In this article, you’ll learn what is rivet and riveted joint? how to use rivets, methods, types of rivets, applications, advantages, and disadvantages.
And also you can download the pdf file of this article at the end.
What is a Rivet?
The riveted joint is a permanent joint cause rivet is a permanent mechanical fastener. A rivet is a cylindrical shaft with a head on one end and the opposite end known as a tail.
Rivets are generally made of mild steel, but at times they are also made of brass, copper, aluminum, etc. These types of fasteners are generally used in structures, bridges, sheet metal operations, ships, and many industries.
Read Also: Different Types of Marking Tools & Their Uses [Names & Pictures]
Parts of a Rivet
Following are the parts of a Rivet:
- Head
- Shank and Body
- Tail
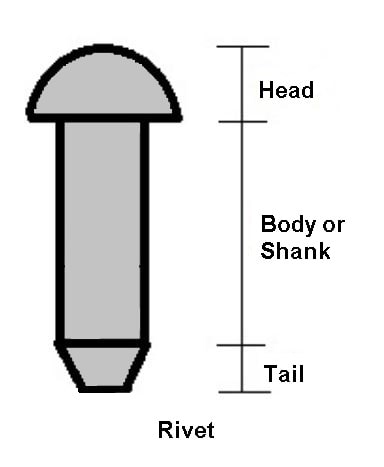
#1 Head
The uppermost part of the rivet is called the “head.” These are made of different types according to different jobs.
#2 Shank and Body
The part below the rivet is called the shank or body. This is round in shape.
#3 Tail
The part below its center is called the tail. It is somewhat tapered. It is inserted into holes of two plates, and the head is made by beating its tail. The length of the tail is ¼ D. A rivet is known by its roundness, length, and shape of the head.
Read Also: Essential Types of Electrician Tools [Names & Uses] Explained
How Does A Rivet Work?
In the construction of machines and structures, rivets are very important fasteners. You can attach rivets by drilling, punching, or by inserting them into a hole and distorting the tail. The most common riveting method involves drilling a hole in the component that will be riveted. This is so that it can be more widely used and is much simpler.
To better secure the rivet, it fits in a hole that is drilled about 1.5 mm larger than the rivet’s actual diameter. Once the rivet is in place, the tail appears at the other end with a deformed shape. It is common for the tail of the rivet to unfold or spread when you pound or smash it.
It will increase in size by about 1.5 times its original size. If you pound or pull the tail flat on one end and make a new head on the other end, you can create a dumbbell-sized rivet. The tail then takes the shape of a dumbbell. The joint has been riveted in this manner.
Read Also: 25 Different Types of Nails and Their Uses [Explained in Detail]
Types of Rivets
There are various types of rivets, including
- Solid rivets
- Blind rivets
- Drive rivets
- Tubular rivets
- Split rivets
- Flush rivets
- Cherry rivets
- Self-piercing rivets
#1 Solid Rivets
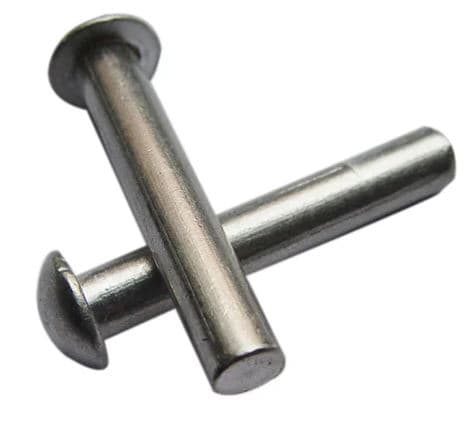
These rivets are made of a single piece of metal and are the most popular type. They are the simplest, most reliable, and oldest types of rivets. Solid rivets are made up of just a shaft and head, which are bent with a hammer or rivet gun. A rivet gun or hammer is used to deform the headless portion on the other end.
These rivets can have either round universal heads or heads that are countersunk by 100°. When dependability and safety are crucial, solid rivets are frequently used. They are employed in numerous fields, including the manufacture of ships, aircraft, and structural steel.
