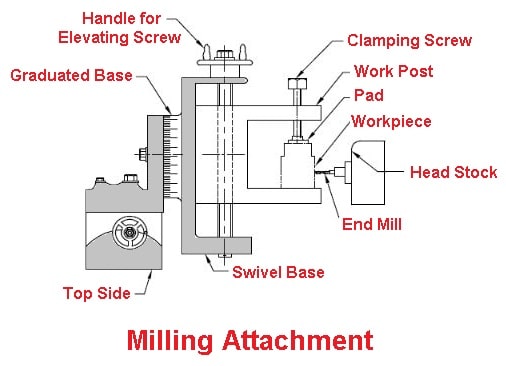
Both of these attachments have provisions for feeding in all three directions, and therefore, it is possible to conduct operations such as keyway cutting, angular milling, T-slot slots and thread milling, etc.
Thread Chasing Dials
The side of the cut threads on a lathe and lathe spindle with lead screw is in the same virtual space for every successive cut. The majority of lathe also has a thread chase dial, which is fixed or attached to the carriage for this reason.
Changing the dial indicates that the split nut should be occupied by a lead screw to follow before the cut grooves. The thread chasing dial is connected to a worm gear, which is meshed by threads of lead screws.
Conclusion
So far we have discussed everything about “lathe attachments and their accessories” if you miss something please let us know in the comments section.
That’s it, Thanks for reading. If you find this article helpful share this with your friends. Have any questions about this topic ask in the comments I’ll respond to you.
Subscribe to our newsletter to get notified when we upload new articles. It’s totally free!
Download PDF of this article:
Read Next:
You can read about every machine in manufacturing technology from here
I loved your blog and thanks for publishing this are the advantages of stainless steel for fabrication projects. I am really happy to come across this exceptionally well-written content. Thanks for sharing and look for more in the future!!
I’m glad you liked our article, thanks for reading and keep visiting.
cant find the pdf link
Hi there! Now you can download the PDF of this article. Thanks for reading.
Sir,
In your engineer’s post you have mentioned chucks, centres, rests, mandrels, catch plates, face plates, angle plates, etc. as attachments. But, in actual these are accessories. The work of accessories is different from that of attachments. In a lathe machine accessories are used to hold, rotate and/or support the workpiece, where as attachments are used to enhance the working capacity of the lathe machine. Hence, it is a humble request to mention chucks, centres, rests, mandrels, catch plates, face plates, angle plates, etc. as accessories.
Thanks for you helpful comment. We updated that article please checkout.