#2 Blind Rivets
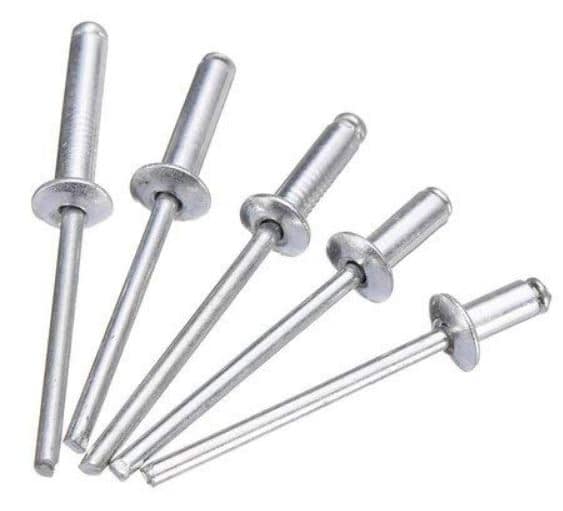
Blind rivets, also called pop rivets, are used when there is limited access to one side of the joint. They are made of a hollow tube with an internal mandrel that expands when pulled to form a robust joint. To join parts together, manufacturers drill holes in the components and insert blind rivets there.
The mandrel breaks off when the blind end of the rivets expands. Blind rivets can be installed in joints from one side of the part, unlike solid rivets. They become “blind” to the opposing side in this way. It is comparatively simple and quick to apply, just like any other rivet. In the fields of shipbuilding, electronics, and aerospace, it is the most powerful joint.
Several of the typical blind rivets in use are:
- Pull-Mandrel Rivets: In their applications, these unique double countersunk blind rivets offer flush surface tightness on both sides. Here, the clamping force is constant because the mandrel head does not separate.
- Threaded Rivets: These types of rivets have an internal thread and are entirely anchored on one side. These are also known as threaded inserts. Originally, these were used to fasten deicing boots to aircraft wings.
#3 Drive Rivets
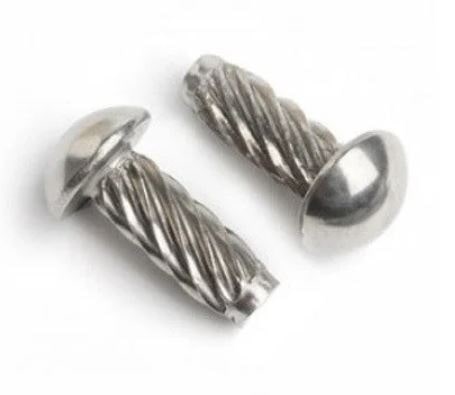
They are also referred to as hammer rivets. Drive rivets are a particular type of blind rivet with a short mandrel sticking out of the head. Drive rivets are more frequently used in applications that are intended to be aesthetically pleasing, such as architecture and other fields.
They are also utilized when a strong joint is needed, but access to one side of the joint is restricted. They do not have as strong of a clamping force as many other types of rivets.
#4 Tubular Rivets
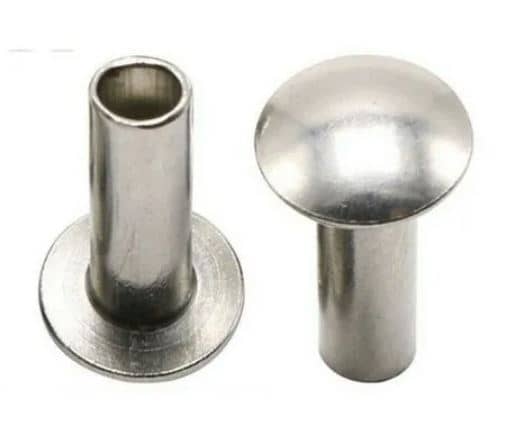
These resemble solid rivets but differ in having a hollow center. The standard tubular rivet has a hollow end and a manufactured head on opposite sides. For joining, the hollow end protrudes through each piece.
These types of rivets must be extremely ductile and made of low-strength metals because they must undergo extensive cold forming. As a result, tubular rivets are widely used in industrial settings. They are often used in applications that call for a permanent joint, such as leatherworking.
These are a few of the various types of tubular rivets:
- Compression Tubular Rivets: These rivets are made of two parts that interfere with one another when they are being fastened. Their commercial application involves soft materials and calls for aesthetics on both sides of the component.
- Semi-Tubular Rivets: These rivets have holes on the field end. Typically, the hole depth is 1.12 times the diameter of the shank. As a result, when the field head is formed, the semi-tubular rivet might feel solid.
- Full Tubular Rivets: These rivets have deeper holes than their counterparts. They typically have lower strength than semi-tubular rivets. Even so, softer materials like fabric and plastic are easily penetrated by them.
#5 Split Rivets
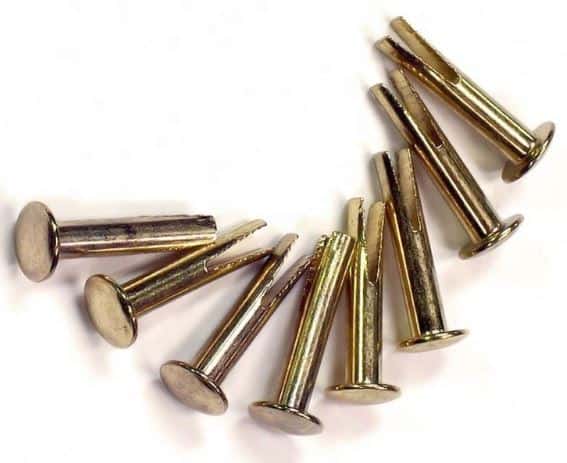
Split rivets are formed by cutting a single piece of metal into two pieces. These two pieces are then joined by putting them through a hole already drilled. For joining softer materials like leather, plastic, and wood, they are the best options.
For use in home repairs, split rivets come in sawed or split body varieties. Additionally, they have pointed ends or tips that can pierce the materials themselves. They should not be used in demanding or crucial situations. They are used when a flexible joint is necessary, like making leather goods.
#6 Flush Rivet
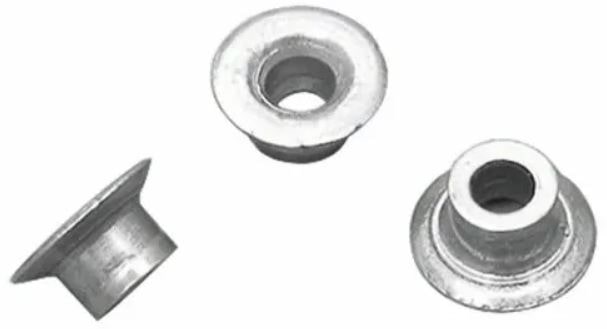
Like solid rivets, flush rivets differ because their flat head is flush with the surface of the material they are joining. For external surfaces, flush rivets—also known as countersunk rivets—are used to maintain aesthetic appeal and reduce aerodynamic drag.
This is because it employs both heads and countersunk holes. On the outside of an aircraft, flush rivets are useful for aerodynamic reasons that reduce drag and turbulence. Along with automotive and marine applications, they are frequently used in aircraft construction.
#7 Cherry Rivets
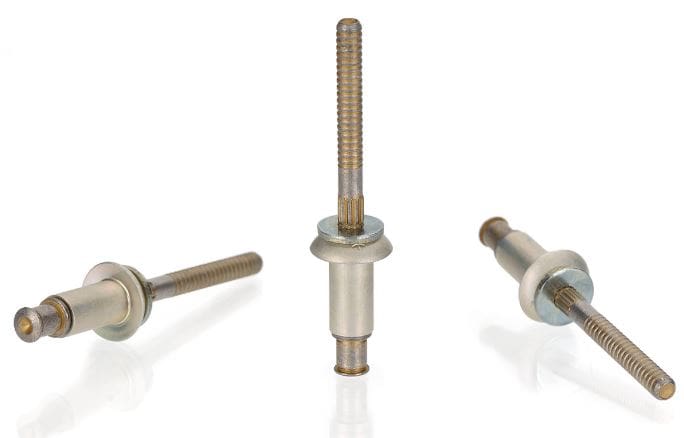
This type of rivet is also known as a pull-through rivet and consists of a metal sleeve with a flared end and is pulled through a pre-drilled hole with a special tool. There are two main applications for cherry rivets, namely aerospace and automotive, in which a strong, permanent connection must be provided.
#8 Self-piercing Rivets
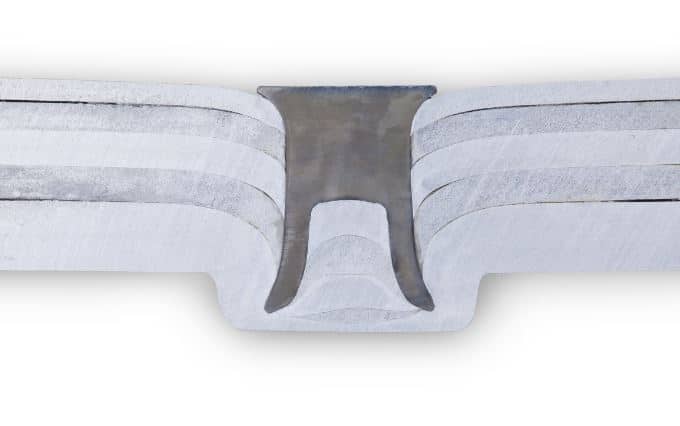
It is not necessary to drill or punch holes before using this type of rivet. This is because the end of these rivets has a bevel drill or chamfered poke to pierce the involved components.
Self-piercing rivets produce a gas-tight or water-tight joint by piercing through the top layer of the material while leaving the bottom layer only partially pierced. The rivet’s tail flares and interlocks with the bottom sheet due to an upsetting die, forming a low-profile button.
Read Also: 16 Types of Measuring Tools and Their Uses [You Must Know]
Materials used in Rivets
For the production of rivets, several types of metals are available. They consist of stainless steel, copper, brass, aluminum, and steel. To meet their needs, manufacturers and designers pick these various materials.
#1 Steel
Applications involving rivets benefit from the use of low-carbon steels. This is because it can secure or fit tightly in its application. Additionally, compared to rigid high-carbon steel rivets, it is much more adaptable and flexible. High carbon steels have a lower moldability and require more material to produce rivets.
#2 Stainless Steel
The stainless steel rivets are highly tough, durable, and deterioration-resistant. These rivets are used in the aircraft, power generation, and locomotive industries. Due to their ability to resist corrosion, these stainless rivets are widely used.
#3 Aluminum
The malleability and lightness of aluminum are well-known qualities. Aluminum is a versatile material that offers a high level of deterioration resistance. Additionally, because aluminum is so malleable, it makes it simple to design complex part layouts.
#4 Copper
In terms of appearance and use, copper is a flexible material. It is extremely effective at transferring heat and electricity. Because copper is such a good conductor of electricity, copper rivets are frequently used in electrical and plumbing appliances.
#5 Brass
Brass is a soft, flexible, and low-friction material. Brass cannot produce sparks because of its characteristics. Brass rivets are the type that works best with gas appliances due to these characteristics.
Read Also: Different Types of Clamps & Their Uses [How To Use Guide]
Methods of Riveting
Riveting is carried out with the help of dies and backup dies that place a rivet in between them and, by the use of force, the rivet is set into parts to join.
The equal and opposite force distorts the rivet and the tail section of the rivet is turned to head downwards, so the entire rivet sits on the plates. In this process, the rivet’s tail is transformed into a ‘head’ sometimes called a ‘shop head’.
To join the riveting parts, they are drilled with the help of a drilling machine. Clearance is noted when riveting because the diameter of the rivet increases to some extent by pressing.
Normally clearance is considered as per the following:
- If the diameter of the rivet is, d = 12 to 24 mm, then Clearance is taken as, C = 1.5 mm
- If the diameter of the rivet is, d = 24 to 48 mm, then Clearance is taken as, C = 2 mm
Read Also: Different Types of Welding Joints (Explained in Detail) PDF
Application of Rivet Joints
Rivets are used in many industries to secure or unite two or more wooden or metallic elements. They allow items to be joined more rigidly and are typically larger than screws of equivalent diameter.
Some applications for rivets are as follows:
Rivets in Aircraft
In aircraft, manufacturers often use robust, long-lasting, and reliable materials while machining different projects. Thus, riveting is a key method in aircraft construction since it allows for solid alignment and the formation of solid pieces.
Rivets in Construction
Rivets are most commonly used in the building industry for their high level of efficiency. They are strong fasteners that make it easier to attach different parts of a construction or machine.
Rivets in Jewelry
Professional jewelry manufacturers use riveting as a cold joining technique in their different activities. Jewelry makers use riveting to effectively complete cold connections with a few common tools, specialized training videos, and basic metal forming capabilities.
Rivets in the Automotive Industry
In the automotive industry, rivets are used to assemble chassis components, body panels, and several other parts. It is typically used for fastening materials of different characteristics, such as steel and aluminum.
Advantages of Rivet joints
The following are the advantages of rivet joints:
- The fabrication cost of the riveting process is cheaper.
- Dissimilar metals can also be added. Even non-metallic joints are also done with riveted joints.
- The riveting process requires low maintenance costs.
- The operation of the riveting process is easy.
Disadvantages of Rivet Joints
The following are the disadvantages of rivet joints:
- It requires skilled workers to do the riveting process.
- Leakage can be a problem for these types of joints but is overcome by special techniques.
Closing It Up
That’s it. Thanks for reading. I hope you like our article on “types of rivets.” If yes, please share it with your friends. If you have any doubts, you can ask us in the comments.
Download the PDF file of this article by clicking below:
Subscribe to our newsletter for more articles like this
Read More articles:
- Vice: Types of vices, parts, how they work?
- Cams and followers: parts, types, application (PDF)
- Different types of washers; how and when to use them?
FAQs
Riveting is a forging method that involves joining parts together using a metal element known as a rivet. Through adjacent surfaces, the rivet serves to attach the pieces. A straight metal piece is connected through the parts. The components are then securely joined by forming both ends over the connection.
Stainless steel rivets are not only corrosion-resistant, but they are also extremely durable, strong, and resistant to deterioration. They can endure extreme temperatures and sustain their strength over long periods.
1/8th of an inch (that is 3175 in mm) is the most popular size for rivet diameters.
Some of the most popular, daily rivet applications are: Building and construction, Transportation and infrastructure, Woodworking and decorative finishing, Fine metalwork and jewelry, Aviation, Aerospace, and Automotive.
Your generosity in sharing this valuable knowledge is truly commendable. It’s like discovering a treasure trove of insights.
Thanks for your feedback.
Thank you for providing such a wealth of valuable information. It’s like discovering hidden treasure.
I’m glad it was helpful for you. You’re welcome.
it is very helpfull for me . i have tell my friends about this side . he said expantional and charming.
thank you a lot
You’re most welcome. I’m glad it was helpful for you.
I hate to be a pain but the picture for your flush rivet #6 is not the rivet but the rivet set tool used with a rivet gun to shoot the flush /countersunk rivet. Other then that mistake I really like the article there are also several different aluminums used to make the rivets we use i aviation structural repairs just so you know.
Thanks for letting me know about the mistake in the article’s image.
Hi There,
Thanks for sharing such an informative article with a clear explanation.
Keep Updating…
You’re welcome.
Excellent explanation 👍
I’m glad you liked it.